Workflow issues affect everyone from top to bottom—even veteran metalworkers can’t stop themselves from hitting a wall now and then. Whether it’s handling a recurring problem or a complete workflow overhaul, it doesn’t hurt to test out new technologies and processes in metalworking.
Table of contents:
- Why should metalworkers adopt new tech?
- The top 6 technologies of 2024 metalworkers
- Multi-function tooling solutions
- Spindle connection improvements
- Real-time quality control
- Affordable shrink-fit tool holders
- Advanced tool-locking mechanisms
- Hybrid additive manufacturing systems
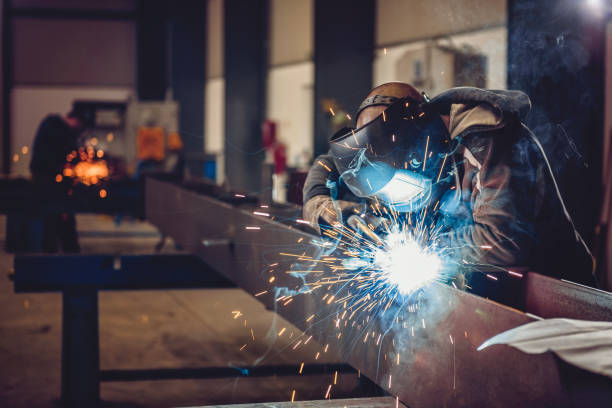
Why should metalworkers adopt new tech?
As of August, the metalworking industry is still stuck in contraction mode, with the Purchasing Managers’ Index (PMI) sitting at 47.2%.
While there was a little silver lining with primary metals showing some growth, fabricated metal products are struggling to perform. This might be the perfect opportunity for metalworkers to understand the impact of Industry 4.0 on the metalworking industry and enact manufacturing quality systems to improve machining output and accuracy.
“While still in contraction territory, U.S. manufacturing activity contracted slower compared to last month. Demand continues to be weak, output declined, and inputs stayed accommodative,” said Timothy Fiore, chair of the ISM’s Manufacturing Business Survey Committee, in this Metal Center News article.
Here are the top 6 technologies that are shaking up the metalworking industry right now:
1. Multi-Function Tooling Solutions
Now, it’s possible to have tools that can perform both roughing and finishing tasks all at once. For example, Sandvik Coromant has introduced a system called PrimeTurning™ that streamlines the process to complete these operations in a single pass. This means faster production times and better quality of finished parts.
2. Spindle Connection Improvements
In fields like aerospace, working with materials like titanium can be difficult due to their hardness and low thermal conductivity (the perfect recipe for tool wear and heat buildup). That’s why having a strong and stable spindle is so important for metalworking technology.
Companies like Kennametal have developed improved spindle designs that prevent bending and wobbling when operating at high speeds. The smoother cuts help tools last longer. Testing has shown that these upgraded spindle connections can improve the surface finish quality and extend the tools’ life through less vibration and more consistent contact with the machined material.
3. Real-Time Quality Control
Software and sensor integration within machining processes is becoming more and more common in metalworking technology. HII Newport News Shipbuilding, coined “all-digital” major shipyard in Virginia, uses tools with advanced metrics that give in-machine quality validation and real-time adjustments.
With the construction of the future USS Enterprise (CVN-80), the shipbuilder is embracing a fully digital design approach by using tablets and laptops for clearer and more interactive work instructions. This change boosts production and enables instant quality checks that allow mechanics to view and adjust digital models directly on their devices.
HII’s President and CEO Christopher Kastner pushed for the digital shift, stating, “Digital shipbuilding and digital instructions work. We need to make sure that they’re employed beyond the aircraft carrier program.”
HII is also partnering with Amazon Web Services to manage its extensive data and promote a quicker, more adaptable manufacturing process. These 3D-printed parts and other additive manufacturing practices mean Newport News Shipbuilding is smashing the bar for quality control in the Virginia industry.
4. Affordable Shrink-Fit Tool Holders
Thanks to cost-effective machines, shrink-fit technology is now more accessible to smaller enterprises. This metalworking technology, with its impressive gripping force, enables stronger tool stability and concentricity in high-speed machining.
These systems are now indispensable in high-torque operations with lowered tool wear and cleaner surface finishes. An example is HAIMER’s Automation Cube One, which can shrink and unshrink tools in just 60 seconds using Siemens Sinumerik One control and manage multiple spindle interfaces at once. It’s a money-saver, tool rigidity booster, and cutting performance enhancer.
5. Advanced Tool Locking Mechanisms
To stop tools from shifting during machining, manufacturers are introducing designs with helical grooves on tool shanks. This locks tools in place within their holders for better accuracy and tool life.
6. Hybrid Additive Manufacturing Systems
The University of Virginia’s School of Engineering heads this research with hybrid systems that merge traditional CNC milling techniques with advanced additive manufacturing. Another example is Hybrid Manufacturing’s AMBIT, which transforms how metal parts are created by allowing milling and additive processes to occur in a single setup. Additive metalworking technology has come a long way.
About GENEDGE
Since 1992, GENEDGE has served the manufacturing supply chain as Virginia’s best public resource to help the industry innovate, compete, and grow. GENEDGE delivers these services on behalf of the Commonwealth of Virginia through high-quality consulting, training, and programmatic solutions. A member of the MEP National Network™ and the lead for Virginia’s DOE-supportedSmart Manufacturing Accelerator (VSMA), we service a market of over 13,844 companies, with nearly 439,848 employees, that produces 14% of Virginia’s GDP.