Written by Bert Eades, GENEDGE Business Services Director
It’s Saturday afternoon on Memorial Day weekend. Family members just arrived at your house for a cookout when your cell phone rings – it’s a supervisor from the plant. An employee cut the tip of his finger off and there’s a lot of blood.
Immediately, your mind races: Is he going to be okay? Should we call 911 or take him to urgent care? Is an urgent care even open? How do we get him there? Was he under the influence? Should we test him?
Once these questions are answered and you start to calm down, other questions may come to mind. How did this happen? How do we safely clean up blood? Do I have to report this injury to someone? If so, who? Is there a deadline? How do I make sure this doesn’t happen again? What if OSHA shows up at the plant?
As a business grows, safety might not always be top of mind. However, a structured safety program is essential to protect its workers, prepare for emergencies and comply with OSHA regulations. Fortunately, OSHA provides resources to help, including a step-by-step guide to create a program and the first couple steps are described below.
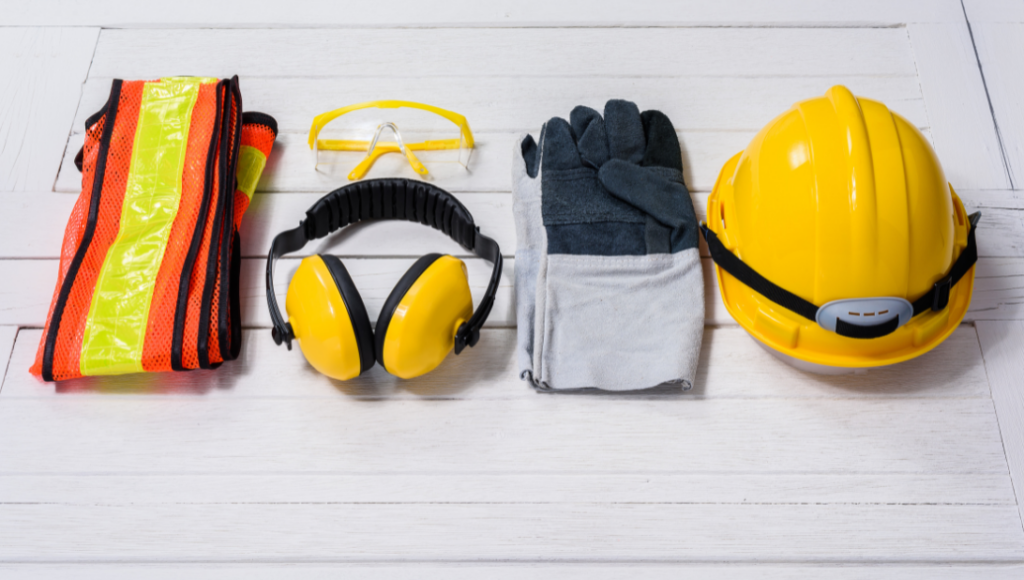
Step 1: Lead with Management Commitment
Like most things, a successful safety program starts with leadership. There are three key deliverables:
- Writing a safety and health policy. This document clearly states the organization’s commitment to maintaining a safe workplace and lists company safety rules. It should be communicated across all levels of the organization to set expectations and establish accountability.
- Develop SMART goals—Specific, Measurable, Achievable, Relevant and Time-bound—that define what you hope to achieve from the program. Here are some examples:
- Reduce the current year’s recordable injury rate by 20% compared with the previous year.
- Train all active employees on lockout/tagout, fall protection, hazardous materials and required personal protective equipment by the end of the year.
- Conduct facility audits at least monthly and correct at least 75% of identified deficiencies.
- Create a safety and health plan. As the saying goes, a goal without a plan is just a wish, so this plan should outline how you expect to achieve your SMART goals and allow you to measure progress. For example, list employee safety training to develop and deliver along with the owners responsible and due dates.
Step 2: Engage Employees in the Process
Employee involvement is critical to the success of any safety program. This starts by forming a team of “safety champions”—employees from various departments who are passionate about workplace safety and can serve as liaisons between workers and management.
There are a handful of key safety processes needed, and this team can help with implementation and execution.
- Define what safety incidents should be reported and create a system that encourages employees to voice safety concerns without fear of retaliation.
- Develop a safety incident investigation process. It should identify root causes and action items, which are critical for driving continuous improvement and achieving your goals.
- Conduct routine safety audits to observe behaviors, identify hazards, ensure regulatory compliance and help build a culture where employee safety is an organizational value.
- Establish a regular agenda and routine meeting schedule for the safety team. They provide a structure to review incidents, share best practices and track progress toward safety goals.
Need Help Getting Started?
Building an effective safety and health program that protects employees and ensures regulatory compliance may seem overwhelming, but you don’t have to do it alone.
GENEDGE can help you develop a customized safety and health policy, set organizational goals, create a plan and implement policies, processes and employee training. To learn more, contact your Regional Growth Manager or reach out to Bert Eades at bert.eades@genedge.org.