The constant pressure to improve and stay productive while lowering costs is part of the job when you’re a machining manufacturer in Virginia.
On a global scale, the CNC market is all but stopping anytime soon—expected to grow from USD 100.78 billion in 2024 to USD 146.65 billion by 2029, with an annual growth rate of 7.79%. This increase is fueled by new economic demands and the trend toward mass customization of products.
At the same time, the industrial Internet of Things (IIoT) is making its mark. IIoT technology, which uses sensors to collect and share data, gives manufacturers the power to optimize production and reduce downtime. The future looks bright for CNC machining and IIoT, according to Grand View Research, with the latter’s market size predicted to reach $1.11 trillion by 2028.
Like other Industry 4.0 technologies, capitalizing on IIoT should undoubtedly help companies achieve better production results and possibly move towards “lights-out” manufacturing.
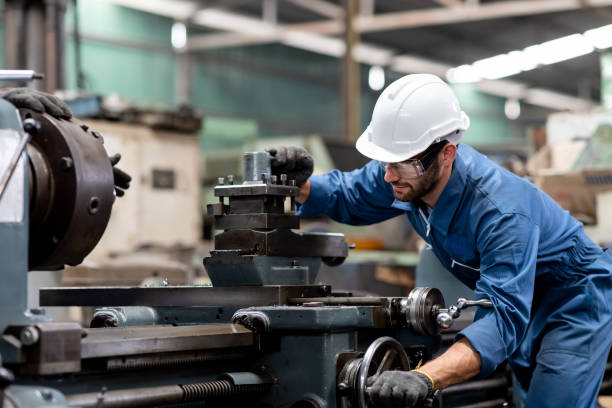
In this blog, you will learn:
- Why IIoT is growing
- How IIot makes machining production more efficient
- How IIoT enables predictive maintenance
- How IIoT helps quality control
- How Virginia manufacturers can leverage IIoT
Why IIoT is Taking Off
CNC machining, which displaced old manual lathes, milling, drilling, and traditional machines, already uses computer programming for better precision. But what makes IIoT especially vital now is its ability to optimize these highly automated systems further.
One of the big game-changers is predictive maintenance. Being able to foresee potential equipment failures before they happen and fix issues before they turn into expensive downtime is exactly what IIoT (Industrial Internet of Things) offers. By keeping a constant watch on machine health and performance, IIoT systems give manufacturers real-time data and insights. Production runs smoother, and workplace safety gets a big boost because there’s less risk of machine accidents.
Small and medium-sized manufacturers sometimes underestimate the risk of cyberattacks, thinking they’re too small to be targeted. However, a video in the Heroes of American Manufacturing series highlights AMG Engineering and Machining, an Indianapolis-based company that is part of the Manufacturing Extension Partnership (MEP) and takes cybersecurity seriously.
President Ted Gary notes, “Today’s challenges have forced a lot of us to go beyond what we thought would be necessary to have a secure environment.” Through proactive cybersecurity measures, AMG unlocked new business opportunities, showing how vital IIoT and security are for modern manufacturing success.
Bringing IIoT into CNC operations doesn’t push operators out of their jobs; it actually empowers them. Instead of worrying about losing their positions, workers can use this technology to learn new skills and handle more complex tasks. When work is more technologically advanced, it’s most likely to be more productive.
IIoT Makes Machining Production Efficient
Because IIoT technology eliminates manual data collection across the shop floor, operators can focus on higher-value tasks, like managing more machines. Autonomously collected production data ensures managers can trust its accuracy. Here’s how:
Overall Equipment Effectiveness (OEE)
Tracks variables affecting operator performance, maintenance, and continuous improvement. As equipment utilization increases, so do efficiency and productivity.
Data Collection
IIoT enables manufacturers to gather data from various machines and equipment in the factory. This data helps identify trends, pinpoint areas for improvement, and optimize production processes to ensure consistent quality.
Real-Time Monitoring
This provides critical metrics to monitor production status in real time. This capability allows for the easy replication of production processes, automated auditing, and timely issue resolution.
Remote Control
Wireless connections between machines and the internet facilitate remote monitoring and control, significantly reducing downtime. Additionally, IIoT-enabled machines can communicate with each other, promoting a coordinated and streamlined production process.
Proactive Problem Solving
One of the most impactful advantages of IIoT is the ability to address problems before they occur. This proactive approach reduces unplanned downtime and boosts overall productivity.
IIoT Enables Predictive Maintenance
Predictive maintenance is a proactive approach that helps manufacturers avoid equipment failures and downtime. IIoT is increasingly important in predictive maintenance via real-time data collection and analysis. Sensors calculate vibrations, temperature, acceleration, displacement, and sound frequencies to detect potential issues before they cause disruptions.
With IIoT, CNC companies can move from preventive to predictive maintenance strategies. IIoT sensors and advanced edge computing enables maintenance teams to unlock machine performance and condition data to inform when maintenance activity should occur.
Applications of IIoT-Enabled Sensors
These sensors find application in various areas, such as:
- Monitoring compressors, motors, robotic equipment, transport vehicles, and conveyors.
- Keeping track of machine functioning conditions.
- Identifying potential future failures for safe corrective action.
IIoT is Great For Quality Control
Good quality management in machining means keeping an eye on and controlling different parts of the process and machines that can affect the quality of the products.
IIoT makes this much easier by giving us real-time data and smart insights.
Here’s How:
Automated Inspection Systems
IIoT sensors embedded in CNC machines continuously monitor critical parameters such as dimensions, surface finish, and tool wear. This data enables automated inspection systems to instantly detect deviations from quality standards so that only conforming products move forward in the production line.
Environmental Monitoring
Factors such as humidity, air quality, and temperature can significantly affect machining operations. IIoT sensors monitor these environmental conditions in real time, ensuring the manufacturing environment is maintained within optimal ranges. For example, high humidity levels can cause material degradation and inaccuracies in precision machining.
Machine Utilization Tracking
IIoT devices help accurately track the utilization of CNC machines. This data helps managers identify patterns that could indicate quality issues, like frequent tool changes or unscheduled maintenance.
Tool Condition Monitoring
Using IIoT-enabled sensors, manufacturers can continuously assess the condition of cutting tools. Parameters like vibration, temperature, and acoustics provide insights into tool wear and tear. Fast interventions, such as tool replacement or reconditioning, can prevent quality defects and prolong tool life.
Data-Driven Decision Making
The vast amount of data collected through IIoT devices aids in making informed decisions that enhance quality. Advanced analytics can identify trends, pinpoint root causes of defects, and suggest optimal machine settings.
How Can Virginia Machining Manufacturers Take Advantage?
- Connect all machine assets, old and new.
- Alter equipment used to unlock more capacity.
- Develop a continuous improvement program with real-time feedback.
- Use real-time workflow automation with accurate production data.
Partnering with a top consultant is the way to go to devise strategies fast in the already-booming Virginia machining sector. You’ll get expert advice and custom strategies to ramp up efficiency and drive innovation.
GENEDGE can help you tap into that growth and stay ahead of the competition with a free assessment.