TL;DR Smart manufacturing uses connected machines, cloud analytics, and AI to raise uptime, cut waste, and boost margins. Adopting these tools now keeps machining operations faster, leaner, and more sustainable; waiting gives the advantage to competitors that already run on data.
Table of Contents
- Smart Manufacturing at a Glance
- Four Benefits You Can Measure
- Where Intelligent Systems Add Daily Value
- The Risk of Standing Still
- A Practical Path to Smarter Machining
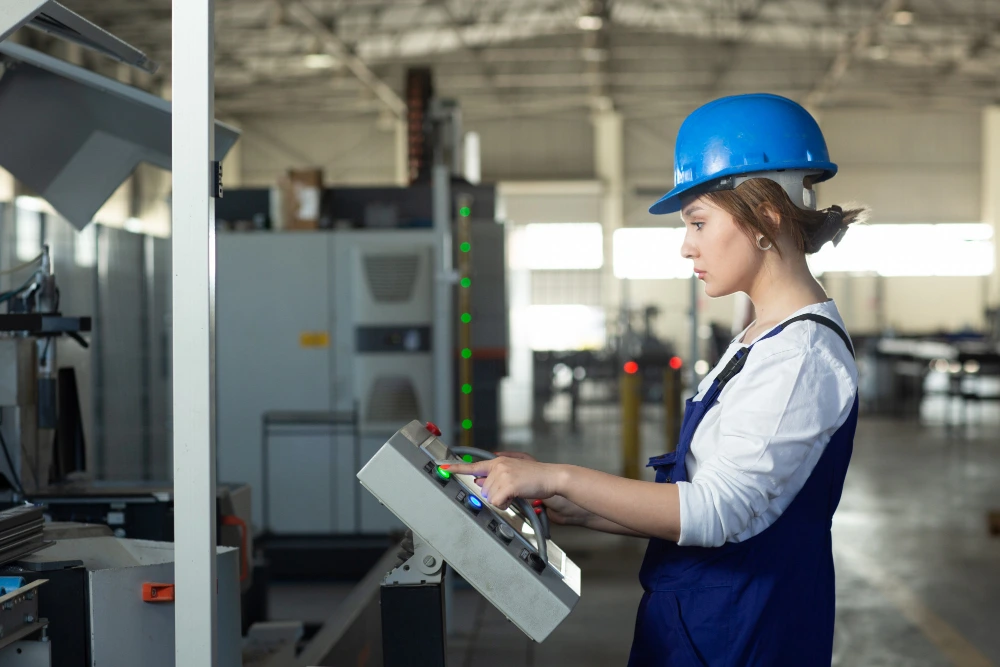
1. Smart Manufacturing at a Glance
The future of machining is defined by visibility. Sensors capture spindle load, vibration, coolant flow, and part dimensions the moment they occur. Those readings feed secure cloud platforms that translate millions of data points into a live dashboard any supervisor can read at a glance.
Early versions of this technology were expensive and limited to large aerospace lines. Prices have since dropped, and modular kits now let even small job shops add connectivity one machine at a time.
Once data starts flowing, operators no longer guess which tool is wearing out or why a cycle slowed; they receive precise alerts supported by real-time data in manufacturing. This clarity is the foundation of every other improvement—from higher throughput to lower scrap—delivered by today’s advanced manufacturing solutions.
2. Four Benefits You Can Measure
Smart investments succeed when they deliver numbers that show up in monthly reports. Connected machining consistently moves four metrics in the right direction:
- Higher efficiency. IoT notifications identify hidden bottlenecks, allowing crews to trim cycle times and raise overall equipment effectiveness.
- Sharper decisions. Live dashboards replace guesswork, so managers reroute jobs and labor before small delays escalate.
- Lower costs. Predictive maintenance schedules service just before a failure, preventing overtime repair bills and rush parts.
- Greener output. Optimized tool paths and balanced material flow reduce scrap and energy, supporting ESG targets that buyers track closely.
3. Where Intelligent Systems Add Daily Value
Smart tools touch every layer of a modern plant and quickly prove their worth.
On the floor. Sensors watch temperature and power draw, while digital twins model fixture changes virtually, saving hours of physical trials.
Inside the cell. Collaborative robots handle loading, gauging, and deburring. Artificial-intelligence software predicts micro-wear on cutting edges—an approach that GE Aviation’s “Brilliant Factory” has used to maintain micron-level accuracy (https://www.ge.com/news/reports/ai-takes-flight-inside-ge-aviations-brilliant-factory).
Across the supply chain. Machine-learning forecasts match inventory to demand swings, limiting both stockouts and overstock. For a deeper dive into resilient planning, see GENEDGE’s growth strategies for manufacturing companies.
For the workforce. Augmented-reality headsets overlay step-by-step instructions on actual equipment. Boeing cut wiring time on its 787 by guiding technicians with AR overlays.
Layered together, these intelligent manufacturing systems shorten lead times and lift quality beyond what manual methods can achieve.
4. The Risk of Standing Still
Market research from Deloitte shows that 74 percent of manufacturers expect smart-factory technology to be essential by 2025. When three out of four peers are actively wiring machines and automating workflows, staying manual leads to clear penalties:
- Slower product launches while connected shops switch tooling overnight
- Higher scrap rates because manual checks miss early drift in accuracy
- Lost bids when customers demand documented, low-carbon parts and you cannot supply verifiable data
Manufacturers who want first-hand stories about overcoming these hurdles can stream GENEDGE’s podcast for manufacturers.
5. A Practical Path to Smarter Machining
Launching smart manufacturing does not require a plant-wide overhaul. A phased plan reduces risk while building internal confidence:
- Instrument a high-value spindle. Install IoT sensors that log load, vibration, and temperature.
- Capture a baseline. Run the machine for two weeks to establish normal operating signatures.
- Pilot predictive analytics. Feed the data into a cloud dashboard and document downtime reductions.
- Expand system functionality. Add scheduling and maintenance modules—hallmarks of advanced manufacturing solutions that scale.
- Upskill the team. Short courses teach operators to respond to alerts instead of waiting for alarms.
- Bring in expertise. GENEDGE tailors technology, funding pathways, and vendor selection to plant size, budget, and growth goals.
Each step locks in measurable savings before moving to the next, ensuring capital is well spent and staff remain engaged.
Ready to Lead the Future of Machining?
Smart manufacturing is already delivering faster cycles, tighter tolerances, and stronger margins for shops that adopt it. Connect with GENEDGE today to pair real-time data in manufacturing with practical, scalable tools and secure your place in the next era of machining.