The small-scale food manufacturing industry is struggling to retain its workers. According to the U.S. Bureau of Labor Statistics, around 750,000 manufacturing jobs remain unfilled despite low unemployment rates. The Manufacturing Institute and Deloitte predict that by 2030, 2.1 million manufacturing jobs will go unfilled due to a lack of skilled labor. In the meat sector, labor-driven disruptions have even caused temporary plant closures.
Many workers are getting older, and changing consumer needs and complicated supply chains make it even tougher. Old ways of hiring aren’t working, but automation could be the solution. With robots and AI, manufacturers can fill the skills gap and make production safer and more efficient. This shift creates a partnership between human skills and machine precision to open up new opportunities for innovation and teamwork.
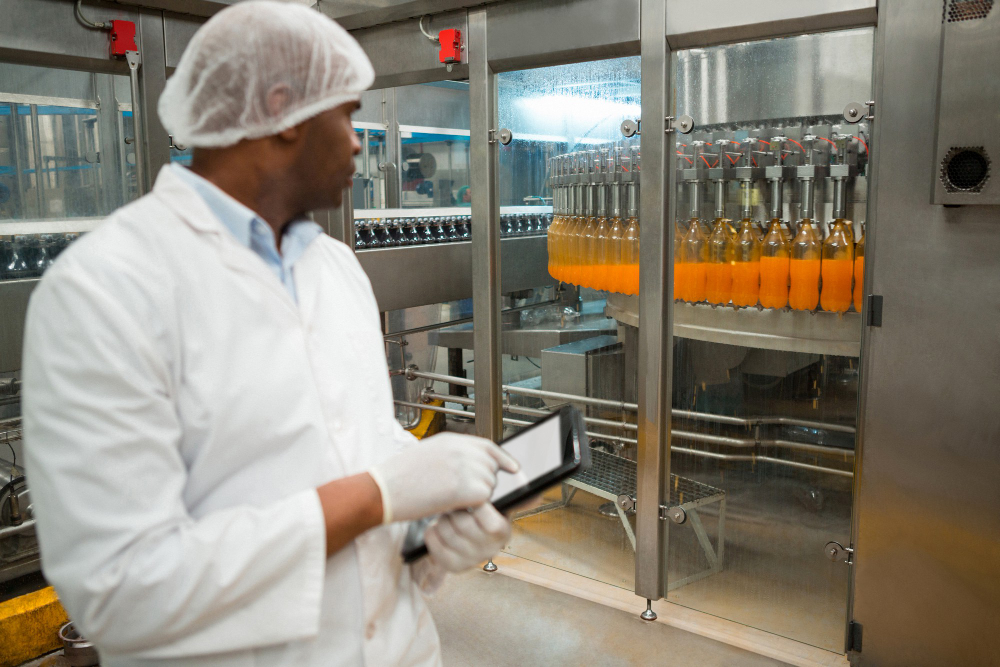
What is Automation?
Food and beverage manufacturing automation uses technology and machines to carry out specific tasks, making the process smoother and less reliant on people. Typically offered in manufacturing consultancy services, it aims to boost efficiency, productivity, and consistency while reducing manual work and mistakes. The International Federation of Robotics reports that about 3.5 million industrial robots are in use globally, with the number growing by over 30% each year since the pandemic.
How Does Automation in Food and Beverage Manufacturing Work?
Food and beverage industry automation is operationalized through advanced programmable devices, systems, and tools—like artificial intelligence (AI), robotics, and computer-controlled machinery. These technologies focus on automating repetitive, labor-intensive, or hazardous tasks, thereby allowing human workers to concentrate on more complex and skill-intensive roles.
By adopting automated systems with food production consultants, businesses can:
- speed up production,
- maintain high-quality products,
- and improve safety standards.
However, before jumping into these advanced technologies, companies must carefully assess how much they’ll grow and save. This helps ensure that their investment truly pays off in the long run.
Want to automate but need to do it on a budget? Read our blog on cost-cutting automation.
How Can Automation Help Solve the Labor Shortage?
Using automation for hard-to-fill tasks helps food manufacturers tackle labor shortages and improve working conditions. Automation addresses staffing gaps, relieves employee burnout, and boosts safety by eliminating monotonous, physically demanding tasks. When machines handle routine jobs, workers can focus on strategies like food safety and quality control. For example, you can choose automation for packaging or sorting while leaving the processing and handling to people.
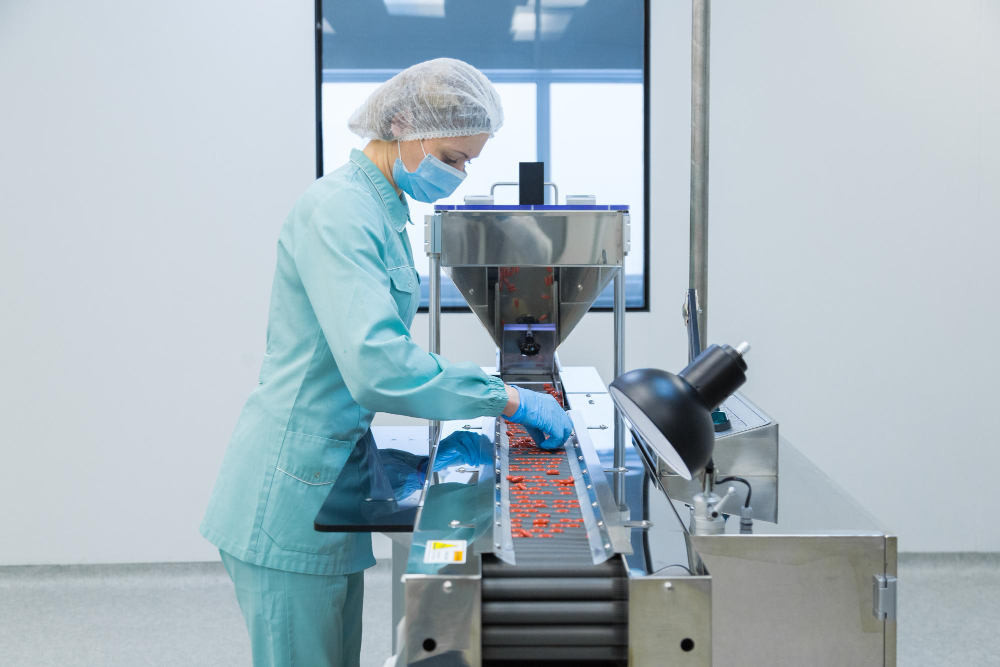
Collaborative Robots (Cobots)
Collaborative robots, or cobots, are designed to work alongside human workers safely. According to a report by Grand View Research, the demand for collaborative robots (cobots) is estimated to grow at a compound annual growth rate (CAGR) of 31.6% from 2025 to 2030. ABB’s SWIFTI cobot, costing around $30,000, can work 24/7 without breaks, performing tasks like picking and sorting small or irregularly shaped objects.
Automated Storage and Retrieval Systems (AS/RS)
AS/RS systems are highly precise and accurate, minimizing waste and boosting output. The global industrial robotic arm market is projected to reach $23.2 billion by 2033. These systems automatically replace and retrieve inventory, streamlining warehouse operations and reducing the need for manual labor.
Delta-Type Robots for Primary Packaging
Delta-type robots are known for their speed and efficiency in pick-and-place applications. Originally designed for a sweets manufacturer, these robots are ideal for picking up food items from a conveyor belt and placing them into trays.
Predictive Maintenance
Predictive maintenance, enabled by sensors and data analytics, allows companies to identify potential issues before they escalate. Automating maintenance, repair, and operations (MRO) lowers costly downtime and ensures machines operate smoothly without constant manual intervention.
Robotics in Distribution Centers
Automation technologies help streamline operations and save time in distribution centers. Software-powered robotic arms can sort and assemble products, prepare orders for delivery, and pack and unpack containers.
2 Food Manufacturers Who Automate
1. Tyson Foods
Tyson Foods has a highly automated chicken plant in Danville, Virginia. This $300 million facility is one of Tyson’s most technologically advanced plants, producing fully-cooked chicken products like nuggets and snacks. The plant features automated case packing lines, high-speed robotic case palletizing units, and wearable armband devices to improve worker safety and productivity.
2. Drake Company
Based in Waynesboro, Virginia, Drake Company specializes in automating the loading process for cylindrical food products like hot dogs and sausages. Their high-performance loading systems can handle up to 1,800 pieces per minute, ensuring flexible packaging options and maximum yields.
Automate with GENEDGE
GENEDGE is no stranger to automation in the food and beverage sphere and every other manufacturing sector. Our food production consultants can help create manufacturing quality systems that:
- Deliver consistent product quality
- Lower time needed for manual inspections
- Lower risk of errors with real-time data analytics
- Immediately identify and correct quality deviations
- Boost output reliability and reduce waste
- Streamline decision-making with actionable insights
- Prioritize maintenance tasks and resource allocation
- Support high-quality product delivery and operational optimization
“Working with GENEDGE in the GoVA Retooling Program has been a great experience. The automated quality control system they helped us design and implement is already showing significant promise in terms of efficiency and cost savings. We’re excited to see how this system will help us drive continued growth.” — Bart Heenan, CEO of Morphix Technologies.