We all know that the electronic design and manufacturing sector isn’t immune to the occasional hiccup—unplanned supply chain challenges can throw a wrench in product launches, shake up market positions, cause material shortages and components, and hit the bottom line hard.
You need a smooth handoff from design to production to keep manufacturing and PCB production running. This means anticipating potential issues and encouraging teamwork among everyone involved—whether it’s the design teams, suppliers, or partners—right from the start.
In this blog, learn how to:
- Streamline processes
- Build resilience
- Speed up time-to-market
- Anticipate future challenges
- Prioritize manufacturing
- Stay ahead
- Secure supply chain
- Plan ahead
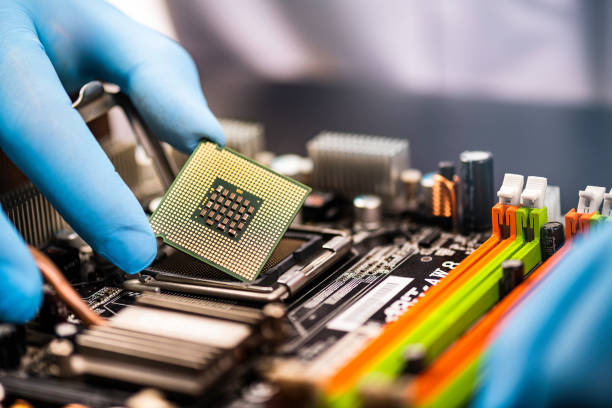
These internal business objectives should shape inventory targets at every stage of the production process:
- Aligning inventory levels with business objectives
- Bill of Materials (BOM) management
- Raw PCBs
- Mechanical housings
- Cabling harness supply
- Use of assembly materials
- Contract Manufacturer (CM) collaborations for staging
- A logistics plan involving all stakeholders
- Partners’ capabilities for shipping and scheduling
- Direct shipment options from CMs to customers
Quick Tips To Optimize the Electronics Supply Chain
Streamline the Design-to-Launch Process
One essential strategy for minimizing the impact of supply chain disruptions in electronic design and manufacturing is to streamline the design-to-launch process. Early engagement with suppliers and partners is key to identifying potential roadblocks and addressing them proactively.
By integrating suppliers early into the product development process, Virginia companies can ensure they are aligned with procurement objectives and prepared to manage changes efficiently. GENEDGE demonstrated this in its collaboration with ERNI Electronics, Inc., by implementing lean manufacturing practices to improve organizational efficiency in its Richmond facility.
Address Preventable Challenges
Supply chain issues such as delivery delays and component replacements are more than prevalent. Delivery delays, often due to fragmented systems, can derail new product launches.
To combat this, creating a culture of collaboration and leveraging advanced technologies like cloud computing can build resilience, often stimulated by supply chain optimization consultants. Additionally, using real-time and predictive data can improve visibility across the product lifecycle, enabling safer sourcing decisions and reducing the chance of expensive disruptions.
Achieve Faster Time-to-Market
A comprehensive approach combining rapid design processes, goal alignment, and electronics configuration can dramatically lower time-to-market. Make sure to manage the bill of materials (BOM) and early supplier collaboration to forge a pathway to market success.
Anticipate Future Uncertainty
Plan ahead to handle unexpected supply chain disruptions by using advanced business tools to forecast potential challenges. Establish clear guidelines for managing high-performance systems that might be subject to export restrictions. Ensure everyone on your team is aware of what products meet these criteria, based on their technical specifications and final delivery destinations.
Prioritize Manufacturing Capacity
Limited manufacturing capacity can become a bottleneck in periods of high demand. Collaborate with your Contract Manufacturer (CM) to set clear product priorities and prevent unauthorized interpretations of production schedules. Your products should always maintain their places in the production line.
Beat Part Obsolescence
To achieve supply chain optimization for your manufacturing company, create a review plan to stay ahead of component obsolescence. Work with your CM to develop strategies for last-time buys and seamlessly transition to alternative components in your Bill of Materials (BOM). Set up automated alerts to catch obsolescence announcements, and designate a decision-maker in your design team to make fast updates.
Secure Authorized Distribution Channels
Protect your supply chain by maintaining clear authorized distribution methods. Prevent gray market infiltration so that all parts come from reputable distributors, a critical step to uphold the integrity of your products. Collaborate with a CM that prioritizes sourcing through trusted channels.
Plan for Product End-of-Life
Incorporate end-of-life planning into the product development phase rather than waiting until production winds down. Strategize for the disposition of leftover inventory, decide on potential repurposing opportunities and manage last-time buys efficiently. Align your logistics strategy with the financial objectives of your enterprise for seamless transitions.
Electronic design and manufacturing professionals in Virginia can find more GENEDGE supply chain resources here.
Want to get straight to the point? Schedule a one-on-one with your dedicated supply chain manager, Elisabeth “Maz” Mazza!