Manufacturing in Virginia
Virginia is currently home to 4,950 manufacturing companies employing 294,883 workers . According to the National Association of Manufacturers, Virginia manufacturing accounted for 8.30% of the total output in the state, employing 5.98% of the workforce. Total output from manufacturing was $49.50 billion in 2021. In addition, there were an average of 239,000 manufacturing employees in Virginia in December 2021, with an average annual compensation of $79,114.61.
Virginia Shipbuilding and repair (not including public shipyards) was responsible for adding $10.9 billion to gross state product (GSP) in 2022 . Aerospace and defense manufacturing contributed about $8.85 billion to GSP in 2021.
Virginia’s non-military maritime industry was responsible for one in five jobs in Virginia and more than $8 billion in state and local taxes during fiscal 2022, according to a recent study conducted by William & Mary.
Defense Manufacturing in Virginia
The presence of DoD in Virginia has a high impact on the state’s economy and GDP. DoD spending per capita in Virginia is reportedly the highest in the nation. In Virginia, the defense industry generates over $103 billion in total economic impact and supports over 885,000 jobs across the state . Of that, military maritime production has a large influence on the commonwealth’s GSP.
Naval shipbuilding and repair
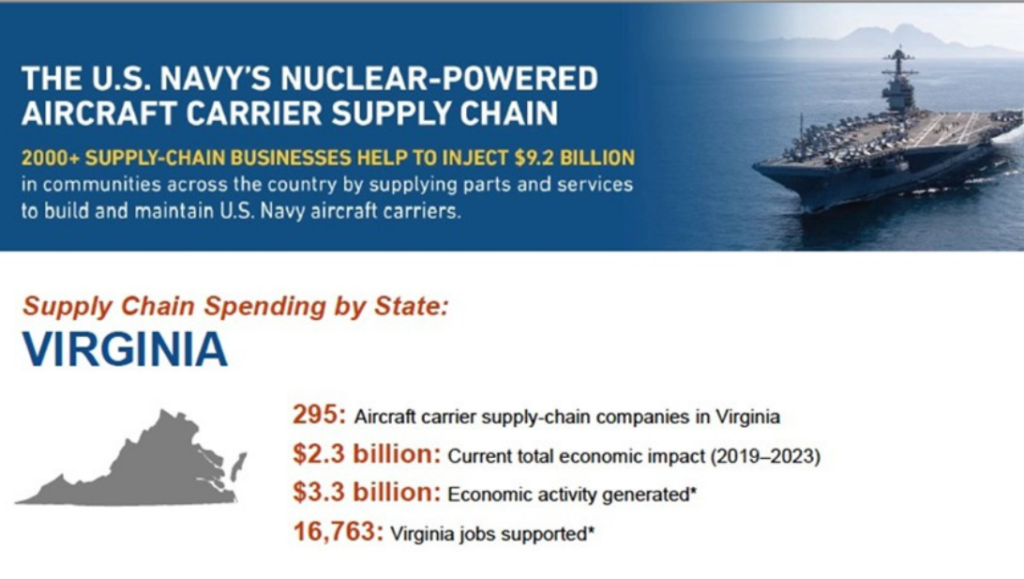
Hampton Roads is home to the largest Navy Base in the country and has over 16 bases surrounding the area. Every branch of the military has a presence in Hampton Roads, and the region’s 100,000 plus active-duty and reserve personnel is second only to the Pentagon. Additionally, over 40,000 civilian personnel are employed on military bases in Hampton Roads.
With reported average annual sales of $6.7 billion and employing 21,800, Huntington Ingalls Industries, the country’s largest private military shipbuilding and repair facility, is by far Virginia’s largest sole industrial employer.
According to the Submarine Industrial Base Council (SIBC), there are 278 submarine industrial base suppliers in Virginia, with $5.8 trillion in funding over the last 5 years , not including the 2 key submarine builders.
According to the Aircraft Carrier Industrial Base Coalition (ACIBC), there are 295 aircraft carrier supply-chain companies in Virginia, accounting for $2.3 billion total economic impact between 2019-2023, and generating $3.3 billion in economic activity and supporting 16,763 jobs.
DoD’s Need for Metal AM in Virginia
Delays in traditional parts fabrication
The National Defense Industrial Strategy (NDIS) document published in 2023 pointed out that manufacturing employment has decreased 36% in the US since 1979, a loss of 7.1 million workers. For the Defense Industrial Base the amount of people employed had dropped by 1.9 million, or 65%. During that period, significant amounts of manufacturing had been offshored driven by cost considerations, and, on shore, OEMs were disincentivized to modernize manufacturing processes or maintain excess capacity. This has resulted in DoD’s overreliance on single or adversarial foreign sources for key materials and production capacity and on supply chains that have proven fragile and vulnerable.
The plethora of challenges facing the DoD supply chains include (source: NDIS):
- Underutilization of Multi-Use (new and innovative) Technologies (such as AM)
- Inadequate Workforce lacking critical skills
- Inadequate Domestic Production:
- Non-Competitive Practices
- Long Lead Times and Sub-Par Readiness
- Fragility of Sub-Tier Suppliers
- Lack of Market Share, Over-Customization, and Obsolescence
- Instability of Procurement and uneven demand
- Outdated acquisition practices
- Funding Uncertainty and Constraints:
- Limited Visibility into International Ally and Partner Requirements
A symptom of the problem at hand is shown in the availability of replacement parts and maintenance delays in the US Navy’s submarine divisions.
The Chief of Naval Operations recently testified on submarine ship maintenance delays with average start-times delayed by 1-2 months and maintenance processes themselves extending an additional 3-4 months longer than expected, resulting in key submarines missing deployments or having them shortened. To mitigate further impacts in private shipyards, the Navy has accelerated awards of contract options and improved cash positions of the industrial base. However, the Congressional Budget Office (CBO) projects that the submarine fleet’s size will exceed Navy shipyards’ capacity to maintain it over the next several years. Shortages of parts are contributing to these maintenance delays. While unable to quantify the effect of those shortages on delays, CBO has highlighted a “cannibalization” rate whereby the Navy borrows parts from one ship to complete maintenance on another, causing readiness delays for the cannibalized ship.
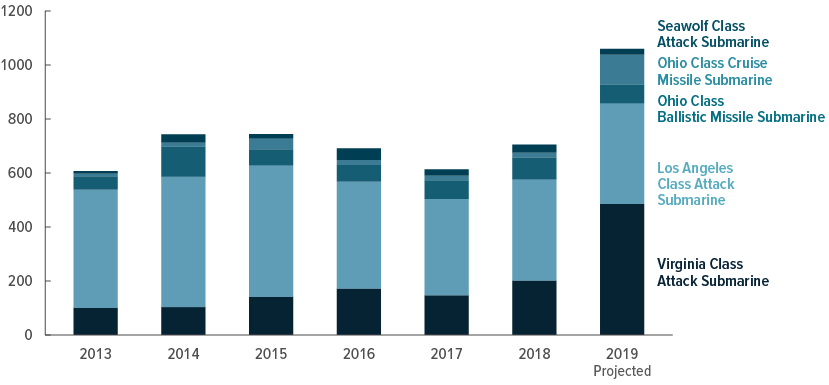
Source: Congressional Budget Office. “The Capacity of the Navy’s Shipyards to Maintain Its Submarines.”
The 50%-60% submarine spare part budget shortfall identified by DLA and NAVSUP above demonstrates the necessity for alternative sources of supply. Indeed, the NDIS report not only highlights efforts by DoD to invest in more very-much-needed private traditional manufacturing capabilities such as casting and forging, but also to encourage them to adopt advanced manufacturing technologies.
Obsolete and One-off Parts
All arms of the U.S. military are working to relieve supply chain challenges and deal with a further complication – obsolete parts.
This is an issue that has adversely affected both US Navy and Air Force as they attempt to maintain aging platforms for which mass production has ceased. The creation of new tooling alone can take months before parts can be reproduced using traditional methods. Typically, obsolete parts are not in high demand so they just need to be in low-volume production which also is not conducive to attracting high quality suppliers.
In 2018, the average age of Air Force aircraft was over 28 years according to Assessment of Military Power, 2018. The age of the aircraft creates a constant requirement for components that are difficult to acquire when original suppliers are no longer in existence and new suppliers have no desire to produce low volume quantities. “According to Air Force Magazine, in the first quarter of 2017 alone, the Air Force had 10,000 requests for parts that received no bidder because the original manufacturer was out of business, or it was not feasible for the company to produce needed parts” .
According to the NDIS, “DoD is not a large player in most industrial markets. DoD’s low volume buying patterns, lengthy periods between modernization, and often unnecessarily over-customized design specifications have combined to make DoD an unattractive customer, especially for smaller businesses.”
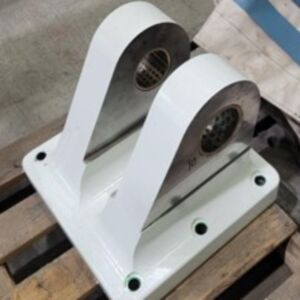
Huntington Ingalls Industries’/Newport News Shipbuilding recently used Wire-arc AM (WAAM) to create a 400-lb hinge for a reactor compartment door for the aircraft carrier Enterprise (CVN 80) for the U.S. Navy. In 2023 the engineering teams realized that the production of the 400-lb hinges required for the ship’s reactor compartment door to the bulkhead would result in critical months-long delays to the overall build schedule. Instead of creating the hinges using a traditional casting process, the team at HII in partnership with Lincoln Electric, turned to wire-based additive manufacturing as an alternative solution. The hinge was completed, post-processed and qualified within 10 weeks.
And indeed, the NDIS also notes that “changing priorities within the DoD, program cancellations, compliance burdens, funding challenges, and technology obsolescence, have disincentivized the traditional DIB to maintain production capacity beyond short-term, steady-state projections of defense demand.”
Digital production methods that include 3D scanning and reverse engineering can recreate obsolete parts in both ‘as-built’ and ‘as-designed’ 3D CAD data. From that point a part can be machined, tools can be created for casting processes, or the part can be rapidly 3D printed.
Given that AM is a methodology that works well with low volumes of parts, this digital production workflow from 3D scan data through to AM can represent a viable alternative to traditional production of obsolete parts.
Moving From Traditional Solutions to Additive Manufacturing
Across the last 25 years metal additive manufacturing (also known as 3D printing) has seen radical evolution and development to the point where it is becoming accepted for critical parts production in many industries, most notably, aerospace and defense shipbuilding.
The main characteristics that have traditionally hampered the widespread acceptance have been: build size, materials availability, and the ability to prove build quality.
Across the years, the main focus of research in AM has been on applications for lighter-weight parts, complex design for AM such as conformal fluid and gas channels, and component reduction. However, it has been noted that US Navy has taken a stance of streamlining efforts by duplicating the traditional design of the part in its Technical Data Packages (TDPs) as opposed to advancing new designs and innovations with a mission to be producing 100 AM produced submarine parts by the end of 2024 . This represents a major shift in the typical AM mindset and has a corresponding shift in training, certification, and design skills.
Metal AM Build Size
Metal AM started back in the early 1990s with very limited build sizes of a few inches and with significant inaccuracies in the printed parts. Since then, the industry has developed into a range of different metal AM technologies that can print parts as big as 38 feet long using a wider option of metal materials and achieving high quality standards.
The build size of Laser Powder Bed Fusion (LPBF) solutions has expanded recently with SLM’s NXG XII 600 offering a build size of 600 x 600 x 600 mm (23 inches), while Velo3D’s Sapphire 1MZ offers a 315 mm radius build to a height of 1000mm (12 inches x 39 inches respectively.) While these are a vast improvement in build sizes compared to 20 years ago, these do not offer much of a solution for very large parts most often found in heavy industry, shipbuilding and aerospace. The emergence of DED (Directed Energy Deposition) AM machines, which are based on welding principles, now offer much bigger build size options of up to 30-40 feet.
A much more recent entrant into the metal AM market is Friction Stir Additive Manufacturing (FSAM) or Additive Friction Stir Deposition (AFSD) which uses contact friction heat on metal materials which can then be extruded and which then weld together. It is able to print fully dense parts with a wrought microstructure with mechanical properties that meet or exceed properties of either traditionally manufactured or other additively manufactured components and has very few limitations on part size. Because of these attributes the technology is garnering fast interest from shipbuilding and aerospace manufacturers.
Increased Choice of Metal AM Materials
The growing availability of high quality AM metal materials including titanium, titanium alloys, Inconel, aluminum, niobium, stainless steel, tantalum, copper nickel, and tungsten also mean that there are a growing number of applications that metal AM can support. This has allowed the development of novel and innovative parts designed to improve performance in such things as turbine jets, rockets using metal AM.
The improvement in laser power in LPBF systems as well as improvements in materials innovation have recently enabled the increased use of copper in 3D printed parts, notably favored by NASA for its thermal conductivity, which is desirable in rocketry where heat exchange is critical . With the addition of metal AM as a solution for copper parts, engineers can now incorporate complex geometric structures into copper part designs which have potential to deliver improved part performance.
The AM Solution for DoD
Additive manufacturing is being increasingly considered important for this key logistical support, offering novel approaches to custom-built tools, prototypes, and replacement components. The Navy has a strong history of using additive manufacturing for each of the “application categories” up until the direct qualified/certified production. The launch of the US Navy AM Center of Excellence and the Accelerated Training in Defense Manufacturing (ATDM) program, both located in Danville, VA are a key part of the US Navy’s strategy to build much-needed skilled workforce in several fabrication methods, as well as build a functioning and valid alternative to traditional forging and casting using AM.
All arms of the military are researching and applying AM into critical areas of need. The Air Force Research Lab recently reopened its Additive Manufacturing Laboratory featuring a host of new production platforms as well as the installation of a novel 3D-printing system for aerospace-grade materials .
The United States Coast Guard (USCG) has been quietly researching and developing AM for repair and maintenance of its fleet since 2016, as well as applying new approaches to maintenance of navigation aids in Federal Waters, many of which have obsolete and unavailable parts. After a period of time focusing on plastic AM, USCG has now ventured into metal AM research.
The US Marine Corps has researched Expeditionary 3D printing, as well as concrete 3D printing of buildings with notable success, including the production of a medical cast aboard an airborne Marine Corps Osprey in July 2023 . In Q2 of 2024, the Corps is also opening a new AM training center located in Danville, VA.
The publication of the NDIS in 2023 forced this kind of research work into action to build “a more robust, modernized defense industrial ecosystem.” Figure 6 describes the actions needed to build resilient supply chains for the defense supply chains.
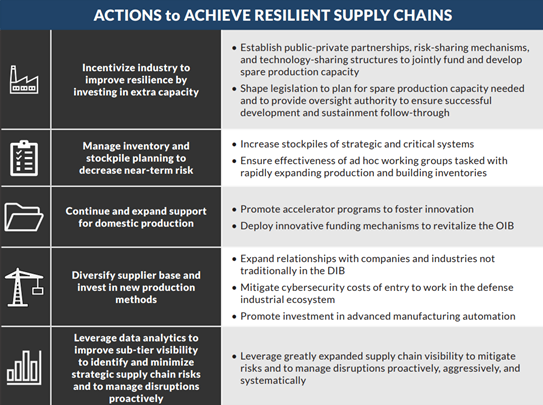
Figure 7. Source NDIS
Metal AM Landscape in Virginia
Challenges to adopting Metal AM
Metal AM is at a point where it can offer viable alternatives to traditional production techniques for the military. Given DOD Program delays, shortfalls in parts, coupled with overall contraction of the defense industrial base, the implementation of additive and advanced digital manufacturing techniques has become a priority across the DoD.
For any supplier considering the adoption of metal AM, there are several challenges to overcome including the demand signal, navigating the procurement processes, investment in equipment, investment in workforce and certifications, and then the cost and time burden brought by qualifications. Additional costs for extra cyber security provisions and, at times, getting top secret classifications are costly and can also adversely affect ROI.
The NDIS has clearly stated that it wishes to address many of these challenges as high priorities:
“The Department will pursue acquisition strategies that streamline the process and communicate a sustained and transparent “demand signal” to both domestic and international suppliers.”
It also prioritizes simplified procurement processes, greater diversification of the supplier base, and improving workforce readiness.
However, the biggest challenge both in terms of time and cost, for an AM parts supplier entering the defense supply chain is the various requirements in place to qualify as a supplier, and then remain qualified. Qualification of Additive Manufacturing (AM) machines, materials, and processes is a major barrier for the broad adoption of AM to produce parts and assemblies for which the in-service application requires certain levels of predictable performance. Generating the requisite data and models requires considerable time and expense from small/medium sized businesses in order to produce a body of statistically significant data. NIST reports that AM aerospace/defense qualification traditionally imposes requirements that cause small suppliers to spend millions of dollars in facility spending and years of material testing before they can supply specific 3D printed parts using a particular alloy and AM machine. Additionally, part vendors are sometimes required to supply substantially different data to each OEM, even when using the same manufacturing process, driving costs even higher.
Understanding the AM requirements for DOD manufacturing facilities and their prime contractors
Meeting qualification requirements for providing metal AM parts into the defense supply chain is a major challenge that can cost a lot of money and several years, even before being able to win any contracts. A number of efforts are underway to help relieve this arduous procedure but they will take time to resolve and become widely accepted.
The State of AM Requirements in Virginia
Virginia has many major industries in play in its industrial manufacturing base, and in the context of the defense supply chain, shipbuilding is a major participant, with aerospace secondary but still important. It is also important to note that in both shipbuilding and aerospace, requirements for parts naturally become more stringent depending on the criticality of the part and result in more extensive testing and inspection than for non-critical parts.
Naval shipbuilding using AM: This tends to be dominated by the NAVSEA requirements documents, with USCG working to potentially leverage these requirements for its own work.
In aerospace, after a supplier has worked through the basic certifications for quality, they will still have to go for extended certifications such as SAE AS 9100, and NADCAP (National Aerospace and Defense Contractors Accreditation Program). Having achieved that much, an aerospace OEM will most likely require qualification to AMS 7032, ASTM 52930, or similar, and then require further testing and qualification on their own proprietary rules. Extensive testing and qualification currently has to be repeated for each aerospace OEM that the supplier is hoping to do business with, resulting in extra and, perhaps unplanned, high cost.
Common Additive Manufacturing Qualification Template (CAM-QT)
The National Institute of Standards & Technology (NIST) indicates that inserting AM into an aviation part factory requires millions of dollars in infrastructure spending and years of material testing. Certain sectors such as aerospace/defense are highly regulated, often necessitating end-user companies to define suppliers’ facility requirements and then certify part reliability and production repeatability. To add further to that burden, the entire process used to qualify a vendor to a single aerospace OEM is deemed proprietary to that OEM, and also entails inspection of vendors’ AM system installation and facility operations to meet OEM standards for safety, reliability, and repeatability. Therefore, in order for such a vendor to become qualified to supply additional aerospace OEMs, it must start the processes all over again for a second or third OEM, costing millions of dollars and taking years to achieve.
With this in mind, CAM-QT is supported by the Office of the Under Secretary of Defense, Research and Engineering (OUSD(R&E)), to bring aerospace gas turbine industry rivals together to establish and implement a single AM supplier qualification process for aerospace gas turbine parts to be delivered to USG and Defense Industrial Supply Chain.
Conclusion
- Suppliers adopting metal AM should be prepared to extend their existing ISO 9001 quality management systems to AM
- While non-critical AM parts do not need so much qualification as for critical parts, a shop should be prepared to perform qualification test builds and testing at any time
- Suppliers should be ready and budgeting for extended quality certifications including AS 9100 and Nadcap accreditations for AM as appropriate (for aerospace.)
- As a general recommendation, qualifying to a good general standard such as ISO/ASTM 52930 will prepare the shop’s workforce to pursue other more stringent qualifications
- At first pass, machine shops should focus on qualifying in one vertical market based on indications of where the most demand will be
- Suppliers will currently have to have a large budget for qualifying numerous times with different OEMs.
The industry as a whole needs to streamline with common qualification practices but more attention needs to be put onto reducing the costs of qualification, and the DoD or US Government may need to find and develop incentives to enable qualification by AM suppliers.
Astro America. (2024). Understanding the Requirements of DoD, Prime Contractors in Qualifying Suppliers of Metal AM in Virginia.