Do you ever feel like food manufacturing is more of a balancing act than a production process?
Between rising supply costs, labor shortages, and meeting strict safety standards, it can seem like there’s a new challenge around every corner. But success comes from implementing smart, targeted solutions, from automating quality control processes and optimizing supply chains to enhancing sustainability efforts.
In this blog, we’ll explore the common challenges with lean manufacturing in the food industry and examine our innovative approaches to overcome them.
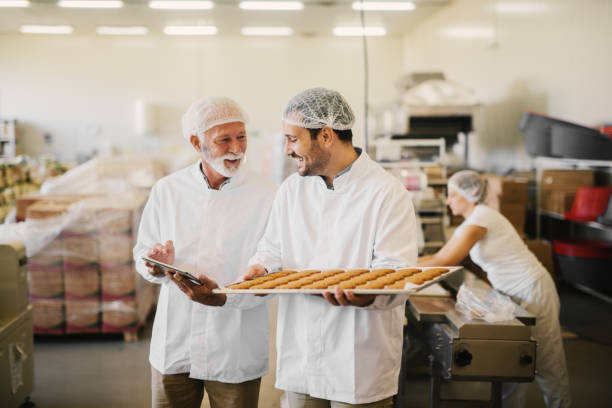
Table of Contents
- Compliance
- Workforce
- Quality
- Expenses
- Supply Chain
- Sustainability
Compliance
Food and beverage regulations are designed to ensure consumer safety, but navigating these complex requirements can be challenging. Proactive safety measures are crucial in lean manufacturing in the food industry, and non-compliance can create costly legal penalties and recalls.
A lean manufacturing consultant can assist your business in becoming or staying compliant through a Food Safety Management System (FSMS). This framework helps identify potential hazards and establishes control measures to prevent future issues using the Hazard Analysis and Critical Control Points (HACCP) system. Automation streamlines this process, facilitating regular staff food manufacturing training, maintaining digital records, and providing audit-ready documentation. These vital elements of a well-functioning FSMS ensure that food safety protocols are consistently followed across all stages of production.
Workforce
Labor shortages continue to be a barrier both in the industry and nationally, with the U.S. Chamber of Commerce’s latest data showing 8.2 million job openings and 7.2 million unemployed workers. To improve productivity while addressing labor gaps, manufacturers must invest in technology and people.
While automation can maintain efficiency with fewer workers, it’s crucial to prioritize attracting and retaining skilled employees. Competitive wages, career advancement opportunities, and training programs can improve workforce stability and productivity.
Emphasizing the importance of workforce development, GENEDGE helps manufacturers implement food manufacturing training programs and career development pathways to attract and retain skilled workers. In-person and online manufacturing training opportunities are available to discuss with one of our consultants.
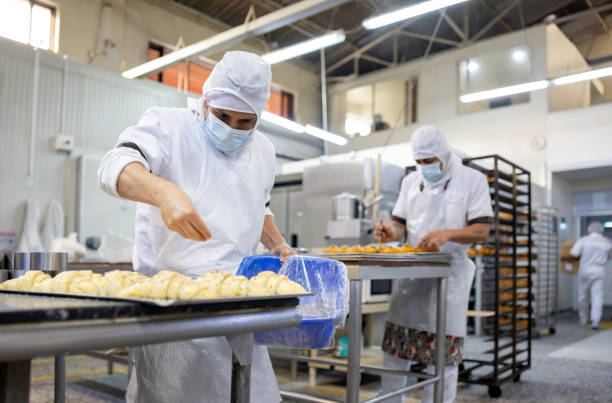
Quality
Scaling production without compromising quality is no piece of cake, but emerging technologies are revolutionizing quality control in food manufacturing.
Through Lean Six Sigma methodologies, we support manufacturers by implementing food manufacturing training and precise automated machinery to improve and standardize processes, minimizing human error and maintaining product integrity.
By incorporating these practices, manufacturers can ensure consistent quality, even as production increases, improving customer satisfaction and lowering financial loss. Get food manufacturing consulting to explore how these strategies protect profit margins without compromising product quality.
Expenses
Increasing material and energy prices and rising transportation costs can impact profitability. To counter looming operational costs, manufacturers now focus on efficiency through lean manufacturing techniques to minimize waste, streamline processes, and lower operational costs.
Take a bite out of inefficiency and lower costs by working with local suppliers in Virginia. Through manufacturing business consulting, we’d love to share strategies focused on driving efficiency and cost savings, giving manufacturers more control over fluctuating expenses.
Supply Chain
In today’s global economy, ensuring manufacturers have a strong supply chain is our bread and butter. Our team of experts emphasizes fostering relationships with multiple suppliers. And using data to forecast demand, enabling companies to remain agile and reduce the impact of potential disruptions. Your GENEDGE lean manufacturing consultant will advise on risk management strategies that optimize inventory while maintaining production timelines, helping manufacturers stay competitive even during global supply chain disruptions.
We facilitate our work with supply chains through an online capabilities database and connection platform known as Supply Chain Support Services. Created for Virginia manufacturers seeking supply chain solutions, the platform helps manufacturers adapt to changing market demands, quickly find new qualified suppliers, discover new contract opportunities, and connect to manufacturing resources in Virginia.
Sustainability
Consumers today are more and more aware of their environmental footprint. To adapt to this trend, manufacturers in the lean food industry are implementing sustainable practices that lower waste and resource consumption. Energy management, environmental health and safety processes, and circular economy practices like recycling are gaining traction for manufacturers dealing with perishable inventory.
Time to Lean In
In food manufacturing, adaptability and lean principles are key ingredients for success. Addressing challenges in compliance, workforce management, quality control, expenses, supply chain optimization, and sustainability helps manufacturers stay competitive while delivering high-quality products.
GENEDGE specializes in providing essential resources to help food manufacturers handle everyday challenges and achieve success. Through food manufacturing consulting, our team of experts will provide custom solutions, whether through automation, workforce professional development, or streamlining supply chains retrofitted to your organization.
Contact one of our lean manufacturing consultants today to learn more.