The metal manufacturing world is moving fast, and Virginia is right in the thick of it. Factories are smarter, machines can communicate with each other, and a whole new digital world is here just to make things better and faster.
According to a fresh report from Deloitte in July 2023, the money being pumped into small metal parts manufacturing construction is huge – like $201 billion. That’s a whopping 70% jump from last year, setting us up for some exciting times ahead in 2024.
READ THE BLOG: REINVENT MANUFACTURING OPERATIONS WITH DIGITAL MARKETING STRATEGIES
Why is all this happening? Well, for starters, everyone’s looking for materials that are light, strong, and last a long time, like aluminum or titanium. Think about how useful this is, especially in the aerospace and automotive industries, where these materials aid energy sustainability. Manufacturers will likely look to invest more in electrification and decarbonization overall.
But here’s the big question: what will keep Virginia’s metal makers on top of their game this year, as we have seen with Virginia MetalFab’s most recent expansion and job creation of over 130 jobs? What technologies will change the way we forge things, from the smallest screws to the largest beams?
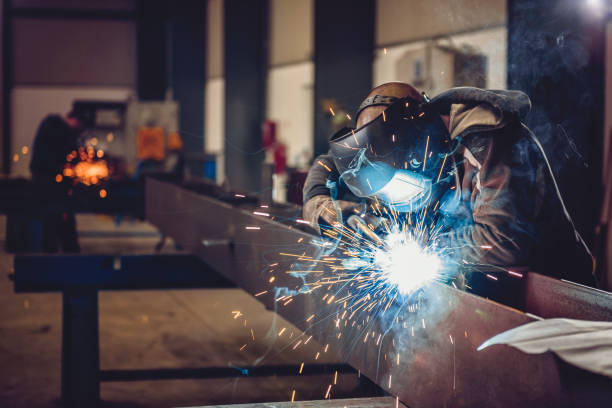
In this blog, we break down:
- 2024’s metal manufacturing trends and technologies:
- AI and ML
- Robots and Cobots
- Digital Twins
- Interconnected manufacturing
Artificial Intelligence (AI) and Machine Learning (ML)
AI and ML are critical for creating precise components and making informed decisions by analyzing large datasets. Deloitte’s latest analysis indicates that 86% of manufacturing executives see smart factories, which incorporate AI, 5G, IoT, and cloud computing, as key to staying competitive in the next five years. These technologies improve machine interconnectivity and automation, with benefits like predictive maintenance to prevent downtime and IoT sensors for real-time monitoring, enhancing productivity and decision-making processes.
Robots and Cobots
Using robots and “cobots” (that’s short for collaborative robots) is a big game-changer in metalworking. Robots are precise; they surpass human capabilities when it comes to tasks that need a lot of attention, like welding or cutting very specific patterns. This means things get done faster and without mistakes.
But it’s not just about doing tasks on their own. These robots work alongside the machines we’ve been using for years, helping everything run smoother and last longer without breaking down. Plus, with robots that can move around the factory floor independently, carrying stuff from one place to another, everything stays neat and tidy, making the workplace safer.
And then there are the cobots. These are designed to work right next to people, doing the heavy lifting or assembly, packaging, and welding so workers can focus on the more intricate parts of the job. It’s teamwork but with robots!
Also, using innovative tech like machine learning to keep an eye on equipment means we can fix things before they even break. This keeps the production line moving without any surprise stops. With all these robots and smart systems, metalworking is stepping into a future where things are done better, faster, and safer.
Digital Twins
Digital twins are no longer just cool tech from sci-fi. They’re a game-changer in small metal parts manufacturing, giving us a digital clone of anything from a single part to a whole process. Imagine being able to test, tweak, and perfect your production in a virtual world before touching anything real.
By 2024, expect digital twins to get even better, thanks to tech like 3D modeling and cloud computing. They’re building the foundations for industrial metaverses, where everything from your factory floor to an entire city can be replicated digitally. This is huge for teamwork and innovation, letting people from all over the globe work together in these virtual spaces. Forbes and a 2023 Deloitte and MLC industrial metaverse study show that almost every manufacturer is getting on board with big hopes for boosting sales, quality, and productivity.
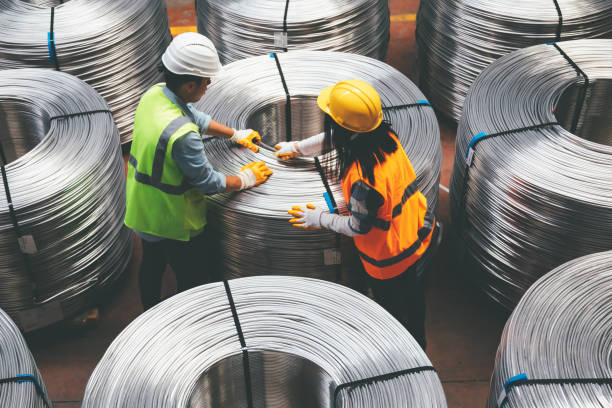
The Push for Smarter, More Connected Manufacturing
The future of metal manufacturing in Virginia is heading towards more digitized and automated processes, especially with innovations like digital CNC machining. Thanks to IoT sensors and advanced data analytics, this technology makes machines more connected and responsive. This automation reduces the need for manual effort and maximizes efficiency.
A significant trend is the exploration of generative AI, like ChatGPT, to create CNC machine code. The Forrester’s July 2023 AI Pulse Survey highlighted that although 67% of businesses are integrating generative AI, 29% are still testing its waters, indicating a careful yet hopeful adoption.
On the forefront of automation is the CubeBOX system, a revolutionary compact robot cell that manages up to three CNC machines non-stop, slashing downtime and pushing productivity to the max. This leap towards interconnected and automated manufacturing is not just about keeping up with technology—it’s about leading in global competitiveness and innovation.
For example, Virginia MetalFab’s evolution into an advanced, fully integrated production company highlights the significant impact of adopting advanced technologies and forming strategic partnerships, like their collaboration with GENEDGE. This transformation, fueled by manufacturing intelligent solutions and an effective use of integrated ERP systems, dramatically improved their operational efficiency and market presence.
Request a free assessment from GENEDGE for more information on manufacturing operations support in Virginia.