TL;DR: A well-optimized manufacturing plant layout isn’t just about fitting machines into a space—it’s about creating efficient flow, reducing waste, improving safety, and supporting growth. From aligning your layout to your value stream to planning for long-term flexibility, each design choice has the potential to impact productivity and profitability. Let’s break down the core principles that make a manufacturing layout truly work.
Want to jump straight to the visuals on how to design your layout? Download the infographic.
In a world of automation, advanced robotics, and real-time production data, you might think plant layout is yesterday’s concern. But the truth? How your manufacturing floor is laid out has a huge impact on how efficiently your business runs.
Whether you’re planning a new facility or updating an existing one, your layout affects everything from output and safety to employee satisfaction and long-term scalability.
“A good layout doesn’t just support your operations—it accelerates them.” – Jeanette Stevens-Cunningham, Director of Marketing & Content Service Delivery at GENEDGE
With that in mind, let’s walk through the key principles of effective manufacturing plant design that every team should consider.
Table of Contents
- Align with Your Value Stream
- Streamline Material Flow
- Make the Best Use of Space
- Prioritize Safety and Ergonomics
- Design for Scalability and Flexibility
- Support Visibility and Communication
- Optimize Based on Data
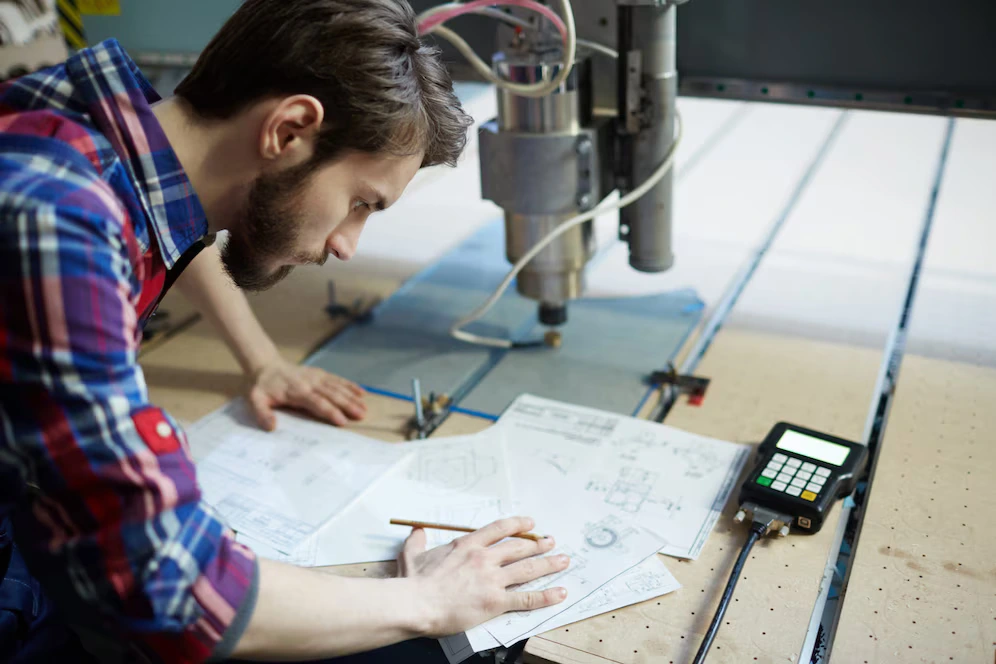
1. Align with Your Value Stream
Before you move any machines or draw up floor plans, get clear on your value stream. This is your product’s journey from raw materials to finished goods.
Mapping your value stream helps you:
- Identify bottlenecks
- Reduce non-value-adding steps
- Understand the physical flow of materials
Once you see how value moves through your business, you can align your manufacturing plant layout accordingly.
Pro Tip: Use value stream mapping (VSM) to visualize how materials, people, and information move through your process.
2. Streamline Material Flow
Your goal: get materials from point A to B with as few touches as possible. Every unnecessary movement adds cost, time, and risk.
Smart material flow design includes:
- Straight-line movement (avoid backtracking!)
- Proximity between related workstations
- Clear aisle spacing for forklifts and staff
- Minimal manual transport
Like designing a highway, fewer intersections, smoother traffic. Good flow is quiet flow. The fewer disruptions you hear, the better your layout is working.
3. Make the Best Use of Space
Square footage is expensive, and clutter is costly. A great layout maximizes every inch.
Look for ways to:
- Use vertical storage solutions
- Implement modular workstations
- Design flexible zones for fast changeovers
- Avoid “dead zones” with no productive value
Tip: Just because a space is open doesn’t mean it’s optimized. Use lean layout simulation tools to test your designs virtually. Toyota does exactly that to achieve its one-piece flow.
4. Prioritize Safety and Ergonomics
An optimized layout should protect your people, not work against them. Your team should be able to move safely, reach what they need easily, and avoid hazardous intersections.
Smart layout safety includes:
- Clear walkways with proper signage
- Ergonomic placement of tools and controls
- Noise control zones
- Separation of pedestrian and forklift traffic
5. Design for Scalability and Flexibility
Your plant needs to work for today’s production—but also for tomorrow’s growth.
That means:
- Leaving space for new machines or assembly lines
- Using mobile or modular equipment when possible
- Designing utility access (air, power, water) with change in mind
Layout flexibility = business resilience.
Partnering with manufacturing business growth consulting experts can help future-proof your design.
6. Support Visibility and Communication
Open sightlines and strategic workstation placement help operators, supervisors, and support staff stay aligned. Communication improves. Mistakes get caught faster. Accountability rises.
Try to:
- Place team leads and supervisors in visible central locations
- Use digital dashboards or status lights visible from across the floor
- Create small shared zones for daily standups and meetings
The layout itself should encourage collaboration.
7. Optimize Based on Data
Modern layouts aren’t set-and-forget. They evolve. Use data to continuously improve:
- Track material movement and lead times
- Monitor energy use by zone
- Use IoT devices and sensors to study equipment performance
- Run simulations before making big changes
Layout design is a living process. Data tells you where to pivot.
Looking for data-driven tools to optimize plant layouts? Check out resources from Lean Enterprise Institute and Manufacturing.net for real-world examples and best practices. GENEDGE Alliance members tap into everything they need in one place.
Don’t Design Alone.
Whether you’re starting from scratch or adjusting your current setup, your plant layout deserves serious attention. These core principles will get you started, but optimizing your design takes experience.
GENEDGE offers tailored support in manufacturing plant layout and operational growth. Our team works directly with small to midsize Virginia manufacturers to help them streamline operations, plan for growth, and implement efficient layouts that scale.