TL; DR: Sustainable machining focuses on reducing waste, energy use, and environmental impact through practical shop-level changes. Small, strategic steps can significantly improve efficiency and reliability without needing a major overhaul.
For as long as machining has existed, manufacturers have looked for ways to make production more practical and good for their profitability. Over the years, advances in cutting tools, production machinery, and workflow optimization have helped businesses improve quality while keeping costs in check.
Today, the push for sustainable manufacturing practices looks a little different. It focuses on lowering raw material waste, cutting energy consumption, and minimizing environmental impact. While conversations around sustainability often focus on big-picture global issues, the real difference comes from practical changes at the shop level—adjusting pricing strategies, eliminating inefficiencies, improving lead times, and becoming more reliable.
Thankfully, creating a more sustainable machining process doesn’t require a massive overhaul. With the right strategies—and often the right expert guidance—companies can take small, smart steps that make machining operations more future-proof.
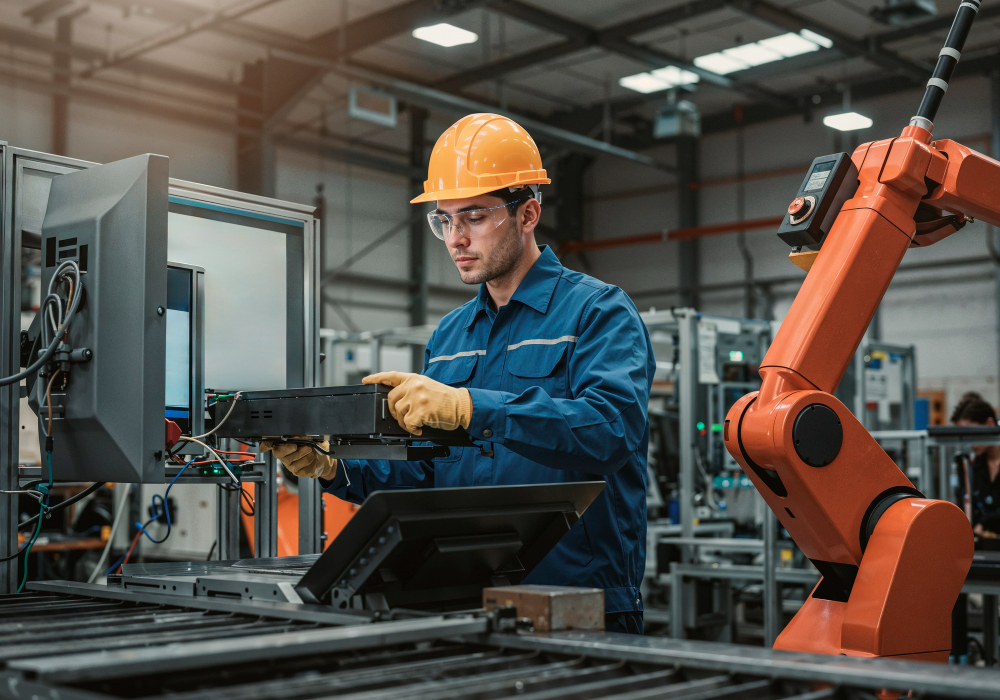
Table of Contents
- Price Smarter, Stay Profitable
- Find the Hidden Costs Holding You Back
- Speed Up Lead Times (Without Cutting Corners)
- Cut Waste Without Cutting Quality
- Boost Productivity Without Burning Out Your Team
- Make Your Processes More Predictable and Less Stressful
- Save Energy, Save Money
- Build a More Sustainable Shop with GENEDGE
Price Smarter, Stay Profitable
One of the biggest challenges manufacturers face is setting sustainable prices. Prices are too high, and customers might walk. Prices are too low, and margins suffer.
Consultants help uncover the hidden costs—like machine downtime, tool breakage, and rejected parts—that often aren’t captured in traditional pricing models. In Virginia, GENEDGE works with manufacturers to apply lean machining pricing strategies that align with operational efficiency, sustainable practices in manufacturing, and long-term profitability.
Find the Hidden Costs Holding You Back
Many shops don’t see where the real money is leaking—unplanned downtime, inefficient tool usage, and wasted materials. These hidden costs chip away at profitability and make sustainability harder to reach.
Consultants like GENEDGE use tools like OEE (Overall Equipment Effectiveness) and lean waste identification to shine a light on these issues. Once identified, they guide manufacturers through process improvements that drive measurable change.
Speed Up Lead Times (Without Cutting Corners)
Sustainability includes customer trust. And lead time isn’t just about how long a part takes to machine—it’s the entire process, including quoting, ordering, approvals, and inventory readiness.
Consultants can streamline those front-end processes, introduce machine monitoring systems, and improve tool inventory management. For example, if a part takes 3 weeks to machine but admin processes add another 2, a consultant can help cut that back, making your 5-week lead time feel like 3.
Through advanced manufacturing consulting, GENEDGE supports companies with smart technology adoption that reduces friction and keeps production flowing.
Cut Waste Without Cutting Quality
Waste used to be seen as the cost of doing business—but now, it’s a red flag. Consultants bring proven strategies to reduce waste across the board:
- Material Waste: Refined tool paths, better nesting, and scrap reuse
- Cutting Fluids: Switching to biodegradable oils or Minimum Quantity Lubrication (MQL)
- Energy Efficiency: Upgrading to machines with lower kilowatt ratings that still outperform older models
These aren’t massive investments but targeted, consultant-guided tweaks that get rid of waste and boost output.
Boost Productivity Without Burning Out Your Team
A sustainable business supports its workforce. Consultants help manufacturers measure labor productivity without tying it to wages, which helps facilities compare performance across teams.
They also guide upskilling efforts, introducing cross-training programs and workflow improvements that cut setup time and make operators more effective. Skilled teams supported by the right tools are more resilient, more productive, and more sustainable.
Lean manufacturing consultants can help implement these people-first strategies to keep your operations running smoothly long-term.
Make Processes More Predictable and Less Stressful
Unpredictable processes lead to wasted materials, missed deadlines, and frustrated teams. Consultants help standardize workflows, reduce variability, and streamline production flow to avoid delays and rework.
They also advise on managing Work-In-Progress (WIP). Too much WIP ties up resources and increases the risk of damage or obsolescence. Keeping WIP low makes production leaner, faster, and more reliable.
GENEDGE also helps Virginia manufacturers rethink their plant layout and expansion to better support lean principles and long-term growth.
Save Energy, Save Money
Energy is one of the biggest areas for improvement—and savings. Studies have shown that energy consumption in machining centers is dominated by auxiliary systems such as cooling, pumps, and other components, while the actual cutting process accounts for a comparatively smaller proportion.
Frank Otabor, an innovation strategist at GENEDGE, expresses in a recent LinkedIn post that data centers in the U.S. already consume 4.4% of the country’s electricity, and that’s expected to rise in the coming years. This same issue applies to machining centers, which also rely on energy-intensive systems.
Consultants help businesses:
- Lower idle machine time
- Optimize cooling and fluid systems
- Upgrade to energy-efficient machines that deliver better results
- Conduct energy assessments
Example: If a machine used to produce two parts per shift and can be optimized to produce three with only a small energy increase, that’s a 36% drop in energy use per part—a huge win for both cost and sustainability.
Build a More Sustainable Shop with GENEDGE
The future of machining is efficient, responsible, and reliable. And with the right partner, it’s absolutely within reach.
And machining sustainably doesn’t mean starting from scratch—it means improving what you already do, step by step. GENEDGE brings lean manufacturing expertise, localized knowledge, and proven systems that help Virginia’s manufacturers thrive in a competitive, low-waste future.
Whether it’s smarter pricing, better lead times, or energy savings, GENEDGE helps turn those goals into action. Contact us to learn more about how we can help in the following areas:
- Plant Layout/Expansion
- Cybersecurity
- Energy Management
- Environmental Health & Safety
- ISO 14001/50001