It’s been over a decade since Industry 4.0.
Over a decade of disruptive technologies in all corners of manufacturing, from aerospace manufacturing to electronic manufacturing. Which technologies stand out in machining?
Industry experts at GENEDGE are seeing huge advancements, with tolerances now often measured in the microns. Virginia companies are maintaining environments that maximize performance and enable advanced quality inspection techniques that use visual software and Coordinate Measuring Machines (CMM). This technological shift has reinvented traditional practices and welcomes a new era of ingenuity and creativity.
Read more to add these five machining technologies to your list of operational must-haves. But if you’re new to the Industry 4.0 world, watch this video first.
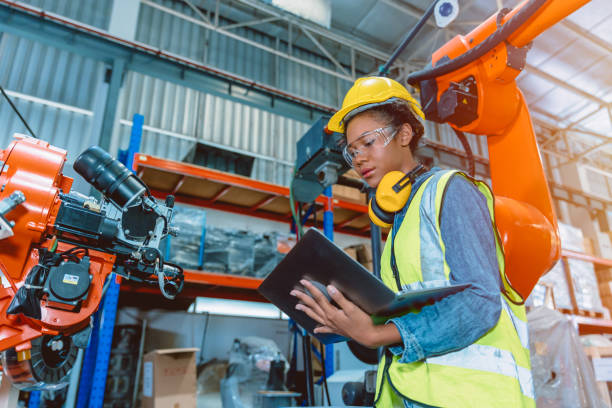
Table of Contents
- CNC Machining with Real-Time Data Analytics
- Adaptive Machining with AI
- Digital Twins for Machining Centers
- Augmented Reality (AR) for Machine Maintenance
- Blockchain for Traceability in Machine Parts
5 Top Industry 4.0 Machining Technologies
1. CNC Machining with Real-Time Data Analytics
At the heart of machining is Computer Numerical Control (CNC). Modern CNC controls now use probes to improve quality assurance, which cuts down on post-machining adjustments. This motivates better machining manufacturing process control and minimizes scrap.
Laser technologies also help link 3D printing with machining. Also, industrial pumps are adeptly distributing coolants, while interconnectivity among systems allows for real-time operation monitoring.
Example:
Automated Machine & Technology, Inc. (AMTECH) uses real-time data analytics to monitor and optimize their CNC machining manufacturing processes. They employ sensors to collect data on parameters such as spindle speed, feed rate, and tool wear, which is analyzed in real-time to adjust machining parameters for optimal performance.
2. Adaptive Machining with AI
Adaptive machining with AI enables real-time parameter adjustments based on sensor feedback and machine learning models. For example, AI algorithms can modify feed rates, cutting speeds, and tool paths in response to changes in material hardness or tool wear.
Example:
Danville Community College’s Precision Machining Technology Program incorporates adaptive machining techniques powered by AI. Their system uses machine learning algorithms to adapt machining manufacturing processes based on material properties and real-time feedback for better precision in manufacturing complex components.
3. Digital Twins for Machining Centers
Digital twins create exact virtual replicas of machine tools. These virtual models provide valuable insights into the machine’s configurations, processes, and tooling to help optimize operations without production disruptions.
With digital twins, machine shops can simulate and test production processes in a virtual environment to spot issues before implementation. Digital twins also facilitate workforce development through realistic training opportunities that help close the skills gap without taking physical machines offline.
Example:
Precision Machining Technology I at CTE Resource uses digital twins to create exact virtual replicas of machine tools. These virtual models provide valuable insights into machine configurations, processes, and tooling, helping to optimize operations without production disruptions.
4. Augmented Reality (AR) for Machine Maintenance
Augmented reality (AR) improves technician training through clear, visual instructions in real-time while they work in the field. When technicians can easily diagnose and repair machines more effectively, there’s less downtime and better outcomes.
Example:
New River Community College uses AR to enhance technician training. Their AR system provides real-time visual instructions, helping students diagnose and repair machines more effectively, reducing downtime, and improving outcomes.
5. Blockchain for Traceability in Machined Parts
Blockchain technology offers a secure and transparent way for supply chain companies to track production updates on a shared digital ledger. Everyone involved has access to a single source of truth and can check a product’s status and location instantly thanks to real-time, time-stamped transactions.
Example:
Commonwealth Center for Advanced Manufacturing (CCAM) in Virginia has implemented blockchain technology to ensure traceability in its supply chain. This system records each part’s history from creation to installation, providing a secure and transparent way to track production updates.
Launch Industry-Leading Technologies with GENEDGE
GENEDGE provides an essential bridge for companies seeking the best technologies in their machining manufacturing processes. GENEDGE streamlines the integration of technologies through industry 4.0 consulting services, working closely with Virginia manufacturers to assess existing capabilities and develop strategic action plans.
Get started with in-person training programs and shop floor implementation and unlock:
- Technology Roadmapping
- Automation
- Industrial and Collaborative Robots
- Intelligent Sensors
- Industrial Internet
- Cybersecurity
- Digital Twins/Simulation
- Big Data & Analytics
- Additive Manufacturing