Lean manufacturing, or Lean production, is fundamentally about streamlining and optimizing various practices, processes, and habits within an organization, mainly focusing on those that generate customer value. This methodology empowers teams to work more efficiently, foster innovation more quickly, and maximize the value delivered to clients. If you’re an organization that wants to adopt Lean manufacturing principles for sustainable growth, this is your guide to getting started.
Whether you are new to the concept or seeking to deepen your understanding, you’ll need to familiarize yourself with the history and core principles of Lean, like Kanban boards. However, simply embedding a handful of Lean practices into your operations is not enough to transform your organization into a Lean one.
REQUEST A Half-Day Lean Process Improvement Class FOR YOUR TEAM.
According to Jim Womack and Dan Jones, the renowned authors of The Machine That Changed the World, in order to truly realize the benefits of Lean manufacturing, we have to perform a holistic overhaul of the entire organizational structure.
“If individual breakthroughs can be linked up and down the value chain to form a continuous value stream that creates, sells, and services a family of products, the performance of the whole can be raised to a dramatically higher level,” they wrote.
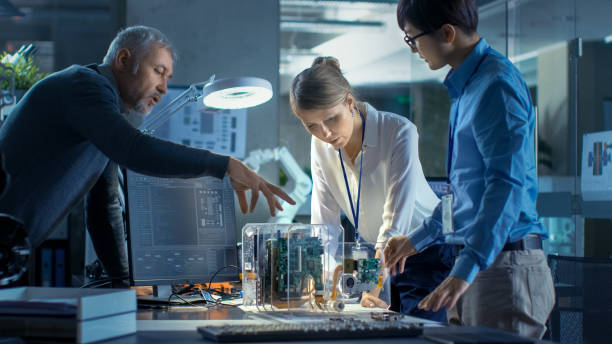
The First Stages To Turning Lean
Realizing the benefits of Lean manufacturing—improved efficiency, flexibility, and customer responsiveness—starts with gaining alignment across the organization. At the heart of this alignment is understanding the “why” behind your actions.
As Simon Sinek highlighted in his How Great Leaders Inspire Action TED talk, comprehending the motives behind your organization’s shift towards Lean methodologies is everything for success. Whether it’s to enhance customer connection, foster innovation, achieve profitability, or secure a competitive edge in the future economy, finding and communicating this reason compellingly is vital to building your lean roadmap.
Find (and Eliminate) Your Wasteful Processes
Jim Womack and Dan Jones, through extensive research at the Lean Enterprise Institute, identified that achieving Lean at the enterprise level requires balancing the needs of individuals, functions, and the company itself. Individuals seek job security and satisfaction; functions aim to preserve and enhance organizational knowledge, requiring a shift towards agile, cross-functional teams; and companies pursue cost control and benefit analysis, valuing agility and Lean principles.
Traditional organizational structures often struggle to meet these diverse needs simultaneously, leading to conflicts that hinder Lean implementation. However, solutions have emerged, enabling organizations to achieve a balanced approach that addresses the needs of individuals, functions, and the entire company.
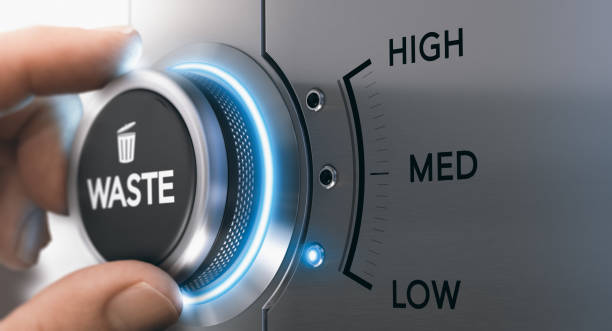
Identify Your Lean Leader
Implementing Lean practices can be challenging, especially in environments resistant to change. Having a leader for Lean—a visible and vocal advocate—can significantly facilitate this transformation. This individual celebrates milestones, generates discussions, and motivates others to persist despite challenges. Whether this champion is a top executive or originates from a grassroots effort, their role is important in endorsing Lean initiatives and ensuring its principles are practiced and valued within the organization.
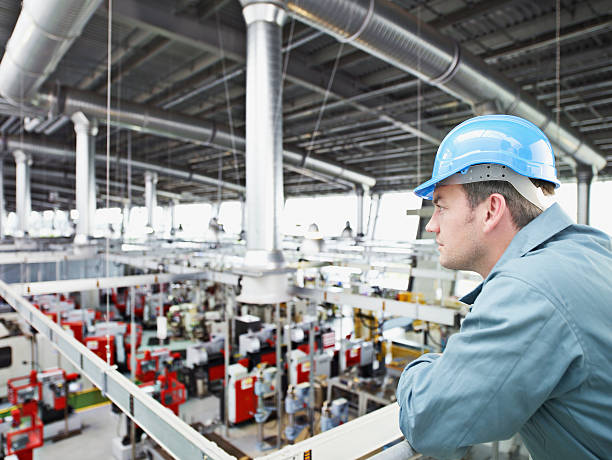
Transcend the Basics
Mastering and implementing Lean concepts requires a shift in mindset, which may seem counterintuitive at first. Strengthen your knowledge of Lean through reading, learning tools, and techniques, and create an environment of shared learning to build a solid foundation. Organizations often benefit from external Lean coaches who can facilitate workshops, offer guidance, and share valuable resources to inspire a successful Lean implementation.
Map Your Value Stream
A fundamental exercise in Lean transformation is value stream mapping. This process allows you to visualize how value flows through your organization, identifying opportunities for improvement. It fuels critical discussions that pave the way for positive changes, making room for a smoother transition to the Lean mindset.
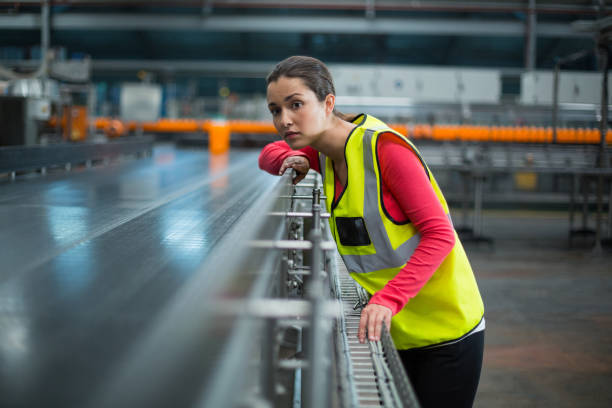
Experiment, Experiment, Experiment
Lean manufacturing embraces failure as a learning opportunity rather than a setback. Cultivating a culture that experiments, learns from failures, and quickly adapts is key to innovation and growth. Companies that encourage this mindset are more likely to innovate successfully and come out on top. The tech sector is an excellent example—companies are rapidly commercializing the lean mindset across all operations for sustainable growth.
Perform at a Higher Level and Grow
Implementing Lean manufacturing principles within your organization shouldn’t be a race against time but a carefully considered process. This slow and intentional approach helps to ensure that everyone within the organization grasps the foundational concepts of Lean, thereby reducing the risk of failure due to misunderstanding or shallow implementation. Remember, aligning around your “why” and sharing Lean thinking and principles across your organization are the keystones for a successful Lean transformation. If you’re ready to start this journey and want to ensure that your Lean manufacturing implementation is built on a solid understanding and strategic alignment, contact GENEDGE lean manufacturing consultant today.