Put yourself in this hypothetical scenario: After a particularly messy batch run of salsa that ended with more sauce on the floor than in the jars, you find yourself reflecting on where you went wrong—your processes.
Because right now, your current method of hand-transferring ingredients between stations while being as clean and quick as possible is a recipe for disaster.
But then you invest in automated pumps and batching systems, and suddenly, your production runs smoothly. This new workflow reduces the amount of time you spend cleaning up after cooking.
This is process optimization at its finest—and just like those newfound kitchen tools, the right equipment and strategies can revolutionize operations in your food processing and manufacturing business.
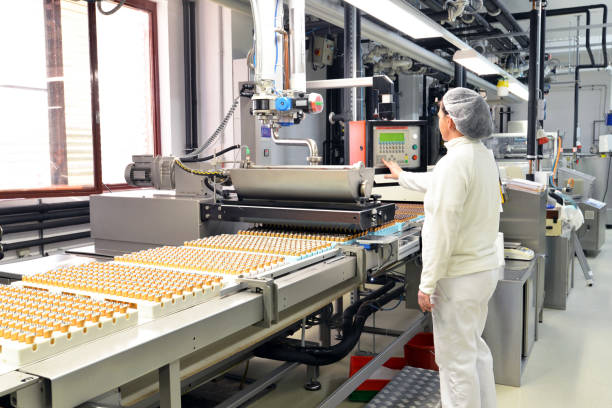
In This Blog We Discuss:
- What is Process Optimization?
- Steps to Optimize Food and Beverage Processes
- Process Optimization Methods
- Benefits
What is Process Optimization?
Process optimization is systematically analyzing and refining operations to eliminate inefficiencies and improve productivity. This practice evaluates routine procedures to identify areas where time, resources, or materials are wasted, freeing up space for manufacturers to streamline their workflows, boost output, and maximize profitability.
While it may sound easy, executing process optimization that actually works for you can be complex and resource-intensive. However, using established optimization frameworks can make it easier by pinpointing operational gaps and giving actionable solutions. Through process optimization, businesses can reclaim valuable time and financial resources, channeling them toward initiatives that drive greater impact and inspire growth.
Steps to Optimize Food and Beverage Processes
Process optimization typically follows a consistent framework, though food manufacturers should adjust these steps to fit their food processing and manufacturing needs.
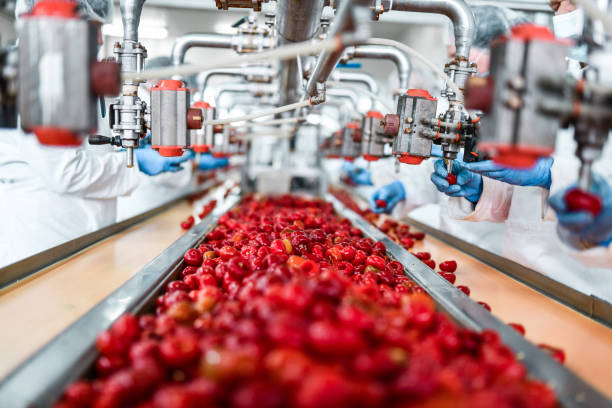
Step 1: Set Goals
To get anywhere, you need clear, measurable goals. Focus your goals on key initiatives like:
- increasing revenue
- lowering costs
- improving customer and employee relationships
Which elements of your production can benefit from process optimization?
Use specific targets instead of vague statements; for example, aim to “increase sales of Product X by 20%” rather than just “develop a better process.” Tie your goals to measurable metrics like upping your Net Promoter Score® (NPS) from 50 to 75. To keep things manageable, limit your goals to three related targets.
Step 2: Find What Works; Ditch the Rest
Now’s the time to dissect your processes and find what drives production. Conduct a complete analysis to distinguish between facilitators and bottlenecks. Are outdated mixers or equipment causing delays? Is human error during packaging disrupting your workflow? Be honest and take note.
Step 3: Build New Processes
Use what you’ve learned from your analysis to create better food processing and manufacturing workflows. Change one process at a time so you can clearly see the impact and monitor ongoing problems.
Step 4: Measure the Impact
As you start introducing new processes, watch how they affect productivity and costs. Collecting this data will help you make informed decisions for future changes and ongoing improvements.
Step 5: Keep It Going
Process optimization is always ongoing. As tech evolves, regularly assess your workflows for new opportunities to improve.
Process Optimization Methods
There are numerous strategies for process optimization, each with its unique emphasis on improving workflows:
- Six Sigma targets quality control and process variation reduction like blending and bottling.
- Kaizen, or continuous improvement, focuses on eliminating waste by streamlining operations like ingredient handling and packaging.
- PDSA (Plan, Do, Study, Act) promotes iterative cycles of improvement that can be applied to refining recipes or adjusting cooking time in the factory.
- Value Stream Mapping visually represents a product’s journey (from raw material acquisition to final packaging), identifying waste and efficiency opportunities.
Most of the above examples are types of lean manufacturing processes. Lean manufacturing is a production process based on the ideology of maximizing productivity while cutting waste to create a stable manufacturing operation. “Waste,” in this sense, is anything that doesn’t add value or profit.
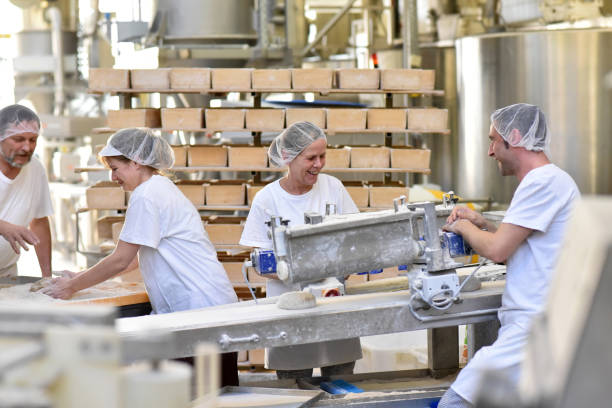
What You’re Ultimately Getting:
- Less Risk
- Better Quality Control
- Better Resource Management
- Better Costs
GENEDGE is always offering growth strategies for manufacturing companies to help Virginia food and beverage manufacturers take the reigns on their operation. Click here to see upcoming virtual lean events or get a no-cost assessment.