Continuous improvement is the backbone of modern manufacturing. To maintain a competitive edge and respond to the evolving landscape, manufacturers must foster an environment where teams are empowered to innovate and enhance operations at every turn.
DEVELOP YOUR COMPETITIVE EDGE: Dive deep into Lean principles with a hands-on simulation
In this guide we’ll explore:
- How to cultivate a workplace that thrives
- Insights on how to empower your team
- How to ensure continuous improvement is a daily practice, not just a slogan.
The Importance of Team Empowerment and Continuous Improvement
Manufacturing thrives on change, with continuous improvement at its core. Empowering teams to innovate and contribute autonomously drives efficiency and productivity.
Using everyone’s knowledge makes manufacturing agile and innovative. Engaging with lean manufacturing consultants offers customized advice and strategies. The strategies can be used to optimize operations for Virginia manufacturers. This approach supports manufacturing workforce development, ensuring teams possess the necessary skills and knowledge to contribute effectively.
An article from the Education Development Center explains some of the tips below and how continuous improvement establishes a strong team. Let’s now turn our attention to some practical tips that can help foster these critical elements in your operations.
Understanding the key roles of team empowerment and continuous improvement in manufacturing success, here are practical tips to foster these elements in your operations.
1. Setting Clear Goals:
Team empowerment starts with a shared vision. Begin by defining specific, measurable objectives. Ambiguity causes confusion, while clear targets align efforts and show results. Here’s how:
- Define Specific, Measurable Objectives: Make goals precise with defined success metrics. For example, aim to cut setup times by 20% in three months or raise first-pass yield by 10% by year-end.
- Communication is Key: Setting goals is not enough; effective communication is crucial. Use different methods and repeat key messages for better understanding. Visual aids like charts can help reinforce the message.
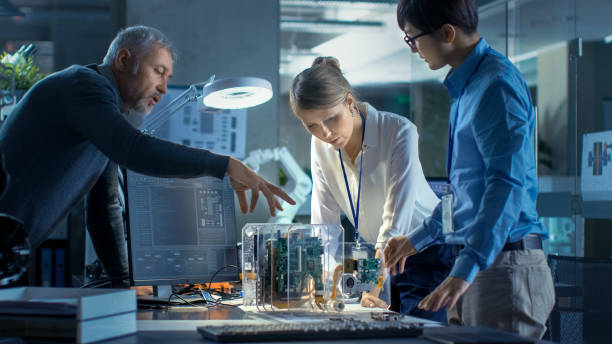
2. Providing Training and Development Opportunities
For teams to contribute fully, they need the right tools and skills. Offer training and development opportunities so team members can acquire and refine the skills necessary for continuous improvement.
Here’s how to ensure your team is equipped:
- Skill-building Workshops: Plan regular workshops focused on specific skills related to process improvements, such as Six Sigma methodologies, creating a Kaizen Culture, or advanced equipment maintenance.
- Support Ongoing Learning: Encourage and provide resources for team members to pursue further education or certifications. Investing in their learning is investing in the growth of your operation.
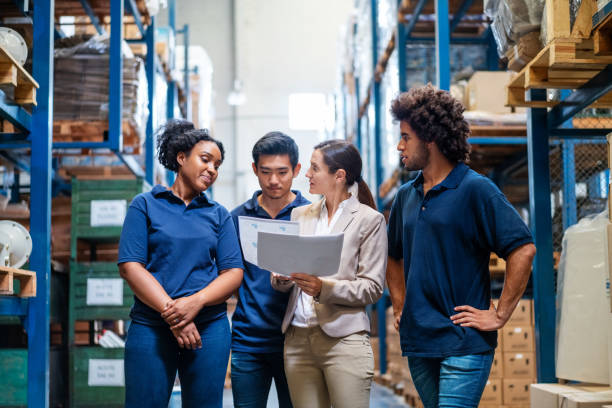
3. Encouraging Open Communication
An empowered team needs to be heard. Open channels for communication within your organization are paramount. This Forbes article highlights that employees who feel their voice is heard are nearly 4.6 times more likely to perform their best work. Here’s how to make it happen:
- Foster a Culture of Transparency: Share information openly about goals, performance, and areas of improvement. Transparent communication builds trust and encourages staff to do the same.
- Listen Actively: Hearing feedback is one thing; actively listening to it is another. Make sure team members know their input is valued and acted upon. Their insights can often be the key to unlocking improved processes and products.
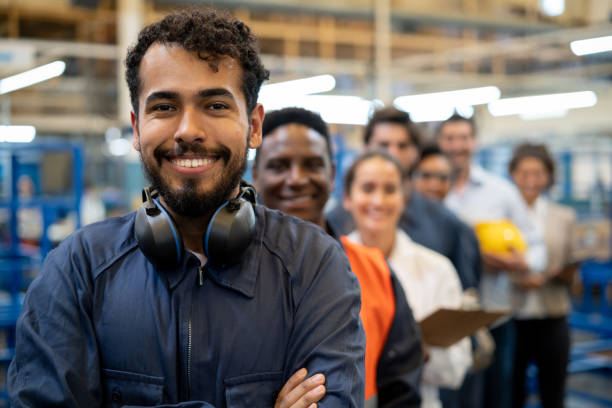
4. Recognizing and Rewarding Achievements
Acknowledgement and rewards help to reinforce positive behaviors and successes and catalyze motivation. Here’s how to recognize and reward your team:
- Acknowledge Individual and Team Successes: Publicly celebrate milestones and achievements. This not only recognizes the contribution of individuals but also serves to motivate the wider team.
- Implement Incentive Programs: Tie specific goals to incentives, such as bonuses or extra vacation days. Such programs ensure that the team is aligned with the organizational objectives and rewarded for achieving them.
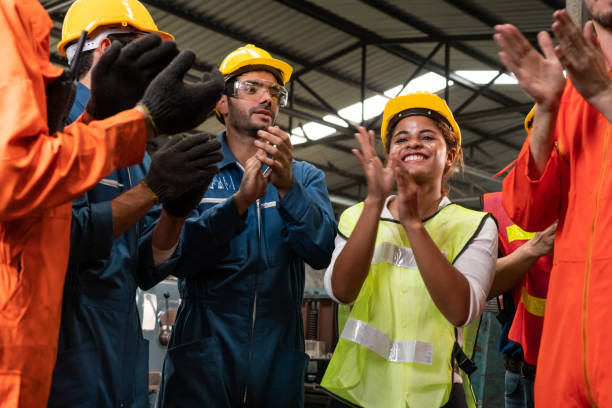
5. Implementing Feedback Mechanisms
Feedback is the lifeblood of continuous improvement. Here’s how to establish and utilize feedback mechanisms effectively:
- Regular Gatherings and Surveys: Organize regular meetings and surveys to gather feedback on processes and restructuring strategies.
- Use Feedback for Improvement: Act on the feedback received. Use positive and negative insights to drive improvements and enhance a collective growth and progress culture.
Empowering manufacturing teams with continuous improvement takes time, planning, effort, and leadership commitment. By following this guide, create an environment where everyone drives progress and improvement daily.
Ready to enhance your manufacturing practices? GENEDGE offers operations optimization for Virginia manufacturers. Request a free assessment and gain access to training services for sustained growth.