At the heart of operational excellence lies the quest of continuous improvement.
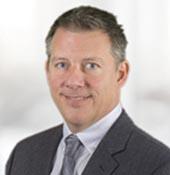
Jeff Shook, GENEDGE’s Engagement Manager, points to EMSCO as an example of that practice. The industrial electronics manufacturer in Ashland is a model lean organization and is a company GENEDGE has worked with over the past 10 years.
“EMSCO has the right culture and mindset of continuous improvement,” Shook said. It’s a company that always thinks and acts with a continuous improvement mindset.
That helps explain why there’s been virtually no turnover over the past decade in the company, which employs about 35 and manufactures products such as electrical wire and multiconductor cable harnesses, circuit board assemblies, and electronic and mechanical box builds.
There are four stages of manufacturing, Shook explained.
They range from Stage 1 “internally neutral,” where a manufacturer might perform poorly and is reactive, to Stage 4 “externally supportive,” where a company offers ongoing training, engages employees, and is proactive. Stage 4 is often described as the best in class.
These stages are based on 12 manufacturing principles that include:
- Safety,
- Good housekeeping,
- Disciplined use of authorized,
- Formal systems,
- Preventive maintenance,
- Commitment to continuous improvement
- Purposeful communications plan
Also key are: ongoing training, an operator-led process control culture, and timely delivery of products to customers.
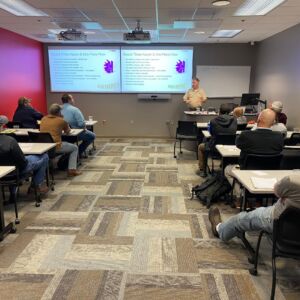
Continuous improvement means you never rest on your laurels. “When we talk about operational excellence, GENEDGE is helping small and medium-sized manufacturers in Virginia assess how they’re doing and identify the challenges and opportunities for success,” Shook said.
EMSCO first reached out to GENEDGE about 10 years ago when the company moved to a new building and wanted help in setting up “in an ideal way” for manufacturing, Garrett said. Over the years GENEDGE has led lean workshops and helped with strategic industry and company evaluations.
In December, EMSCO co-owner Parker Garrett invited GENEDGE back for him and his co-workers to continue learning more about the lean process.
“Lean is a little bit like a quote of Benjamin Franklin along the lines of, ‘Humility is one characteristic that when you think you’ve obtained it, you’ve lost it.’ Lean is like that – it’s a work in process. If we think we’ve obtained it, we’ve probably lost it,” Garrett said. “The lean workshop really helped our organization as a whole see what could be done if we did things a different way.”
There’s a perception that efficiency means doing a job faster and in larger quantities. The lean process is the opposite by eliminating wasteful activities and making only what is needed when it’s needed. When you do that, it’s easier to catch and correct mistakes.
“GENEDGE has helped us with creating a culture that is enjoyable to work in, that has you get the satisfaction of building something from beginning to end. By having organization and well thought out structures, there are no fires on the floor,” meaning crises and issues are eliminated, Garrett said. “There’s no question that we love learning and are always looking at ways to improve.”
If you are interested in learning more about taking a Lean 102 class click HERE or email: info@genedge.org to learn more about upcoming offerings.