TL;DR Smart factory automation—robotics, IIoT sensors, and AI analytics—turns data into action. Plants that start with a focused pilot, upskill their teams, and scale in phases cut downtime, lift first-pass yield, and protect margins. GENEDGE can map your first move.
Table of Contents
- Why Automation Now Drives the Bottom Line
- Five Automation Plays That Deliver Fast ROI
- How to Launch Automation Without Disruption
- Clearing the Most Common Roadblocks
- Beyond the First Pilot—Building an Industry 4.0 Roadmap
- Act Before Your Competitors Do
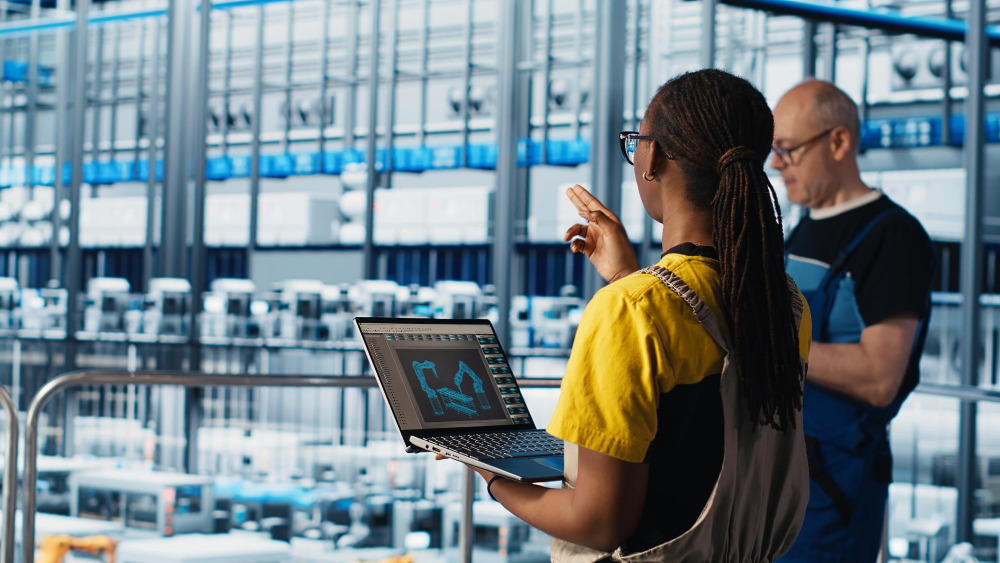
Why Automation Now Drives the Bottom Line
Manufacturers see tightening labor pools, volatile demand, and higher energy costs. Smart factory automation tackles all three:
- Robots run 24/7 without fatigue
- Edge sensors stream live performance data into dashboards
- AI vision flags defects before scrap piles up
A recent Deloitte survey shows 74 % of plants expect full Industry 4.0 adoption within two years; waiting risks delivery and price advantage.
Five Automation Plays That Deliver Fast ROI
1. AI-Powered Customer Service
Chatbots handle routine order questions, schedule RMAs, and collect real-time feedback. Human agents then focus on complex negotiations, improving both responsiveness and loyalty. (Closed-loop data flow strengthens manufacturing quality systems and speeds design fixes.)
2. Sensor-Driven Supply Chains
RFID tags, GPS beacons, and predictive models forecast demand spikes and port delays. Smart inventory frees cash for R&D instead of shelving excess stock.
3. Predictive Maintenance
Machine-learning algorithms compare vibration, temperature, and power draw against baseline signatures. When risk rises, planners intervene during scheduled downtime—plants report up to 50% fewer surprise stoppages and longer asset lifetimes. GENEDGE’s online training manufacturing courses show technicians how to read and act on those alerts.
4. Vision-Based Quality Control
High-speed cameras paired with neural networks inspect every part at line speed, catching microscopic flaws invisible to the naked eye. Less scrap means lower cost of goods sold and stronger audit trails for medical, aerospace, and food-grade contracts.
5. AR-Guided Workforce Training
Head-mounted displays walk operators through changeovers and torque checks step by step. In-line prompts shave minutes from setup and ensure best practice across all shifts, tightening consistency as automation scales.
How to Launch Automation Without Disruption
Many leaders stall because the end state looks overwhelming. Success comes from starting small and expanding on wins:
- Select a pilot line. Choose a bottleneck where baseline data already exists.
- Connect and observe. Add IIoT sensors, stream secure data, and watch a full production cycle.
- Define success. Tie KPIs to fewer stoppages, lower scrap, or faster cycle times.
- Scale methodically. Replicate only after savings match or exceed pilot cost.
- Upskill continuously. Blend vendor instruction with GENEDGE’s online courses so that learning occurs in real-time, not just in classrooms.
Clearing Common Roadblocks
Every plant has hurdles that can derail an automation plan. Address them early to keep momentum alive.
- Legacy equipment lacks digital outputs ‒ retrofit sensor kits add connectivity without major cap-ex
- Data-security concerns ‒ encrypted gateways and zero-trust networks protect IP from shop floor to cloud
- Operator resistance ‒ early wins such as fewer midnight call-ins turn skeptics into champions
- Tight capital-state tax credits and performance-based vendor financing defray pilot costs
A short discovery session with GENEDGE identifies which of these hurdles matter most in your facility and outlines practical fixes that match your budget and risk tolerance.
Beyond the First Pilot—Building an Industry 4.0 Roadmap
Once a plant masters connectivity and predictive alerts, advanced options come into play:
- Edge AI that adjusts process parameters in milliseconds
- Autonomous mobile robots to feed lines without forklifts
- Blockchain traceability that tracks every component from supplier dock to customer install
GENEDGE guides manufacturers through each maturity level, ensuring that investments line up with strategic goals—whether that is penetrating a regulated market, slashing changeover time, or capturing real-time OEE across multiple sites.
Act Before Competitors Do
Smart factory automation has become the price of admission for reliable lead times and competitive costs. Facilities that move now will own the data—and the margin gains—that late adopters cannot recapture.
Ready to pinpoint your highest-value starting point? Contact GENEDGE for a plant-floor assessment. Our experts translate buzzwords into practical, ROI-focused steps that bring manufacturing automation solutions to life safely, scalably, and at a pace your workforce can absorb.