TL;DR IoT is changing CNC machining in a big way. Real-time data and connected machines help manufacturers spot problems faster without making things complicated. This blog walks through how it works and how you can get started.
The global CNC machining market is growing fast, expected to hit $140 billion by 2029. As demand for precision parts grows, more and more manufacturers are using IoT and real-time analytics to stay ahead. Why? Because old-school manual checks and delayed reports just can’t keep up.
Virginia manufacturers are already embracing this shift. Programs like GENEDGE’s Virginia Smart Manufacturing Accelerator are helping small and mid-sized shops adopt IoT and real-time monitoring tools faster, with hands-on training and consulting support.
Today, companies are using real-time production monitoring and smart sensors to make better decisions, faster. Whether you’re running two machines or two hundred, the goal is the same: make less errors, be more efficient, and unlock new capacity using live data.
Read more on what our manufacturing business consulting experts have to say.
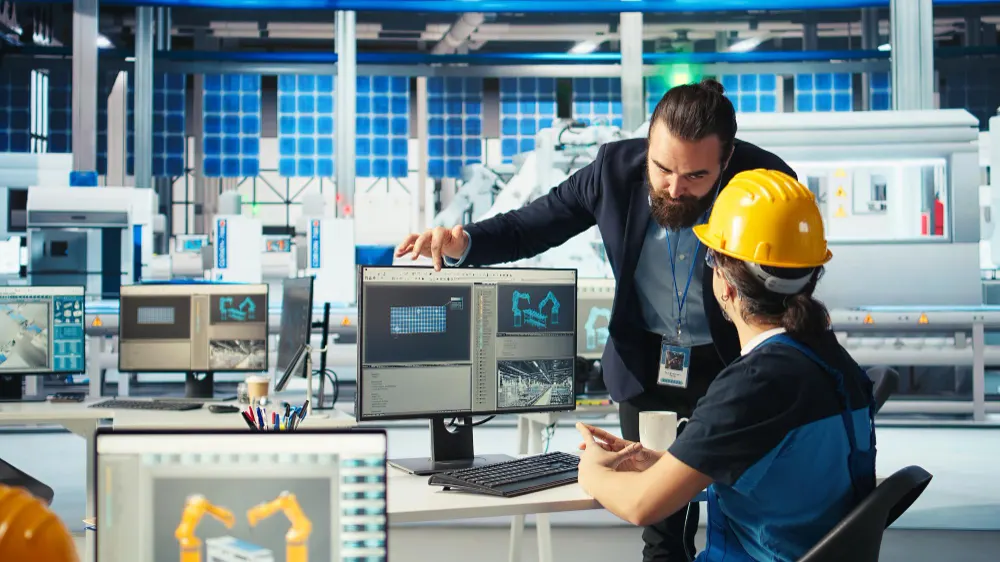
Table of Contents
- What Is IoT in CNC Machining?
- Why Real-Time Monitoring Matters
- How Data Improves Accuracy and Output
- Starting Small: What You Need to Begin
- Support from GENEDGE
What Is IoT in CNC Machining?
IoT (Internet of Things) in CNC machining means your machines are constantly sharing data about temperature, vibration, tool wear, performance, and more. With sensors installed directly on the machine or through retrofitted modules, data flows to a central dashboard in real time.
This visibility helps operators and managers:
- Monitor performance 24/7
- Spot small issues before they become downtime events
- Improve consistency across shifts and runs
- Make smart, fast decisions using real-time production monitoring
Why Real-Time Monitoring Matters
You can’t improve what you can’t see. Real-time production monitoring makes hidden problems visible. Think of it like a live health tracker for your machines.
What you can track:
- Machine uptime and idle time
- Cycle times and part counts
- Alarm states and stoppages
- Operator productivity by shift
With that level of insight, manufacturers can make continuous improvements backed by real numbers, not guesswork.
In fact, through recent partnerships with Virginia Tech and Old Dominion University, Virginia is actively training its workforce on using IoT tools to monitor CNC machine health and performance.
Real-time analytics for CNC machine performance also makes it easier to benchmark across teams, identify training needs, and prioritize maintenance.
How Data Improves Accuracy and Output
In order to improve CNC machining accuracy with data, you need to close the feedback loop. Instead of reacting after parts go off-spec, real-time monitoring lets you catch shifts in performance as they happen.
For example:
- A spike in spindle vibration might flag a worn tool
- Changes in ambient temperature can impact part tolerance
- Subtle feed rate changes could make the surface finish quality lower
When you monitor these inputs in real time through CNC machining optimization, you can adjust right away or even automate corrections.
The result: fewer rejected parts, more consistent quality, and higher customer satisfaction.
Starting Small: What You Need to Begin
You don’t need a massive investment to get started. Many CNC machines already support IoT connectivity, or can be upgraded with plug-and-play sensors.
A basic setup usually includes:
- Machine sensors or data collectors
- A gateway or edge device
- Cloud or local dashboards for analytics
From there, you can grow your system at your own pace. The best way is by starting with high-impact use cases (like tracking downtime or tool wear) and scaling from there.
Want to See Smart Manufacturing in Action?
Join us at the VSMA & CVCC Smart Manufacturing Workshop on May 6th in Lynchburg, VA, for hands-on demos, expert insights, and real-world applications of IoT and digital manufacturing. It’s a great chance to connect, learn, and get inspired.
Register here →
Support from GENEDGE
Not sure where to start? GENEDGE offers custom solutions for industrial engineering to help Virginia manufacturers modernize their operations.
No matter what your business is trying to do, like hoping to improve machine utilization, eliminate scrap, or build a smarter workflow, we’ll help you find the right solution for your floor. All backed by data, not guesswork.