Small to midsize machine shops do not = assembly lines.
We deal with a whole different world of high-mix, low-volume production. So, while the core principles of lean manufacturing are incredibly valuable, we need to adapt them to fit our unique needs.
That’s why we need to think strategically – a lean toolkit designed specifically for the challenges and opportunities of machining. In this guide, we’ll explore practical strategies that go beyond the basics, helping you go lean in your machining operations.
REQUEST A Half-Day Lean Process Improvement Class FOR YOUR TEAM!
Table of Contents:
- What is Lean Machining?
- 9 Key Lean Machining Principles
- Lean Tools to Use and Not to Use
- Register for our Danville Lean Six Sigma Black Belt Course!
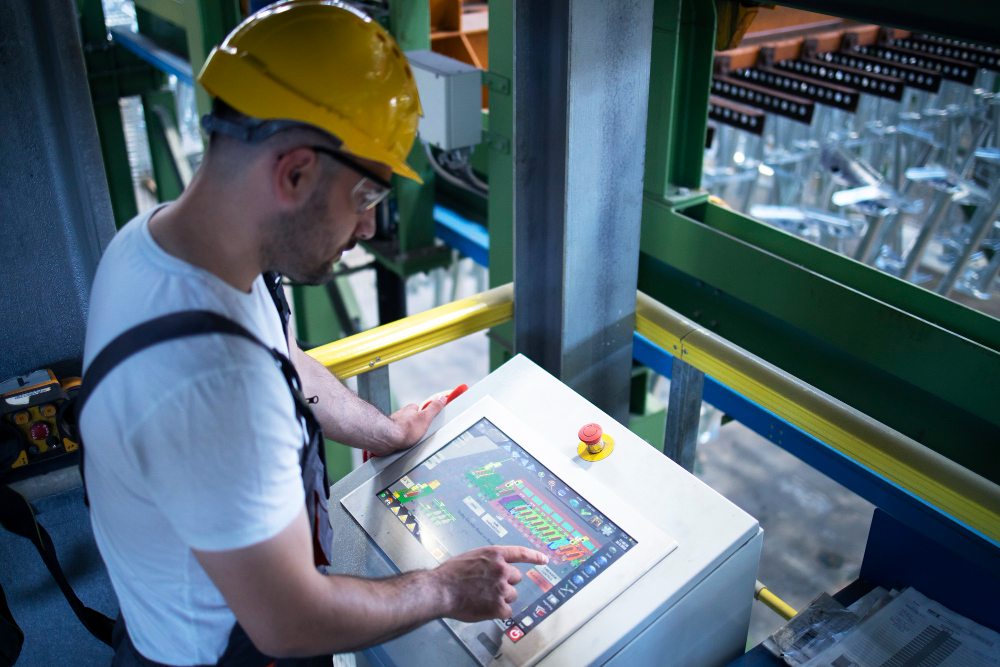
What is Lean Machining?
Lean manufacturing in the CNC shop is all about maximizing productivity by minimizing waste and fine-tuning your entire operation to run like a well-oiled machine (pun intended!).
The roots of lean manufacturing go back to the Toyota Production System, which identified eight major categories of waste (often remembered by the acronym DOWNTIME):
- Defects
- Overproduction
- Waiting
- Non-utilization of talents
- Transportation
- Inventory excess
- Motion waste
- Excessive processing
9 Key Lean Machining Principles
1. Segment Your Product Mix
Categorize your products based on volume, demand, and margin. “Runners/Repeaters” are good for medium-to-large batch jobs with long-term agreements. “Strangers” are one-offs, repairs, and prototypes – small batches with unique requirements. This segmentation helps you organize for productivity (5S) by setting up dedicated areas for different product types. This also plays into Just-in-Time Production (JIT), as you can better anticipate and manage the flow of materials for each segment.
Want to learn more about 5S? Read this Blog: Benefits of 5S in a manufacturing environment.
2. Rationalize Your Product Mix YoY
Annually review your product portfolio. Eliminate unprofitable or low-margin items. Focus on what brings in the most value. Don’t be afraid to let go of the “cats and dogs” that drain resources. This aligns with the lean principle of continuous improvement by constantly refining your offerings for maximum profitability.
3. Split Your Shop (If Possible)
Consider dividing your shop into two: one for Runners/Repeaters (Shop 1) and one for Strangers (Shop 2). Shop 1 focuses on efficiency and optimized flow for larger batches. Shop 2 is a quick-turnaround operation, equipped for rapid prototyping and small-batch production using flexible automation and multi-tasking machines. This separation allows for strategic plant layout, optimizing material flow, and minimizing transportation waste for each product type.
4. Go For a Cellular Layout in Shop 1
If you currently use a process layout (similar machines grouped together), consider switching to a cellular layout for your Runners/Repeaters. Group machines are needed for specific part families in cells. This dramatically reduces material handling and improves workflow, directly addressing motion waste and transportation waste. Within these cells, prioritize consistent implementation of periodic and preventive maintenance to minimize downtime and keep things running smoothly.
5. Get Right-Size Non-Machining Processes
Don’t just focus on machining times. Look at manual processes (sawing, inspection) and non-machining processes (heat treatment, plating, washing). Bottlenecks here can kill your overall efficiency. Bring supporting processes into the cell where possible, reducing waiting time and improving process flow.
6. Combine Processes with Multifunction Machines
Instead of just chasing higher metal removal rates, consider investing in multifunction machines that combine consecutive operations. This reduces setup times and material handling, especially for part families. This directly tackles excessive processing and improves tooling efficiency by minimizing tool changes and optimizing cutting parameters. Be smart with machining parameters and processes to maximize the value of these machines.
7. Standardize Routings and Simplify the Process with AI
Critically examine and standardize part routings within families. Use AI and ML to eliminate variations in machines, sequences, fixtures, tools, and gauges. Aim for a linear, assembly-line flow whenever possible. This minimizes motion waste and waiting time. You can also use AI in quality control, like with visual inspection systems.
8. Ditch the Inventory Buildup with Make-to-Order Scheduling
Move away from make-to-stock and embrace make-to-order. Use finite capacity scheduling (FCS) software (like Drum-Buffer-Rope or advanced heuristics) to create realistic schedules that consider resource constraints. For smaller shops, a cell team huddle might be enough. This reduces inventory excess and enables just-in-time production.
9. Use “Water Spiders”
Implement “water spiders” – dedicated employees who handle material movement between workstations. This frees up skilled machinists to focus on machining, improving overall efficiency and reducing non-value-added time. This directly addresses transportation waste and allows for better utilization of talents.
Lean Tools to Use
A consultant can help you pick the right tools for your roadmap. But know which ones are out there:
- Six Sigma Problem Solving
- Value Stream Mapping
- Kaizen/Rapid Improvement Events
- 5S
- Kanban/JIT
- Setup Reduction/SMED
- Total Productive Maintenance (TPM)
- Visual Workplace
- Error-Proofing
- Quality at the Source
- Continuous Problem Solving
Lean Tools to Avoid (or Adapt Carefully):
- Top-Down Leadership
- Assembly Line Balancing
- One-Piece Flow Cells
- Takt Time
- Manual Scheduling
Want to Run a Leaner, Meaner Machining Shop in Virginia? This Course Can Help.
We’ve covered some powerful lean strategies, but putting them into action takes real know-how. If you’re serious about transforming your shop and becoming a lean expert, check out the Danville Lean Six Sigma Black Belt Certification Course with GENEDGE.
This program will give you the skills and confidence to lead lean initiatives and make a real difference in your business. You’ll learn how to spot and eliminate waste, streamline your processes, and build a culture where everyone is focused on continuous improvement.
Register for the Danville Lean Six Sigma Black Belt Certification Course by February 28, 2025!