Running a small metalworking shop in Virginia is tough. You’re juggling tight deadlines, demanding clients, and the constant pressure to stay competitive. One tool that can seriously level up your game? CNC machines. They’re not just fancy gadgets; they’re game-changers. Let’s break down the benefits.
What You Learn:
- What CNC machines are
- The 9 biggest advantages for your small metal shop
- GENEDGE’s next big metalworking event!
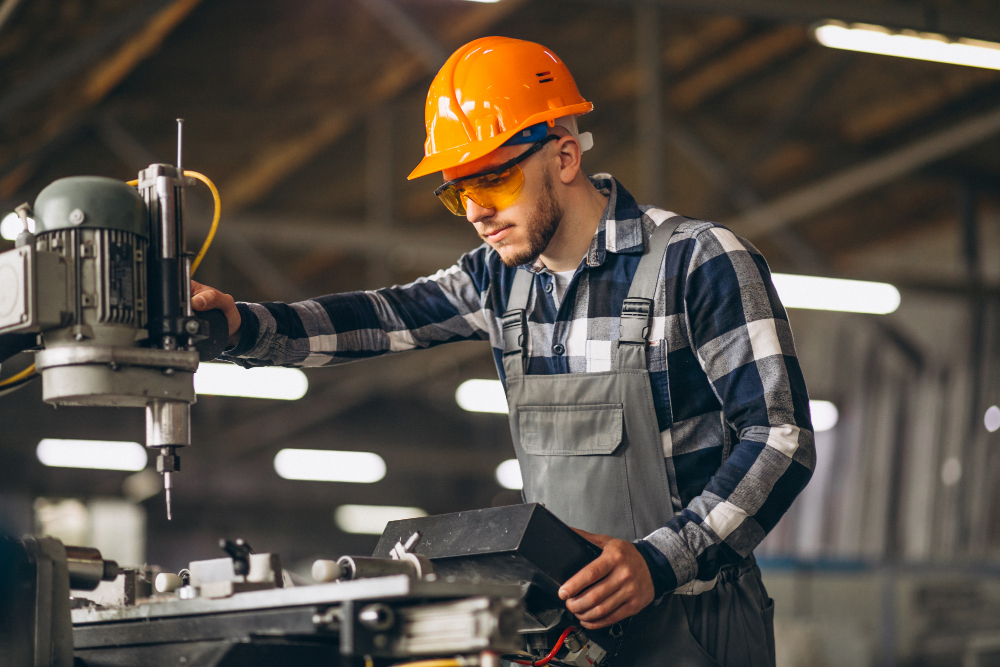
What Are CNC Machines?
CNC machining is a manufacturing process where computer software controls the movement of tools and machinery, allowing for precise and automated shaping of metal. This process is used with machines like lathes, mills, and routers, making it a versatile and essential part of modern metalworking.
Looking for a more cost-effective option? Read our recent blog about robotics in precision manufacturing.
Advantages of CNC Machines
Precision
Forget about relying solely on skilled hands (though those are still valuable!). CNC machines follow precise computer instructions, virtually eliminating human error. This translates to insane accuracy. A tiny imperfection in a part can be the difference between a smooth operation and a malfunction. CNC machines can consistently produce parts with tolerances down to 0.001 inches (that’s about 1/10th the thickness of a human hair!). Try doing that by hand every single time.
Production Speed
CNC machines don’t need coffee breaks or sleep. Once programmed, they can run 24/7, boosting your output. Large orders that would take days or even weeks to fulfill manually can be completed much faster with a CNC machine. Increased production speed means quicker turnaround times and the ability to take on more orders. This is especially beneficial for CNC machining for beginners who are looking to quickly increase their production capabilities.
Consistent Part Quality
CNC machines ensure every single piece is identical, which is crucial for everything from engine components to furniture hardware. Achieving perfect replication by hand is tough, but CNC machines guarantee this consistency every time.
Lower Costs
While CNC machines are an investment, they can save you serious cash in the long run. By bringing production in-house, you can lower outsourcing costs. CNC machines also lower material waste through optimized cutting paths and precise control, which saves you money on raw materials. Consulting with experts in manufacturing business growth consulting can further help you maximize these savings.
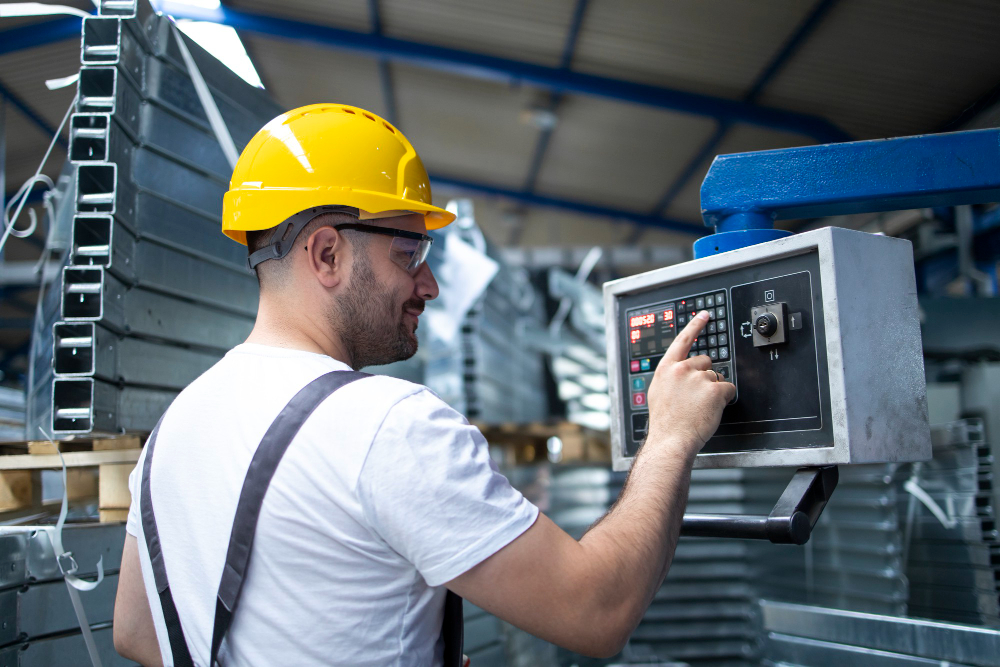
Complex Geometries
With advanced techniques like 5-axis machining, CNCs can create incredibly complex shapes and designs that would be impossible with manual machining. This opens up new possibilities for your shop, allowing you to produce intricate parts that meet customer demands and expand your market. Knowing CNC machining operations can help you use these capabilities to their fullest.
Depending on what works best for your metalworking operation, you may gravitate toward laser cutting methods over the traditional CNC. Read more about the differences between the two.
Makes Work Safe
CNC machines keep operators at a safe distance from cutting tools and flying debris, significantly reducing the risk of workplace accidents. Automated processes like IIoT and AI lessen the chance of human error, thereby minimizing accidents and injuries in the shop.
Lower Maintenance
While it require periodic maintenance, they generally have lower maintenance costs than manual machines. Fewer moving parts and automated lubrication systems contribute to reduced wear and tear, leading to lower operating costs and less downtime. Enacting robust manufacturing quality systems can ensure that your machines remain in top condition.
Material Versatility
CNC machines can work with a wide range of materials, from metals and plastics to wood and composites. This versatility lets you cater to diverse industries and customer needs, allowing you to adapt to changing market demands and explore new revenue streams. Investing in manufacturing workforce development can help your team stay updated with these versatile capabilities.
Lower Labor Costs
While the initial investment in CNC machinery can be significant, the long-term labor cost savings can be substantial. CNC machines require less direct human intervention than manual machines, allowing you to operate with a leaner workforce. This means better allocation of resources and increased profitability.
The Bottom Line: CNC Machines = Growth
For small metalworking shops in Virginia, CNC machines aren’t just a purchase; they’re an investment in growth. They boost productivity, improve quality, reduce costs, and open up new possibilities. If you’re serious about taking your shop to the next level, CNC technology is definitely worth considering.
GENEDGE helps small businesses implement functionally advanced CNC machines and helps capture ISO 9001 and SBA HubZone certifications for ongoing success. Join our upcoming Re-VAMMP workshop at Weyers Cave, VA on February 18th to discover how Metal Additive Manufacturing (MAM) can revolutionize your small shop. Learn from industry experts, explore cutting-edge technologies, and unlock new growth opportunities – register today!