Small, understaffed, under resourced, outperformed? It’s never too late to automate.
As change accelerates, Virginia manufacturing companies—even small ones—are quickly catching on that they need to develop a new approach toward infrastructure efficiency. Automating IT operations will refine your processes no matter the complexity of your existing systems or your current modernization stage. When team and budget sizes are small, practicing automation can be the perfect way to work across technical disciplines and enact an actionable project management style.
What you’ll learn:
- What low-cost automation is
- Why automation leans on lean manufacturing
- How to automate in six ways
- Real examples from fellow VA (and other) manufacturers
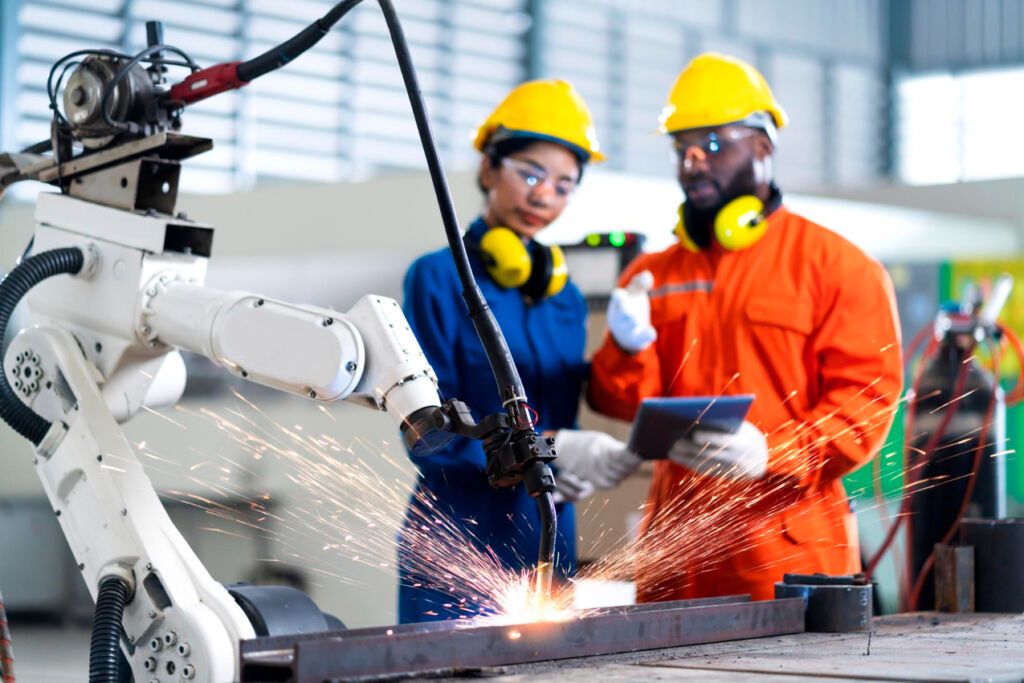
What is low-cost automation?
Low-cost automation is a strategic yet budget-friendly approach to being more productive without larger-than-life investments or extensive system overhauls. The emphasis here is on incorporating simple, effective technologies into existing operations to streamline processes, improve energy management in manufacturing, and lower the reliance on manual labor.
For example, manufacturers can deploy low-cost robots made with plastic components to handle lighter tasks, typically managing payloads around 2 kg with tolerance levels of +/- 1 mm. Though these robots aren’t suitable for high-precision functions in industries like metalworking, they excel in more straightforward roles like sorting and packaging light items or performing safety-related duties within a facility. Recent sensor technology and software innovations make low-cost automation more accessible, allowing small manufacturers to integrate these solutions without facing the steep costs associated with high-end collaborative robots.
Why go lean?
Focusing on continuous improvement, lean manufacturing can readily incorporate low-cost automation by integrating budget-friendly technologies, like simple robots and improved sensor systems. This helps manufacturers achieve their lean goals without lofty investments. Lean manufacturing consulting can provide valuable insights and guidance on implementing these changes across diverse processes.
Six Ways to Low-cost Automate
1. Cloud-Based MRP/ERP Systems
Cloud-based Manufacturing Resource Planning (MRP) or Enterprise Resource Planning (ERP) systems, like MRPeasy, are a budget-friendly way to streamline your business operations. Since these systems operate online, you don’t need to worry about spending money on expensive hardware.
They can easily grow with your business, adapting to your future needs. These systems manage everything from inventory and production schedules to customer orders. For a more personalized, hands-on approach, seek lean manufacturing consulting with a professional.
2. Low-Cost Automation Tools
Plenty of affordable automation options can greatly boost your efficiency. With a consultant’s help, start small with programmable logic controllers (PLCs) and robotic arms, focusing on the most important tasks first. These tools help cut down on the manual work that causes frequent human error.
3. Phased Automation
Instead of diving straight into a full-scale automation overhaul, small manufacturers can take a step-by-step approach. Begin by automating the most time-consuming tasks and then slowly incorporate additional automation as the budget permits. This way, you can lower financial risk and make tweaks based on early outcomes.
4. Open-Source Software
Open-source software can revolutionize how small manufacturers handle automation without breaking the bank. With tools like LinuxCNC for CNC machines and OpenPLC for automation control systems, businesses can access powerful capabilities for free. These solutions are backed by vibrant communities that offer abundant support and resources to help you along the way.
5. Government Incentives and Grants
Governments often provide incentives and grants to help small businesses embrace automation. Look into local and federal programs that could fund your projects, easing those initial costs and making automation more achievable. Check out the SBA’s website.
6. Educational Institution Collaborations
Partnering with local universities and technical schools offers small manufacturers a golden opportunity to tap into valuable research and fresh expertise. These institutions often have automation-focused programs and can provide valuable internships or collaborative projects that mutually benefit both parties involved.
How small manufacturers automate
They’re using 3D printing and robotics.
Somic America Inc., a leading automotive component manufacturer in Wytheville, Virginia, has integrated automation by leveraging 3D printing and robotics. By collaborating with Plex, they modernized infrastructure using ERP and MES platforms for streamlined operations and improved data accuracy. Automation has enabled a fully integrated quality management system for consistent product quality by cutting non-value-added activities.
They’re using it for assembly and inspection.
Cadence Inc., headquartered in Staunton, Virginia, designs and integrates custom automation equipment for assembly and inspection. Its vertical integration approach allows it to control every aspect of product development and manufacturing, incorporating technologies like metal injection molding, machining, and laser processes—all vital to the supply chain.
They’re building new CNC machines.
Triangle Precision, a precision machining company in Kettering, Ohio, has successfully leveraged automation with the help of FastLane, a part of the Ohio MEP and MEP National Network™. FastLane guided Triangle in automating its new three-axis CNC machine by incorporating an articulating arm and conveyor system. This enhancement allowed them to implement lights-out machining.
Automate success with GENEDGE
GENEDGE offers growth strategies for manufacturing companies to help you get the most out of the latest manufacturing technologies. Our experts work closely with you to pinpoint areas full of potential and guide you through the difficult transition into Industry 4.0. Whether you’re trying to cut costs, streamline processes, or simply modernize your operations, GENEDGE’s focus on lean manufacturing practices means you’ll find ways to make viable changes to boost your bottom line.
Contact GENEDGE for a custom assessment and see how we can help your business grow through smart, affordable automation.