TL;DR More than ever before, Smart technology for small food manufacturers can now be added in smaller, more manageable steps. Compact sensors, cloud dashboards, and focused automation trim waste, raise throughput, and lock in quality—all without a full plant overhaul. Start with a quick audit, tackle one high-impact area, and use GENEDGE resources to keep upgrades practical and affordable.
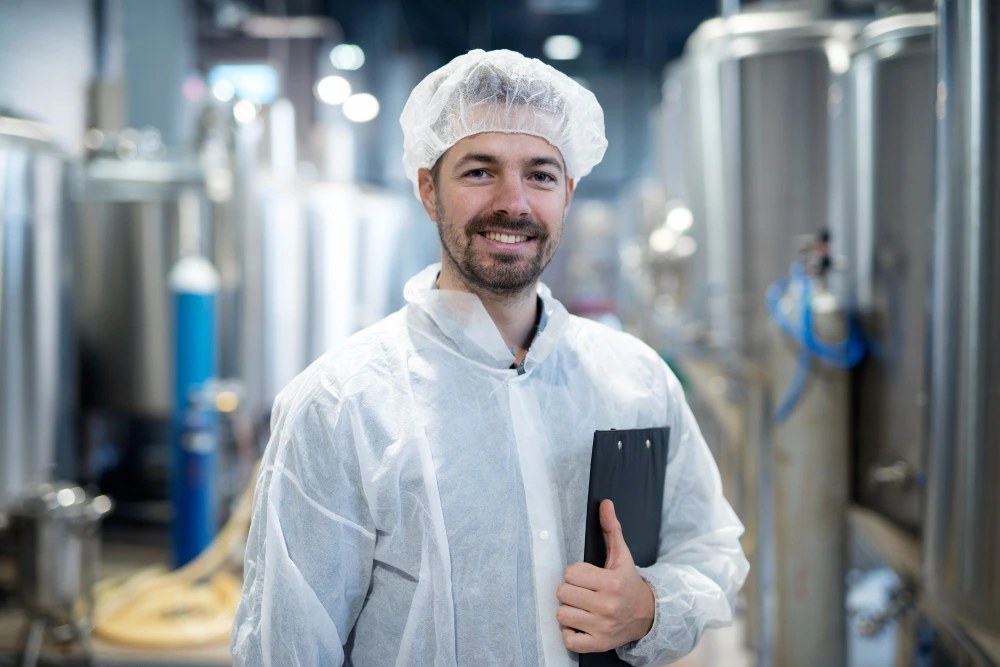
Table of contents
- Why smart tech can’t wait
- First steps on a lean budget
- Tools with the biggest payback
- GENEDGE support and stronger supply chains
- Clearing common roadblocks
- Action plan—one step at a time
- Move forward with GENEDGE — next steps
Why smart tech can’t wait
Rising ingredient costs, labor gaps, and stricter safety rules push every processor to run leaner. Smart tools—sensors that flag temperature swings, AI cameras that catch label errors, and cloud apps that keep inventory honest—help small plants meet demand while protecting margins. Many of these food industry technology solutions now arrive in modular, budget-friendly packages, turning what used to be capital projects into measured, pay-as-you-grow investments.
First steps on a lean budget
A short assessment keeps spending focused. Walk the floor, note rework, track downtime, and tally scrap. Outside advisors—such as GENEDGE and its custom solutions for manufacturing companies—can validate findings and rank fixes by ROI. From that baseline, small operators typically move in three clear stages:
- Target the worst bottleneck. Choose the station that wastes the most time or product—often manual filling, slow labeling, or unmonitored refrigeration.
- Pick one affordable tool. This might be a pair of plug-and-play temperature sensors or a tabletop filler—true low-cost automation for food processing.
- Measure everything. Track waste, labor hours, and energy before and after. Hard numbers justify the next round of upgrades.
Each step proves that upgrading food production without high costs is possible, building momentum for the next improvement.
Tools with the biggest payback
A few modest technologies consistently return value:
IoT storage sensors
Drop-in devices send real-time alerts when cold rooms drift out of spec, helping reduce spoilage by as much as 30 percent. They also feed continuous data into digital logs, easing audits.
Semi-automatic fillers and labelers
These units lift throughput, cut spills, and relieve repetitive motion. Because they keep operators in the loop, they fit existing workflows without extensive retraining—an easy win for manufacturing efficiency for small food businesses.
Cloud-based inventory and ERP apps
Subscription platforms replace spreadsheets, sync purchasing with production, and support digital transformation for food manufacturers without servers or IT staff.
AI inspection kits
Machine-vision cameras mount over existing conveyors, catching crooked caps, underfills, and off-color product. Fewer rejects mean less material in the dumpster and more on the dock.
Simple production dashboards
Low-cost screens combine sensor feeds and order data, giving managers a single view of yield, downtime, and quality trends—fuel for continuous improvement.
Rolled out one at a time, these tools build a data-driven culture and free up cash for successive upgrades.
GENEDGE support and stronger supply chains
Tech gains crumble if supplies stall. GENEDGE’s SCOIN program offers supply chain optimization for manufacturing companies, mapping supplier risk and linking processors with vetted regional partners. Aligning SCOIN insights with shop-floor tech ensures that late ingredients or packaging shortages don’t derail smart production.
Clearing common roadblocks
- Budget anxiety – Start with a single sensor or semi-auto station, use state grants or tax credits to offset cost, then reinvest savings.
- Data silos – Choose cloud tools with open APIs so QC, production, and purchasing share a single source of truth—a cornerstone of any quality system.
- Staff resistance – Demonstrate how automation removes tedious chores, and provide concise, hands-on training.
- Vendor overload – Let GENEDGE vet suppliers to match true food industry technology solutions to real shop-floor needs.
Action plan—one step at a time
- Audit pain points. Quantify waste, downtime, and manual rework.
- Pilot a single tool. Start with the biggest bottleneck—often packaging or refrigeration.
- Track the payoff. Document gains in scrap, labor, and energy.
- Expand deliberately. Add sensors, AI inspection, or cloud ERP as ROI builds.
- Leverage GENEDGE. Their experts integrate tech upgrades with funding paths and supply-chain alignment so smart technology for small food manufacturers delivers lasting results.
Early adopters show that modest investments made in the right order drive measurable gains: fewer rejects, tighter inventories, and better margins. One well-chosen upgrade leads to the next, turning manual plants into agile, data-driven operations.
Move forward with GENEDGE — next steps
Modernizing doesn’t require a blank check—just the right sequence and the right partner. GENEDGE delivers custom solutions for manufacturing companies along with SCOIN supply-chain support, helping small processors adopt technology that pays for itself. Talk with a GENEDGE advisor to map out your first pilot, secure funding, and build a roadmap toward a leaner, data-driven future.