TL;DR Smart cameras, live‑data sensors, and predictive software are changing beverage production quality control. New tech spots defects early, warns crews before machines break, and adjusts recipes on the fly. The result is lower scrap, smaller utility bills, and more bottles that meet spec—all of which are major wins for cost, waste, and sustainability.
Table of contents
- AI’s new role on the line
- Why plants see quick wins
- Where AI brings the most value
- Building a solid foundation
- Clearing common roadblocks
- What’s next for AI in beverage plants
- First steps for new adopters
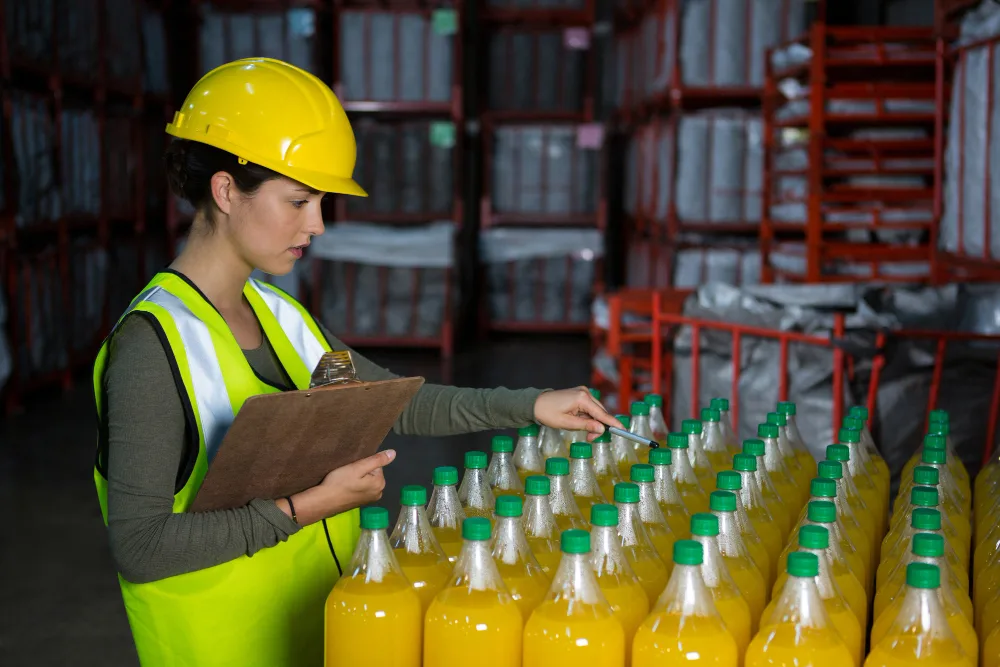
1. AI’s new role on the line
Human inspectors can’t watch every bottle or crunch millions of data points. In today’s AI quality control beverage industry setups, cameras check each container against a “perfect” image while algorithms flag tiny changes in fill height, cap torque, or label position. Results show up on cloud dashboards, giving managers instant insight and faster fixes—something that’s vital in modern beverage manufacturing optimization.
2. Why plants see quick wins
- Less waste, lower cost—Vision tools reject bad bottles early, saving product, glass, and labels. Predictive alerts cut rinse‑and‑restart cycles, proving how AI helps reduce production waste in beverages and eases waste management in beverage production.
- Steady quality—AI watches colour, clarity, and pH in real time, so every batch meets the target specs.
- Sustainable beverage production—Fewer rejects mean less water, energy, and packaging per saleable unit.
- Easier audits—Automatic logs speed up recalls and meet rules—an often‑missed benefit of AI quality control in beverage factories.
3. Where AI brings the most value
- Visual checks – High‑speed cameras catch chipped glass or crooked labels in a flash.
- Line monitoring – Sensors track pressure, flow, and temperature, then tweak valves in seconds, boosting beverage production quality control.
- Predictive maintenance – AI reads vibration and motor load to schedule repairs before a breakdown.
- Recipe tuning – Machine learning balances sweetness and acidity, cutting costly trial runs.
- Demand forecasting – AI reviews sales trends so buyers order only what’s needed—part of wider AI for waste reduction in manufacturing programs.
4. Building a solid foundation
AI works best when plant data is clean and reliable. Start with clear work rules, traceable lot codes, and calibrated gauges. Many plants tighten these basics through GENEDGE’s manufacturing quality systems service, which maps current checks and fixes gaps. Once set, a cloud dashboard plugs AI results into the plant’s quality management system for manufacturing. Operators get live alerts, maintenance teams get early warnings, and managers see end‑of‑shift reports. AI insights move straight to action—less overfill, fewer label do‑overs, and more progress toward sustainable beverage production.
5. Clearing common roadblocks
Up‑front cost, scattered data, and staff nerves top the worry list. Start small—one camera cell or one sensor—and scale after payback. Link lab, production, and inventory data through the same dashboard to kill silos. Train line leads to read alerts, techs to solve issues, and operators to trust that AI highlights problems, not people.
6. What’s next for AI in beverage plants
Edge computers will soon run AI right on machines, a sign of the future of beverage manufacturing with AI. Fillers will self‑adjust drop by drop, blockchain will track every ingredient, and carbon dashboards will refresh hourly. These upgrades will push beverage production quality control from paperwork to real‑time screens on the factory floor.
7. First steps for new adopters
- Audit defects – Which flaws cause the most waste?
- Run a pilot – Test one vision cell or predictive sensor on that pain point.
- Bring in experts – GENEDGE’s manufacturing quality systems team can link hardware, data, and lean goals.
- Measure ROI – Capture waste, labour, and energy before and after.
- Build the roadmap – Use results to expand AI plant‑wide under a robust quality management system for manufacturing.
Plants that start today report less scrap, more sellable bottles, and a clear edge built on reliable beverage production quality control. Early moves position any beverage line for the next wave of AI tools, meaning lower waste and higher margins in every case pack.
Support from GENEDGE
Unsure how to launch—or scale—an AI upgrade? GENEDGE delivers tailored industrial-engineering services that guide Virginia manufacturers through every step of modernization. Whether the goal is tighter machine utilization, zero scrap, or a streamlined digital workflow, GENEDGE specialists map the current process, crunch the data, and recommend solutions that fit your floor—no guesswork, just numbers.