Metal-cutting methods have come a long way. In the past, workers would spend long hours manually cutting metal with little accuracy. Now, laser cutting and traditional machining technology make exact cuts look easy for various types, thicknesses, and complex metal shapes. These manufacturing quality systems help manufacturers choose what suits their needs, balancing cost, speed, and accuracy for quality products.
Table of Contents
- The difference between traditional and laser cutting
- Different traditional methods
- Different laser methods
- How to figure out which is best
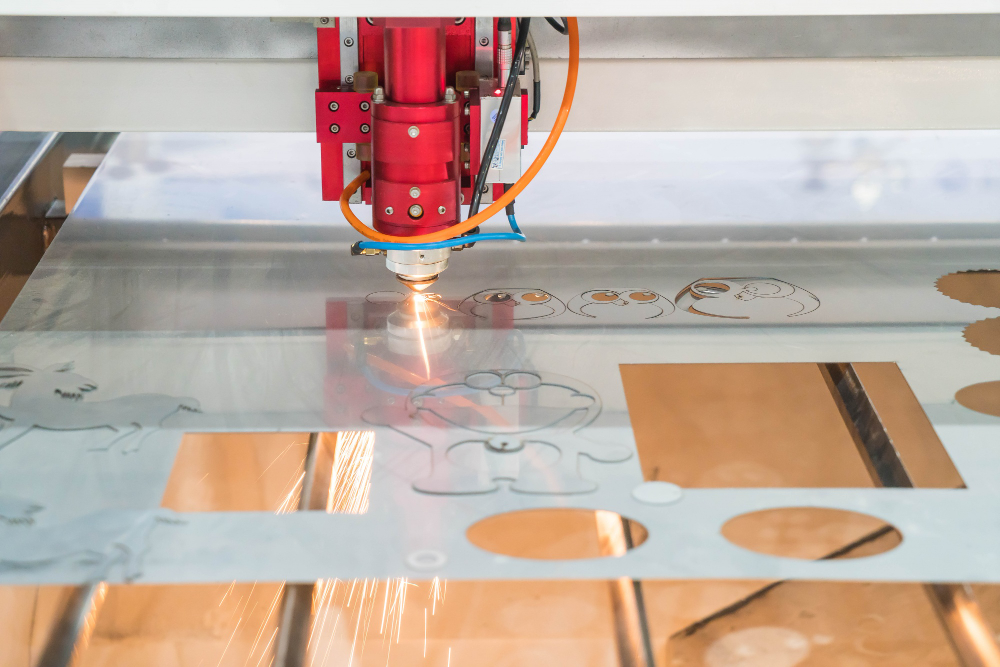
What is the difference between traditional cutting and laser cutting?
Traditional
Traditional cutting involves mechanical processes like sawing, shearing, grinding, milling, and machining, using standard tools like knives, scissors, saws, and drills. This method relies on “old school” physical contact between the cutting tool and the material, often resulting in wear and tear on the tools.
Pros of traditional cutting
- Simple
- Affordable
- Accessible
- Ready to use
- Maintains skills
Cons of traditional cutting
- Limited capacity
- Wear and tear
- Slower
- Prone to errors, which means money wasted
- Greater risk of injury
- Higher labor costs
Laser
Laser cutting uses a focused laser beam to melt, burn, or vaporize material using CO2 lasers, fiber lasers, and Nd: YAG lasers. It is a non-contact process, lessening tool wear since the laser beam does not physically touch the material. Because of its precision capacity on metals, plastics, wood, and even delicate materials like paper and textiles, laser cutting is highly effective for industries like automotive and aerospace.
Pros of laser cutting
- Affordable (depending on the brand)
- Easy to use (depending on the brand)
- Fast production times
- High precision
- Productive
- Durable components (fixtures and tools)
- Lower labor costs
- Material nesting efficiency
- No material contamination
- Tight tolerance cutting
- Cuts various material types
Cons of laser cutting:
- Can require complex programming (depending on the brand)
- Expensive energy requirements
- Restrictions on cutting material thickness over 25.4 mm
- Limitations with certain reflective materials like brass
Different Types of Traditional Cutting Machines
CNC Shearing Machines
CNC (computer numerical control) shearing machines are great for making straight cuts in big metal sheets. They work like scissors, with two blades moving back and forth to slice through the material. These machines are efficient and need little upkeep, making them reliable for straightforward jobs. However, they’re best suited for simple, straight designs, so they might not have the flexibility of other cutting techniques.
Punching Machines
Punching machines use a die and a press to cut holes or make indents in materials by exerting high force. They are perfect for creating repetitive patterns in thin materials, thanks to their quickness and accuracy. However, punching works best with thin materials and requires custom dies for unique patterns, leading to higher upfront costs and setup time.
Flame-Cutting Machines
Flame-cutting machines, also known as oxy-fuel torches, use a mix of fuel gas and oxygen to create a flame that can easily melt thick steel sheets. They’re a cost-effective choice for handling thick materials, but they do have drawbacks, like causing more thermal distortion and producing a wider cut than other methods.
Plasma Cutting Machines
Plasma-cutting machines use a fast-moving stream of hot, ionized gas to cut through metals like stainless steel and aluminum. These machines are great for delivering quick, clean cuts across different thicknesses. While they excel in speed and the quality of cut surfaces, they produce a lot of heat and noise, impacting safety and the working environment.
High-Pressure Water Cutting Machines
High-pressure water cutting, or water jet cutting, uses a fast stream of water mixed with abrasives to slice through tough materials. Because no heat is used, this method is very versatile, cutting different materials without changing them. However, cutting thicker materials can take longer, creating a wet work area. Maintenance costs can be high due to the wear and tear on the nozzles and pumps.
Different Types of Laser Cutting Machines
CO2 Laser Cutters
CO2 laser cutters are versatile machines that can cut various materials, including wood, acrylic, and fabric. They use a gas mixture to produce a laser beam, making them suitable for multiple applications, from industrial manufacturing to crafting.
Fiber Laser Cutters
Fiber laser cutters are ideal for cutting metals. They use a fiber optic cable to generate the laser beam, and they are known for their high efficiency and precision. These machines are commonly used in metalworking industries.
Crystal Laser Cutters
Crystal laser cutters produce the laser beam using synthetic ruby crystals. They are typically used for cutting and engraving hard materials like ceramics and glass.
Diode Laser Cutters
Diode laser cutters are often used for engraving and are compact and affordable, making them suitable for hobbyists and small businesses. They are especially effective on softer materials and offer a user-friendly experience.
UV Laser Cutters
UV laser cutters use ultraviolet light to cut materials with high precision. They are often used for cutting thin metals and plastics, providing detailed work without damaging the materials.
Hybrid Laser Cutters
Hybrid laser cutters combine different types of lasers to handle a variety of materials and thicknesses. This flexibility allows them to be used in diverse applications, offering greater versatility for complex cutting tasks.
How Do I Know What’s Best For My Manufacturing Operation?
Different machining methods cater to different industries based on their functions. In the food and beverage sector, maintaining hygiene and precision is everything. Depending on their food manufacturing training, laser cutting is favored for precise, clean cuts that minimize contamination. Traditional methods like mechanical shearing are cost-effective for simpler parts without direct contact with food.
To find out which methods work best for your business, think about the material types you’re working with. Is it metal, which is better suited for CNC milling and turning? Is it plastic, which better suits laser cutting or waterjet cutting?
Some companies even upgrade traditional methods to more advanced versions. For example, Zenith Precision Machining, a GENEDGE partner in the southwest Virginia location, uses CNC horizontal machining, CNC vertical machining, and 5-axis precision machining to produce complex parts. Their capabilities also include turning and turn-mill centers, which allow them to machine parts with tight tolerances and intricate features.
Here are some other things to consider:
- Precision requirements
- Production volume
- Complexity of design
- Cost
- Lead time
- Flexibility and scalability
- Environmental impact
- Your team’s expertise and training
- Safety
Interested in growth strategies for manufacturing companies? A manufacturing consultant at GENEDGE can formulate a detailed plan to fit the right methods and technology into your processes.