Industrial robots have come a long way from their early days of automating basic tasks like welding and painting in the automotive industry. Today, in the era of smart machining 4.0, these versatile machines are transforming the world of precision machining, offering a cost-effective alternative to traditional high-end machine tools.
Thanks to improvements in accuracy, repeatability, and offline programming capabilities, robots are now being used for tasks that require far greater precision than ever before. While robots may not yet match the rigidity and micron-level precision of CNC machines, their adaptability, affordability, and growing precision make them a fast-growing popular option for many machining applications.
In this blog, we’ll explain how robots are evolving to find their place in precision machining and where they can be best applied today. Scrolling down isn’t your style?
Read on to learn these three points:
- The 3 biggest benefits of robots in precision machining
- 4 ways robotics helps precision machinery
- 4 real-world applications
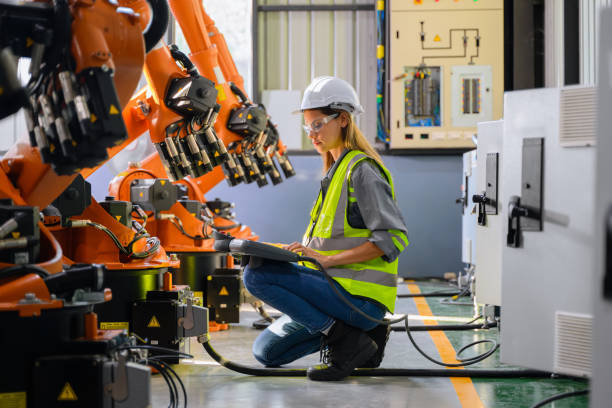
Key Benefits of Robots in Precision Machining
1. Cost Savings
Traditional CNC machines, especially those used for creating prototype models, can be expensive and over perform in terms of the precision they offer. On the other hand, robots can achieve a high level of precision at a fraction of the cost, making them an attractive option for prototype modeling and other less demanding machining tasks.
2. Flexibility and Versatility
Industrial robots excel at flexible operations, like 5-axis machining and wraparound tasks, handling diverse workpieces from prototypes to molds. Their traveling equipment and turntables allow easy reconfiguration for different part sizes and machining needs.
3. Wide Operational Range
Robots can cover a broad operational range, making them ideal for complex tasks like carving intricate designs or machining large parts. With innovations in precision, robots can now handle processes that were once reserved for more expensive equipment.
How Robotics Achieves Precision in Machining
While industrial robots offer many advantages, achieving the required level of precision in machining processes is a challenge that means overcoming several technical hurdles.
GENEDGE’s advanced manufacturing training programs can assist with the following:
1. Improving Absolute Accuracy
One of the challenges with robots in machining is their absolute accuracy. While robots can repeatedly return to the same position (repeatability), their ability to move to a specific location with pinpoint precision (absolute accuracy) was traditionally limited. However, recent advancements in robotics have addressed this by compensating for machine differences, sensor errors, and arm deflection. Now, robots can achieve an accuracy of 0.5mm or less, making them suitable for many precision tasks.
2. Software for Seamless G-code Conversion
Most CNC machines use G-code to control cutting, but new software now converts G-code into robot-friendly programs, allowing users to use the same CAD/CAM data and easily transition to robotic machining.
3. Reducing Micro-Vibrations
Micro-vibrations from torque changes in a robot’s joints can affect machining precision, but new techniques reduce these vibrations for smoother operation and better finishes. Virginia manufacturers can prevent tiny irregularities in the final product by addressing resonance and correcting motor signals.
4. Precision Tool Measurement
In five-axis machining, tool position changes can cause discrepancies. To prevent this, robots use reference tools with spheres to measure and adjust the tool’s position before machining, ensuring precise results despite complex movements.
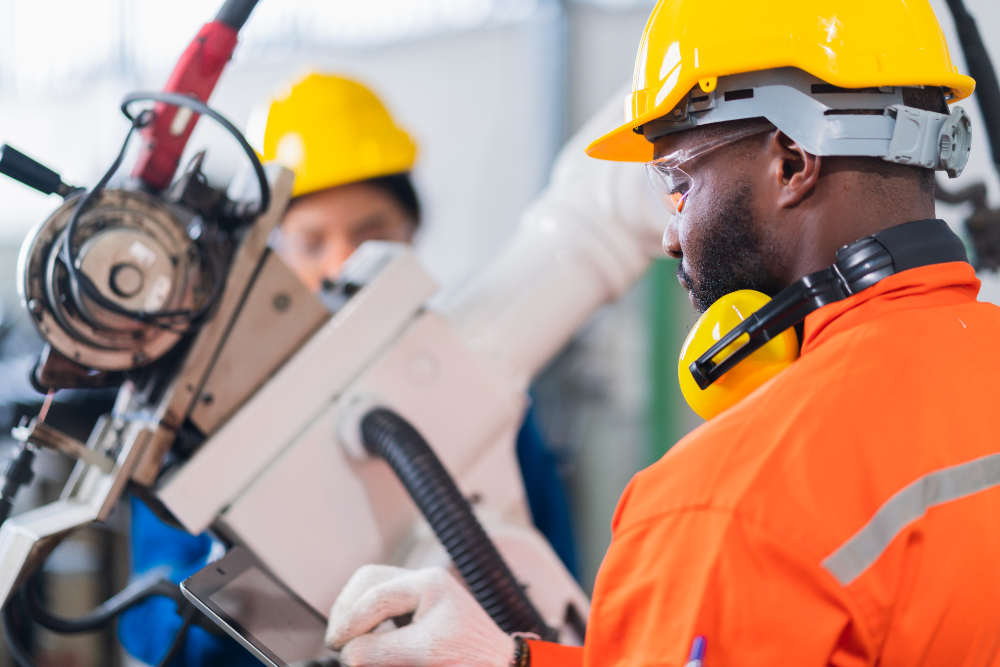
Real-World Applications of Robotics in Machining
1. Automobile Prototype Machining
Robots are now used to create automobile prototypes, like seats and instrument panels, replacing expensive CNC machines that offer more precision than needed. This shift has lowered costs while still providing the required accuracy for prototype production.
For example, robots have been used to machine large-scale prototypes of automobile seats made from materials like Styrofoam or urethane.
2. Laser Welding and Free-Form Surface Machining
Robots are also used in high-precision tasks like impeller laser cutting or welding and free-form surface machining, where precise movement control is crucial. Advanced robotics technology like IIoT enables detailed manipulation, making robots ideal for complex components in aerospace, automotive, and other industries.
3. Nike’s 2010 FIFA World Cup Campaign
An innovative example of robotics in action was seen during Nike Japan’s 2010 FIFA World Cup “Write The Future” campaign. Robots were used to carve messages from supporters into a life-size statue of an athlete. This unique use of robotic precision machining highlighted the capabilities of industrial robots and demonstrated how versatile and adaptable they can be in creative applications.
4. Novus Hi-Tech Robotics in Virginia
This company provides various industrial robot applications that are transforming manufacturing, including precision machining. Their robots are used for tasks such as arc welding, spot welding, materials handling, machine tending, painting, picking, packing, palletizing, and assembly.
The Future of Robotics in Precision Machining
As technology evolves, we can expect robots to take on even more demanding machining tasks, further blurring the lines between traditional CNC machines and robotic systems. Whether for large-scale manufacturing or intricate prototype production, the future of precision machining looks bright with robotics working with us.
Learn More About the Virginia SMART Manufacturing Accelerator!
Want to learn more about how manufacturing intelligence solutions can transform your business?