TL;DR — A well‑built manufacturing training programs fill skill gaps, raises throughput, trims operating costs, improves safety, and prepares plants for Industry 4.0. The sooner you launch, the sooner those gains arrive.
Table of Contents
- Close the Skills Gap with Workforce Development
- Boost Throughput with Advanced Training
- Reduce Operating Costs by Growing Talent Internally
- Build a Safety‑First, Audit‑Ready Culture
- Prepare Teams for Industry 4.0 Technologies
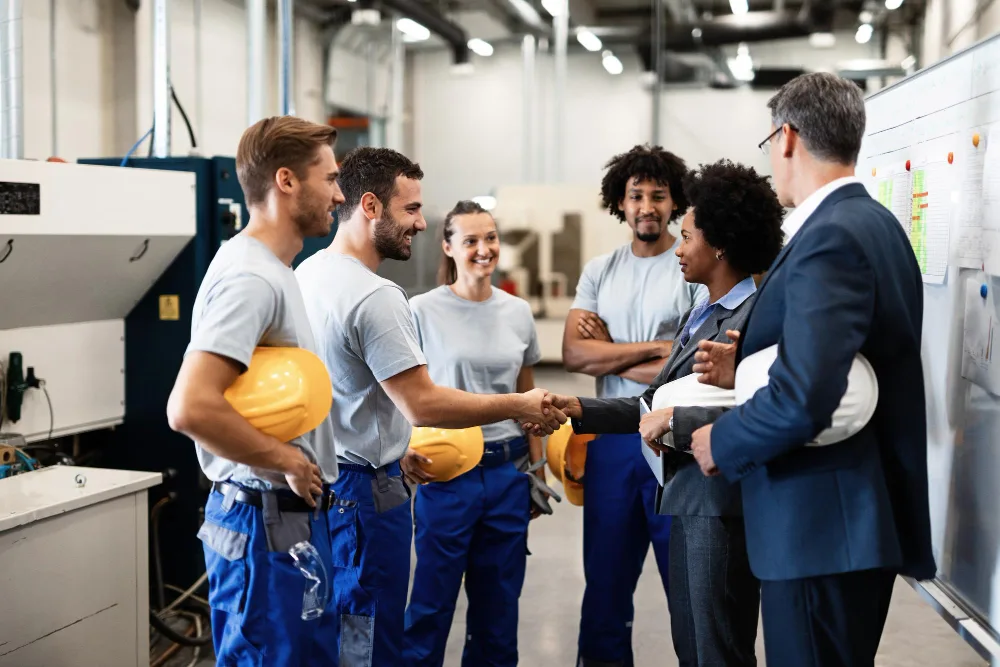
Why Training Can’t Wait
Every month, U.S. manufacturers advertise thousands of open roles they can’t fill, while customer lead times stretch and improvement projects stall. Forward‑thinking companies counter the shortage by rolling out manufacturing training programs that grow talent from within.
When skills rise, machines run better, scrap falls, and expansion plans move from “someday” to “signed.”
The five reasons below show how targeted learning turns workforce pressure into a measurable advantage.
1 · Close the Skills Gap with Workforce Development
A structured manufacturing training program does more than teach button‑pushing. It pairs classroom concepts—print reading, basic metrology, lean foundations—with floor mentoring that delivers context in real time. Supervisors note that novices who follow this blended path safely operate equipment weeks sooner, and seasoned operators gain a route into maintenance, quality, or team leadership. Turnover drops because people see progress; recruiters spend less on ads; and workforce development in manufacturing becomes a strategic asset rather than a yearly scramble.
2 · Boost Throughput with Advanced Training
Skill unlocks hidden capacity. At a food processor, changeovers shrank by thirteen minutes once operators finished advanced manufacturing training on standardized setup sheets and torque specs. First‑pass yield rose seven percent, and short stops declined almost one‑fifth. The curriculum combined shop‑floor coaching with online training manufacturing refreshers that fit into pre‑shift huddles. Metal‑formers report similar results after rolling out manufacturing training courses on die‑setting and statistical process control: more good parts, less overtime.
3 · Reduce Operating Costs by Growing Talent Internally
Turnover, scrap, and breakdowns drain profit faster than new sales replace it. Continuous manufacturing skills training reverses that flow. At one aerospace supplier, voluntary quits fell by six percentage points, saving nearly $80 000 in rehiring and lost production. Scrap was cut in half when machinists applied newly learned SPC techniques. Operators trained in daily condition checks caught bearing wear early, cutting emergency repairs by more than half. Those savings funded sensor retrofits and data‑driven marketing consulting manufacturing campaigns that opened new markets.
4 · Build a Safety‑First, Audit‑Ready Culture
Policies matter only when workers know how to use them. Comprehensive manufacturing training programs embed lock‑out, hazard recognition, and near‑miss reporting into daily routines. A coastal metal‑former introduced ten‑minute safety refreshers during warm‑ups; recordable injuries dropped by one‑third within a year. Digital completion logs integrate with site‑wide manufacturing quality systems, which means OSHA and ISO auditors verify compliance in minutes, not hours. Fewer incidents free supervisors to focus on process improvement instead of paperwork.
5 · Prepare Teams for Industry 4.0 Technologies
Connected sensors, MES dashboards, and cobots deliver value only when staff can interpret data and act on insights. Future‑ready manufacturing training programs weave three themes into existing curricula:
- Data literacy – SQL basics and SPC chart reading
- Automation collaboration – safe interaction zones and fault isolation
- Continuous improvement – root‑cause analysis built into daily huddles
A plastics molder added these elements, switched scrap alerts from a two-day delay to live dashboards, and saved $180,000 in resin during the first quarter alone. Keeping content current with refreshed online training manufacturing modules ensures teams evolve alongside technology.
Ready to Build a Workforce That Delivers?
GENEDGE hosts more than 500 expert‑authored modules, plus onsite coaching to design manufacturing training programs for any shift pattern or budget. Whether the goal is rapid onboarding, advanced certification, or plant‑wide transformation, our advisors create learning paths that show measurable gains within months.
Contact GENEDGE today to assess current capabilities, map a custom training plan, and start the upskilling effort that secures your competitive edge.