The GENEDGE Alliance Small Business Support Services are made possible by the
NIST Manufacturing Extension Partnership (MEP): https://www.nist.gov/mep.
Click to Read GENEDGE Alliance Member Case Studies
Here’s What We Know:
Manufacturers play a crucial role in contributing to economic growth, and small manufacturers are crucial to that growth
Our mission is to provide the necessary tools and resources your business needs to stay competitive, innovate and grow in Virginia.
Which is why the value you’ll receive from a GENEDGE Alliance Membership is unmatched.
Explore Each Of The Benefits Below:

GENEDGE Alliance Emerging Business Program
Learn More About The Emerging Business Program
Digital Resources & Tools From Leading Industry Experts
Digital Resources
Ask The Expert Exchange Page, Get Your Questions Answered in Real Time!
Ask The Expert A Question
Online & In-Person Training Opportunities for Professional Development
Professional Training & DevelopmentGENEDGE Alliance Support Services Are Built To Grow with Your Business:
Access to Supply Chain Support Services
GENEDGE offers unparalleled Supply Chain Support services, specifically tailored for Virginia’s manufacturers, transforming your supply chain into a seamless, efficient, and resilient operation. Thanks to exclusive funding provided to state Manufacturing Extension Partnership (MEP) Centers like GENEDGE, we are at the forefront of empowering manufacturers with the tools, insights, and strategies needed to excel.
Learn More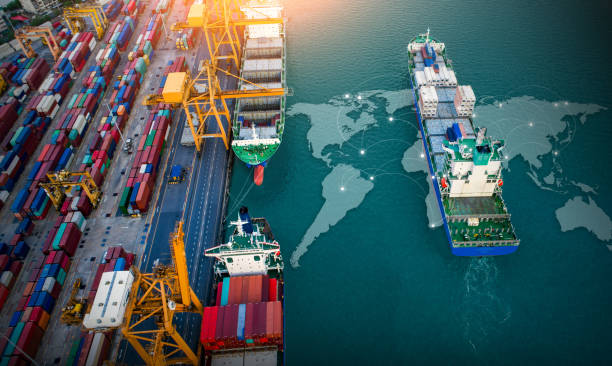
Introducing, Ask The Expert!
If you are looking for answers to your questions quickly from reputable sources then you are in the right place! Here you have access to the answers to common questions, or ask your own questions of our dedicated subject matter experts.
Get Your Questions Answered
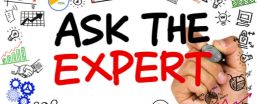
Emerging Business Program
The goal of this program is to offer subsidized consulting to small manufacturing companies with high growth potential. This platform will help companies identify their gaps and determine what solutions make the most sense for their business to drive growth.
Learn More or Apply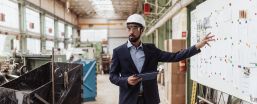
Manufacturing Now in Virginia Podcast
This podcast, produced by our very own Jeanette Stevens Cunningham, focuses on the issues that matter to Virginia’s manufacturers. As a member you will get the most current episodes as they are released. Become a member of the GENEDGE Alliance and hear from subject matter experts, other manufacturers and our staff as we discuss the issues that matter to you.
Listen Now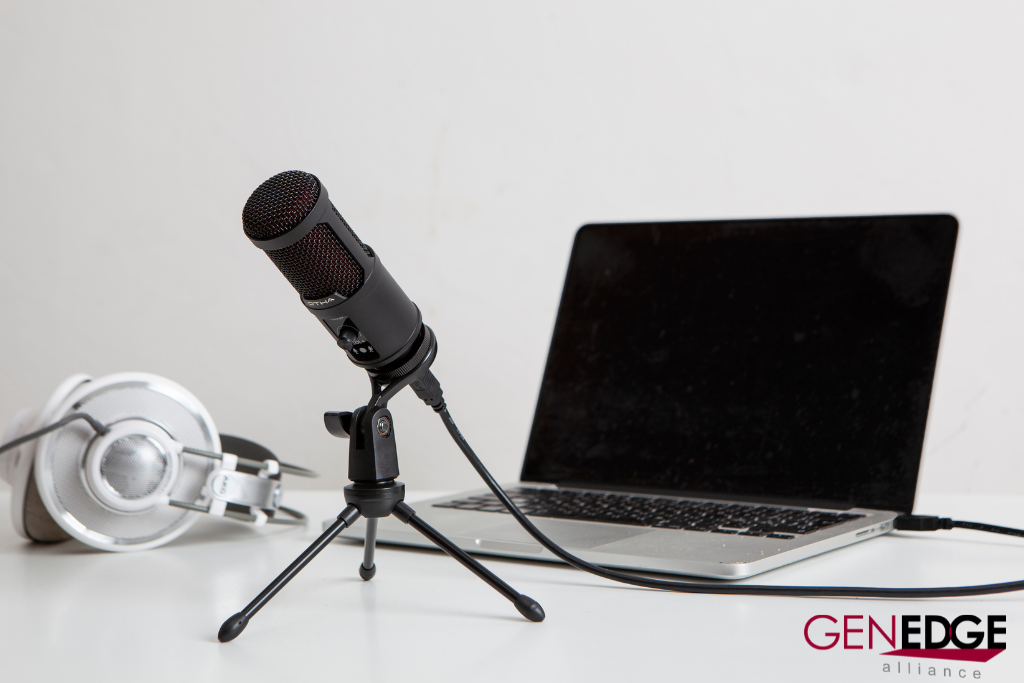
Small Business Resources and Content
GENEDGE is a treasure trove of resources, especially for family owned manufacturing businesses and small manufacturers. We have gathered an array of tools and resources designed to answer your questions, helping you navigate the challenges of running a manufacturing business.
Learn More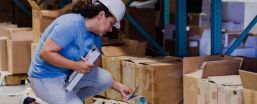
Discounted Online Education and Training
GENEDGE provides high-quality educational content accessible on your schedule. The GENEDGE Learning Management System offers standard on-demand courses or we can customize training packages to meet your needs.
As a GENEDGE Alliance Member, you will qualify for discounts to online training.
See Available Courses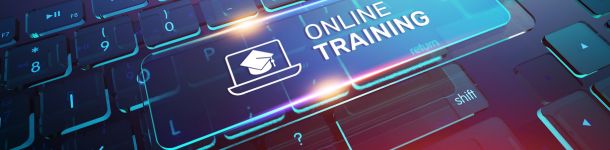
GENEDGE Alliance members need to meet certain requirements, right?
Yes, there are three basic requirements for GENEDGE Alliance membership (full Terms and Conditions here):
- Members must be acting on behalf of or as an employee of a manufacturing supply chain company located in Virginia. Membership will be limited to members of these companies.
- Members agree to provide valid and current company and contact information as required to validate their client status, provide offered services, and generate the member account.
- The member acknowledges that the GENEDGE Alliance is a publicly supported program and agrees to cooperate in surveys and other evaluation methods required by our sponsors for reporting to evaluate the program’s effectiveness.
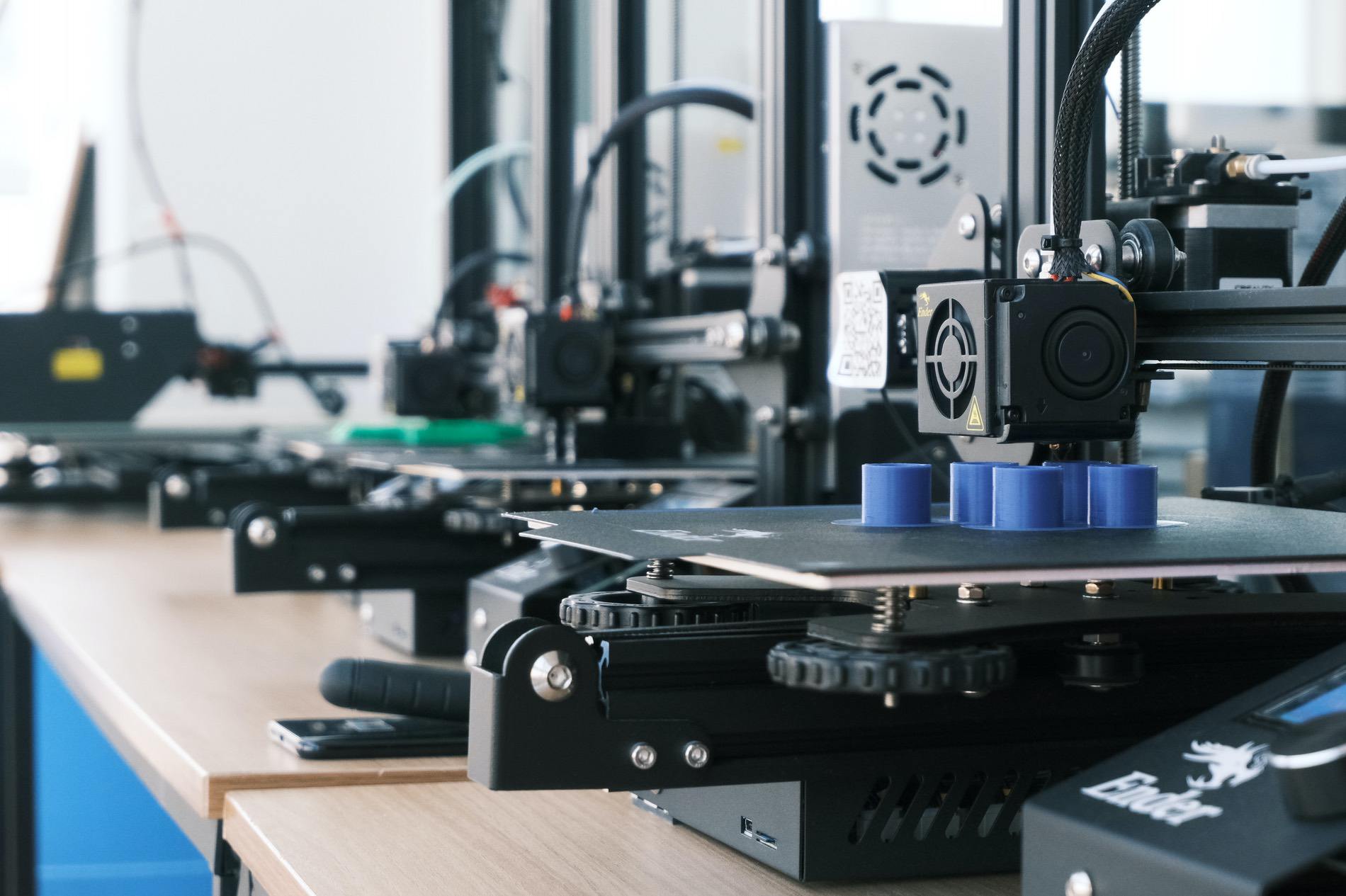
Create Your Free GENEDGE Alliance Member Account Today
Get helpful resources, content, and tools to help you find what you are looking for!
Questions? Connect with Us
Please connect with your Small Business Manager to learn more.