If you are a plant manager, you know how important it is to have an effective plant layout. It can make or break your manufacturing operations, affecting efficiency, productivity, quality, safety, and customer satisfaction.
Got a manufacturing company with less than 20 employees? Transform operations with the GENEDGE Emerging Business Program!
But what makes a good plant layout? And how can you design or improve your existing layout to meet your current and future needs?
In this blog post, we at GENEDGE will share tips and best practices for using lean principles to create a lean plant layout.
In this blog, we’ll cover:
- What a lean plant layout is
- How to design a lean plant layout
- How industry leaders are applying lean principles to production
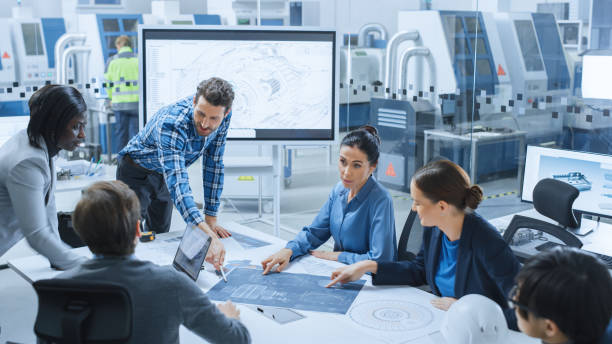
What is a Lean Plant Layout?
A lean plant layout streamlines your smart factory workflow, cuts waste, and enhances value, leading to reduced costs and improved quality. It’s all about arranging your processes with the end-to-end flow in mind—turning raw materials into customer-ready products efficiently. Unlike conventional setups, lean layouts align tasks side-by-side, slashing unnecessary movement and handling of materials. This minimizes delays and inventory build-up, keeps the work area clear, and makes troubleshooting straightforward.
To the manufacturer’s benefit, lean layouts favor versatile, appropriately sized equipment tailored to specific product lines, boosting adaptability and reducing downtime. Visual cues play a big role, too, making operations transparent with indicators like kanban cards and color-coded areas, aiding in real-time communication and organization.
How to Design a Lean Plant Layout
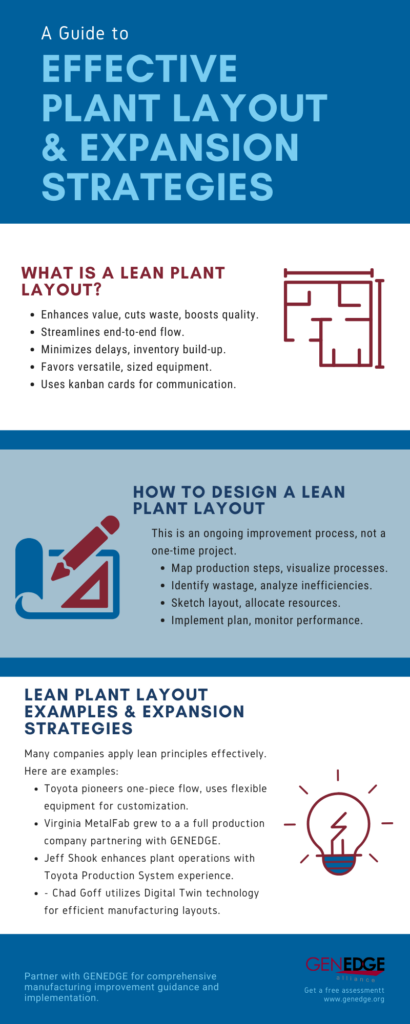
Designing a lean plant layout is not a one-time project but a continuous improvement process. But the steps can be pretty simple:
Map Your Value Streams
Identify what you produce and the steps involved from start to finish. Use value stream maps to visualize your process, noting times, inventory, and the flow of information.
Identify and Analyze Wastage
Look for inefficiencies—long walks, excess stock, quality issues, bottlenecks, or unnecessary production. Tools like spaghetti diagrams and 5S can help identify what’s not working and why.
Plan Your Future State
With your analysis in hand, sketch out a new, waste-reducing layout. Use diagrams and software to bring your vision to life, and plan the resources and time you’ll need to make the changes.
Implement and Monitor
Put your plan into action and rejig your space. Keep an eye on key performance indicators to see how things are improving. Regular checks and team feedback will help you refine your layout even further.
Examples of Lean Plant Layout and Expansion Strategies
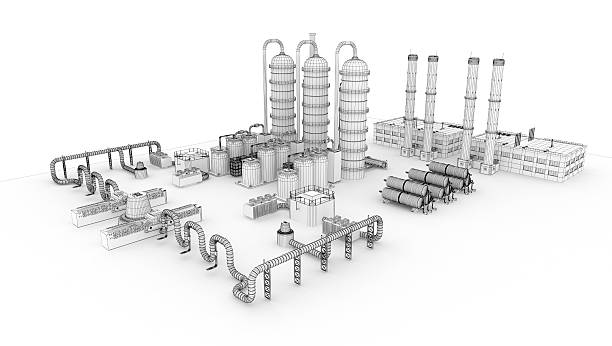
Many companies have successfully applied lean principles to their plant layout and expansion strategies. Here are some prime examples:
- Toyota, the pioneer of lean manufacturing, has designed its plants to achieve a one-piece flow, where each product moves smoothly from one process to the next without any interruption or waste. Toyota also uses flexible equipment that can produce different models for better customization. Neat!
- Virginia MetalFab, a leading metal manufacturer in Virginia, partnered with GENEDGE to evolve from a small “job shop” into a full production company. With GENEDGE’s assistance, Virginia MetalFab expanded its manufacturing and fabrication services, achieving a leap in market share for the transportation industry and enhancing its physical footprint. This expansion was facilitated by a comprehensive commercialization plan and a lean facility layout, resulting in significant sales, job creation, and cost savings.
- Jeff Shook at GENEDGE, an Engagement Manager, stands out for his skill in improving how plants are arranged and operated. Thanks to his international experience and hands-on work with the renowned Toyota Production System, Jeff has played a key role in bringing manufacturing back to local shores and driving efficiency in a range of sectors. He’s known for significantly upgrading Pioneer Electronic Corporation’s assembly lines to handle thousands of products every day and for improving the manufacturing of heating, ventilation, and air conditioning (HVAC) units at Daikin Applied Americas, which greatly boosted their output and quality.
- Chad H. Goff at GENEDGE, an engagement consultant with over 29 years of experience in product management, spearheads 2D & 3D design and oversees large-scale projects. Chad excels in utilizing Digital Twin technology and software like FlexSim to refine manufacturing processes and create digital plant layouts.
Redefine Your Factory Plant with GENEDGE
Remember, perfection may be a moving target, but with lean, you’re always driving forward—the quest for improvement is unending. Ready to start this transformative journey? Partner with GENEDGE. Our expertise will guide you through every step, from initial assessment to final implementation, ensuring continuous improvement becomes the hallmark of your manufacturing operations. Get a free assessment with GENEDGE today.