Consumer expectations are at an all-time high, placing heightened pressure on manufacturers to consistently deliver on schedule. Any lapse can result in losing valuable customers, revenue, and credibility. This is why streamlining operations is so important. It doesn’t always mean purchasing costly equipment or high-tech solutions. Rather, the change often needed is in the work processes and the strategies businesses can implement to back this up.
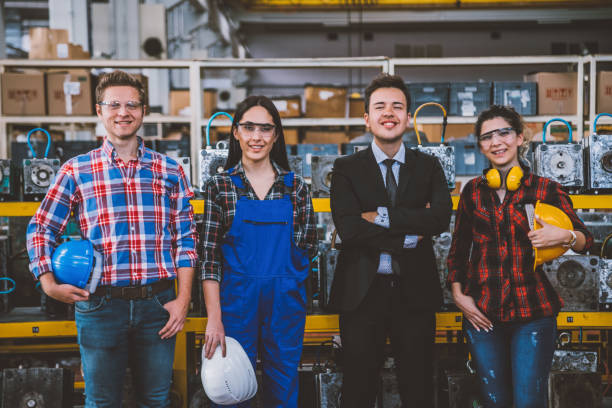
Why Streamline Operations?
Streamlining manufacturing processes is vital for Virginia small manufacturers to boost company profits and maintain competitiveness. Below are some compelling reasons to consider this route:
Increased Customer Satisfaction
Streamlined operations ensure faster order fulfillment, becoming increasingly important in an age of instant gratification. Excellent customer service builds loyalty, a vital component for long-term success.
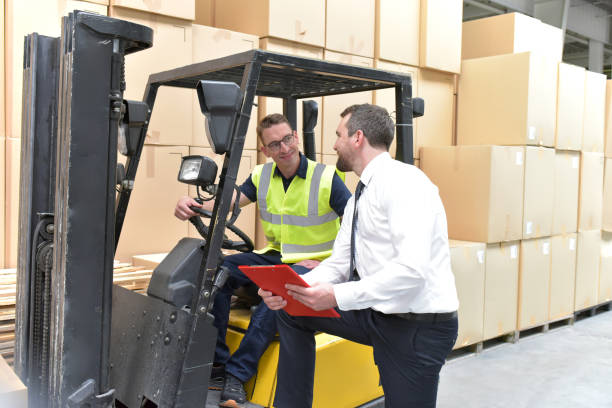
Cost-Effectiveness
Lean manufacturing techniques like continuous improvement and value stream mapping can save money because their core principle is eliminating waste. According to a 2019 research study in Peru, waste can include underused talent, excess inventories, or ineffective processes that do not create customer value. A well-tuned manufacturing process requires less labor and minimizes time spent fixing errors. This efficiency frees up resources for essential tasks like meeting customer needs.
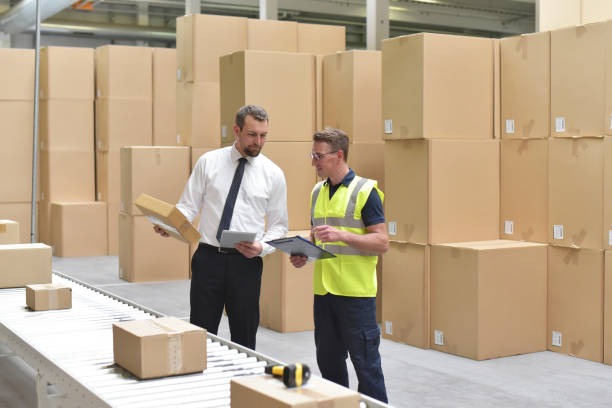
Efficient Workflow
Streamlining operations smooth out bottlenecks that cause delays, resulting in an efficient workflow. It enables manufacturers to produce goods faster without compromising quality.
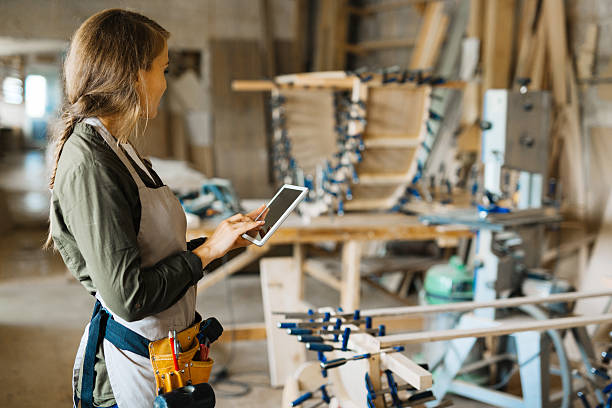
Customized Solutions
Every manufacturer is unique, and the key to streamlining operations is a tailored approach. By conducting a thorough analysis of existing processes, manufacturers can identify specific areas for improvement, implement targeted changes, and measure the impact of these changes on overall productivity and efficiency.
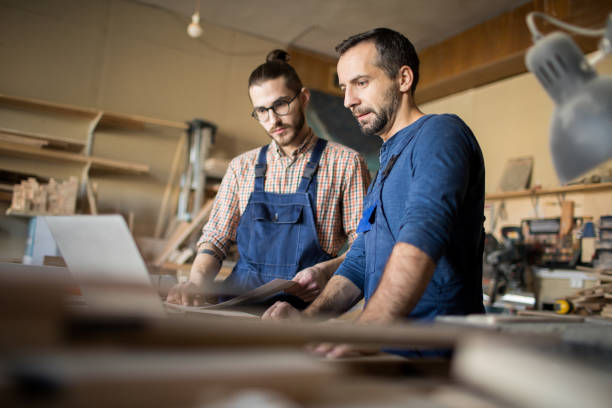
How to Streamline Operations?
Manufacturing process optimization can seem challenging on the outside, but the right strategies can quickly boost efficiency and productivity.
- Request an Assessment
An initial step in optimizing your manufacturing operations is to request an assessment from GENEDGE. This evaluation helps identify areas for improvement and enables us to tailor solutions that best fit your unique processes.
- Identify Bottlenecks
Bottlenecks are stages in your manufacturing operations where processes slow down or even halt. They represent areas of inefficiency and can lead to severe delays and increased costs. Identifying and addressing these issues is crucial to optimizing your production line and improving overall efficiency.
- Attend Lean Manufacturing Classes
GENEDGE offers a variety of training and professional development courses for small manufacturers. The Half-Day Lean 102 Class with Simulation provides an immersive learning experience on lean principles, featuring simulations for a hands-on understanding of lean tools and methodologies.
- Participate in the Emerging Business Program
The Emerging Business Program by GENEDGE offers customized solutions for smaller manufacturers seeking to optimize their operations. It pinpoints specific improvement areas tailored to each business’s unique needs, which can significantly enhance efficiency and profitability.
- Adopt a Lean Manufacturing Methodology
Lean manufacturing focuses on limiting waste and improving operational efficiency. By identifying and eliminating all types of waste in the manufacturing process, such as unnecessary transportation, excess inventory, waiting time, and defective products, you can significantly reduce lead times and improve productivity.
When talking about specific lean strategies, we like to prioritize continuous improvement and value stream mapping. Continuous improvement is an ongoing effort to enhance products, services, or processes, while value stream mapping is a lean-management method for analyzing the current state and designing a future state for the series of events that take a product or service from its beginning through to the customer. Here are some essentials:
- The “Why-Why Analysis” technique: to uncover the root of the problem.
- Ishikawa Diagram (Fishbone diagram): to perform comprehensive problem examination.
- Affinity Diagram: to sort and organize data.
- Failure Modes and Effects Analysis (FMEA): to catch issues in their early stages.
- 5S Dashboard: to promote workspace organization using the five S’s: Seiri (tidiness), Seiton (orderliness), Seiso (cleanliness), Seiketsu (standardization), and Shitsuke (discipline).
- PDCA Cycle (Plan-Do-Check-Act): to ensure continuous improvement.
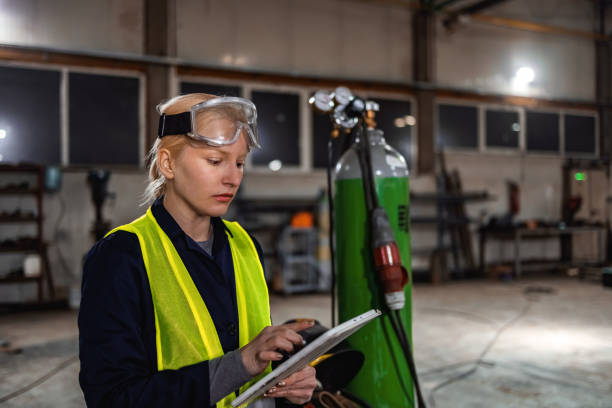
- Embrace Automation
Automation can help reduce the need for manual labor and mitigate human error while ensuring consistency across your manufacturing process. For example, a Virginia-based small manufacturer of electronic goods could implement an automated soldering process. This replaces manual soldering, which is time-consuming and error-prone. It can benefit payment and accounting processes, order processing, marketing efforts, and inventory management.
- Reduce Downtime
Downtime is a significant source of inefficiency in the manufacturing process. Keeping a close eye on your production processes can help quickly identify and address any issues that may cause downtime, such as machine maintenance requirements, equipment failure, or human error.
- Train Employees
Proper training and professional development of your employees is essential to creating manufacturing efficiency solutions, increasing productivity, and streamlining operations. Well-trained employees are better prepared to take on higher responsibilities and can significantly contribute to the success of your business.
- Continuous Improvement & Lean Manufacturing Program
For larger manufacturers, GENEDGE’s Continuous Improvement & Lean Manufacturing services offer comprehensive programs to streamline operations at a larger scale. These strategies help reduce lead times, increase profitability, and improve overall productivity.
Drive Operational Excellence and Improve Shop Floor Processes
We trust this article has underscored the significance of fine-tuning your manufacturing operations and provided useful guidance on accomplishing this. Streamlining operations may seem overwhelming initially (we’ve been there!), but rest assured, the right strategies can revolutionize your manufacturing processes and elevate your business to unprecedented levels.
Ready to take the next step toward maximizing production efficiency? Request a personalized GENEDGE assessment and contact us today. Let’s work together to optimize your processes with lean manufacturing in Virginia.