Since the 80s, the food industry has seen fierce competition only pushed forward by the proliferation of private-label products by specialized third-party manufacturers. Though in the mainstream for decades, more and more manufacturers are going lean to redefine supply chains.
Lean manufacturing preaches the dualism of less waste, more operational efficiency—an approach that promises to raise profits and customer loyalty. Driven by value stream mapping and just-in-time production, this high-level way of thinking addresses workforce turnover, the rising cost of ingredients, and the natural perishability of raw materials.
REQUEST A Half-Day Lean Process Improvement Class FOR YOUR TEAM

In this blog, we cover:
- Lean’s objectives
- This history of lean
- How lean helps food manufacturers
- How they’re doing it
- Tips from GENEDGE to lean out
Lean’s Goal
In a nutshell, lean is not about shrinking staff or slashing resources; instead, it’s about making the best use of what you have. These are the core focuses:
- System Complexity
- Lead Time
- Transport
- Space
- Inventory
- Human Effort
- Packaging
- Energy
Origins of Lean
The roots of lean manufacturing can be traced back centuries, though its principles were more formally articulated by figures like Benjamin Franklin and Frederick Winslow Taylor. Franklin showed the what, how, and why of dropping waste for profit in his “Poor Richard’s Almanack,” while Taylor advocated for systematic improvements in his “Principles of Scientific Management.” He named the five principles: value, the value stream, flow, pull, and perfection.
The evolution of lean practices took place in the automotive industry, driven by Henry Ford, and later, Toyota’s Shigeo Shingo and Taiichi Ohno. Toyota’s Production System, developed post-World War II to address shortages, revolutionized manufacturing with its “just-in-time” model, focusing on demand-driven production and lesser inventory.
Manufacturers who adopt lean food manufacturing solutions see supply chains that lower overprocessing, excess inventory, and unnecessary transport, making them more agile and responsive to the market.
How Can Lean Thinking Help Me?
Lean thinking simplifies production by removing unnecessary steps and concentrating on adding value. This approach benefits small and medium enterprises (SMEs) in the food industry, which make up a big portion of the sector. Through lean supply chain optimization services for manufacturers, these companies can:
- Cut out wasteful actions to give your customers more value and make sure your supply chain runs smoother.
- Resolve bottlenecks and delays to keep products moving smoothly through the supply chain.
- Foster a flexible team to maintain consistent product flow and high quality.
- Speed up how you deliver products and services by cutting out waste.
- Find and fix quality problems while keeping track of everything.
How Are Food Manufacturers Doing Lean?
About 4,000 miles from VA and across the Atlantic, a UK-based company is producing a wonderfully inclusive range of meat-free and dairy-free food products. Referenced in this scholarly Springer conference paper, the company supplies major supermarket chains, offering items such as vegetable burgers, sausages, and cutlets. The typical production process includes steps like raw material preparation, cooking, mixing, shaping, coating with crumbs, frying, and finally freezing and packaging the products.
To integrate lean principles into their operations, the company reviewed its product lines, manufacturing processes, technical facilities, and process flow charts. They identified key areas for improvement and successfully implemented lean tools like waste elimination, 5S methodology, Single-Minute Exchange of Die (SMED), the Andon system, visual management, and work standardization. As a result, they achieved better production efficiency and product quality, and lower production costs by cutting waste and actually adding value.
It seems Virginia manufacturers can learn from our overseas neighbor!
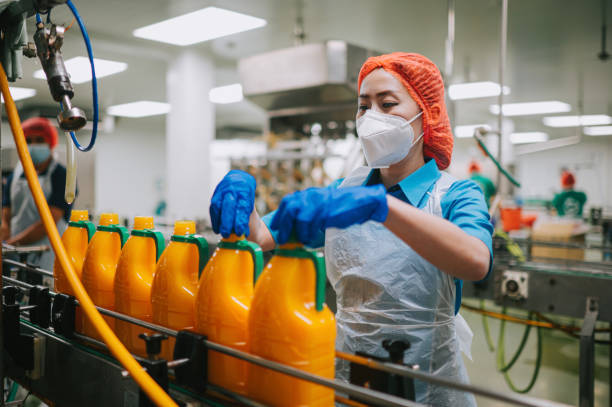
Tips For Virginia Food Manufacturers
To effectively implement lean manufacturing practices, Virginia food manufacturers can benefit from the lean action plan developed by GENEDGE, a Manufacturing Extension Partner (MEP) and food manufacturing consultancy group:
- Planning for Lean: Begin by appointing a dedicated supply chain connector to lead the transformation process. It’s essential to gather comprehensive lean knowledge and identify specific areas that need change.
- Interim Lean Diagnosis: Introduce preliminary steps to test the waters of lean applications. This phase should address potential challenges such as lack of top management support and lean knowledge gaps.
- Lean Operations and Control: Establish a concrete framework for ongoing operations, focusing on five main areas: redefining value, mapping value streams, detecting waste, developing an efficient production state, and maintaining control over lean operations.
Find a more comprehensive roadmap from MEP here.
Turn Your Processes Lean
GENEDGE can offer food manufacturing solutions throughout the supply chain by providing training and resources to “lean out” your employees and processes. Our industry insights can also facilitate a seamless transition by helping to customize lean tools according to a company’s unique needs since waste can happen at any time.
Contact us to learn how to make it happen.