Before 2020, biopharmaceutical manufacturing was probably something most people didn’t think much about. But then COVID-19 became real, and suddenly, it was clear how important it is to have a quick, reliable way to make and obtain lifesaving medicines. Virginia stepped up, leveraging cutting-edge digital tech and analytics to speed up drug approvals from years to months.
Today, Virginia is emerging as a hotspot for pharmaceutical manufacturing, attracting a growing number of industry players. Big names like Civica and Phlow have set up shop in the state, joining pharma giant Merck & Co. (NYSE:MRK) and AMPAC Fine Chemicals (NYSE: AMPA), which produces active pharmaceutical ingredients and intermediates for the pharma and biotech industries. Granules Pharmaceuticals (NSE: GRANULES) recently opened a new packaging and distribution facility near Manassas in northern Virginia, further solidifying the state’s position in the biopharma landscape.
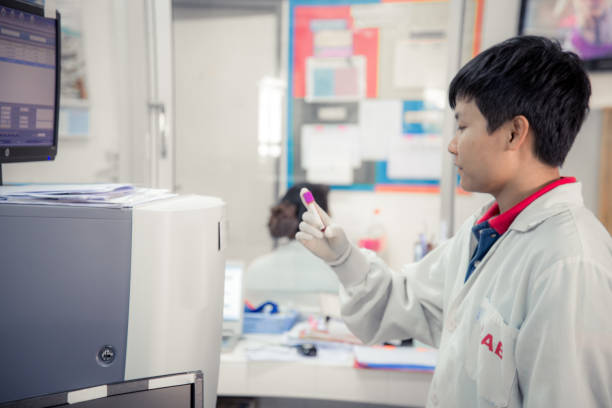
So, is there room to keep this momentum going?
Definitely. The key is to double down on using digital tools and analytics in manufacturing. This can turn today’s facilities into the “plants of the future,” boosting quality, speed, agility, and resilience.
- Learn how GENEDGE ignites success for businesses like yours in our small business manufacturing operations guide!
Just last year, the Virginia Economic Development Partnership (VEDP) announced the following initiatives to establish its place in domestic drug manufacturing, stabilizing the U.S. pharmaceutical supply chain:
- Engineered Biopharmaceuticals: They’re investing $6.1 million to grow their operations in Danville.
- PS Fertility: A new $1.4 million facility is coming to Albemarle County.
- Granules Pharmaceuticals: Expanding with a $12.5 million packaging plant in Prince William County.
- Civica: Building a $27.8 million lab testing center in Chesterfield County.
- Virongy Biosciences: They’re expanding their operations by $471,000 in Prince William County.
- Bode Technology: Elevating their viral diagnostic tech in Prince William County.
- Thermo Fisher: Putting $97 million into growing their bioanalytical lab in the Greater Richmond area.
In this blog, we cover:
- Digital tools and why they work for biopharma manufacturers
- Planning for digital transformation
- How GENEDGE is getting involved in the industry
Digital Tools and Their Impact
Digital tools (specifically, Industry 4.0 ones) are transforming how biopharma companies operate, making everything faster and more efficient. For example, these companies can monitor and optimize their manufacturing in real-time by integrating digital twins (virtual replicas of physical systems), advanced analytics, and automation techniques. This means they can catch issues before they become problems and make adjustments on the fly.
Planning Digital Transformation
Biopharma companies can follow different approaches, from implementing specific digital use cases to developing comprehensive “lighthouse” sites that set the standard for the entire organization. Implementing digital initiatives on a case-by-case basis can address immediate pain points, while lighthouse sites offer a holistic transformation that can be scaled across multiple locations.
Ultimately, the goal is to create a digitally-enabled manufacturing environment where decision-making is data-driven, biopharmaceutical manufacturing processes are automated, and quality is continuously monitored and improved. This proactive transformation approach will enable biopharmaceutical manufacturers to meet the market’s growing demands, mitigate risks, and drive sustainable growth.
A great example of successful digital transformation in manufacturing is how GENEDGE assisted RADVA Corporation with operational improvement consulting. Based in Radford, Virginia, RADVA makes protective and temperature-sensitive packaging for various industries, including electronics, furniture, and pharmaceuticals. When RADVA faced issues with lengthy press mold changeover times, they teamed up with GENEDGE and Virginia Tech’s Industrial and Systems Engineering Senior Design Team to tackle the problem.
Introducing new biopharmaceutical manufacturing process steps, making organizational improvements, and upgrading their equipment reduced mold changeover times. This collaboration led to some pretty impressive results: cost savings of $135,000, the creation or retention of five jobs, and a total dollar impact of $450,000.
About GENEDGE’s New BioPharmaceutical Resources for Virginia Manufacturers
GENEDGE has launched a Pharmaceutical Supply Chain Resources Program to help small and medium-sized pharmaceutical suppliers in Virginia improve their cybersecurity. Knowing the need for strong cybersecurity practices, this government-funded program helps small local manufacturers protect sensitive data and ensure compliance with industry standards. The program offers several free services, including:
• Comprehensive cybersecurity assessments
• Identification of potential vulnerabilities
• Implementation of necessary cybersecurity controls
• Ongoing support and guidance
In addition to the grant program, GENEDGE has created a Pharmaceutical Resources Page as part of their manufacturing operations support. This online resource helps suppliers understand and comply with cybersecurity requirements. The page is divided into three sections: High-Level Information and Resources, Framework Selection Assistance, and Framework-Specific Resources. This structure makes it easier for suppliers to achieve compliance by offering clear and actionable guidance.
Small and medium-sized pharmaceutical suppliers interested in this opportunity should contact David E. Bartlow Jr., PMP, PMI-RMP, at 571-317-5242 or email dbartlow@GENEDGE.org for more information on biopharma operational improvement consulting. Request a free assessment from us today!