Remember when 3D printers were just a futuristic dream? Well, those days are over! These amazing machines that can build almost anything from scratch are becoming more affordable and accessible for everyone, including small businesses.
As of 2025, people are even able to “print” their own clothes! That’s not science fiction anymore. With 3D printing, you could soon customize everything from the fabric to the fit. No more off-the-rack sizes or limited color choices. The future of fashion could be personalized and printed right in your own home.
In this blog, we’ll unpack how 3D printing is changing the metalworking business and what exciting possibilities lie ahead.
Want to speak directly to a professional? Contact GENEDGE for manufacturing business consulting services.
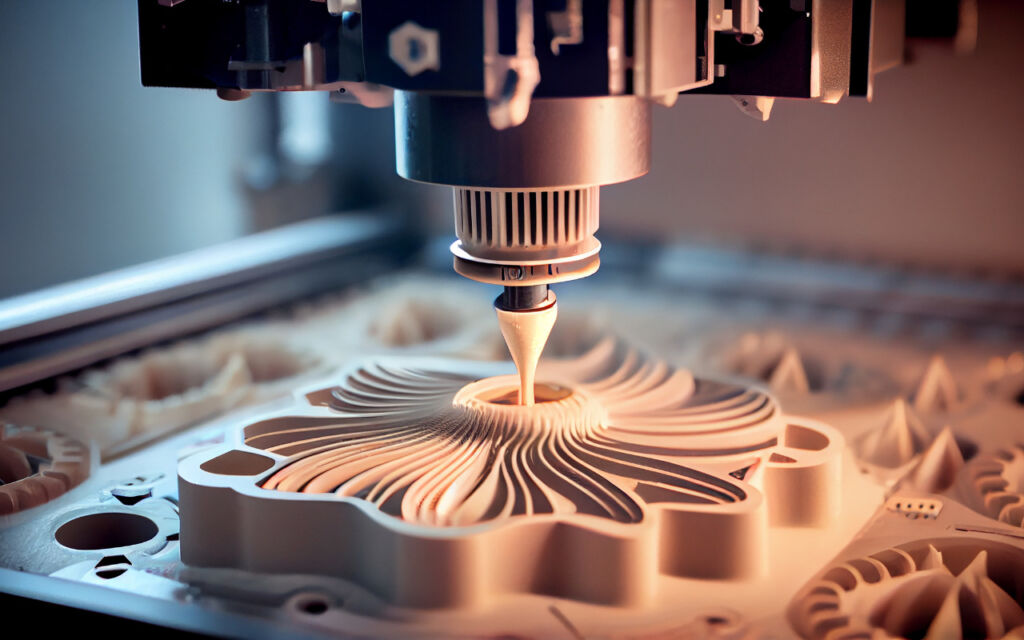
Table of Contents
- What is metal 3D printing?
- Why metal 3D printing works for your wallet
- Challenges and considerations
- A Virginia metalworker who 3D prints
What is metal 3D printing?
3D printing is one of many great growth strategies for manufacturing companies. Imagine you can “print” real things, not just words on paper! That’s essentially what 3D printing in metal does. An Industry 4.0 staple, it uses a special machine to build objects layer by layer, just like stacking tiny blocks. You start with a digital design – a blueprint on a computer – and the printer follows those instructions to create the object.
Think of it this way: Instead of carving something out of a solid block (like a sculptor), 3D printing builds it up from scratch, adding tiny bits of material until the final shape is complete. This allows for incredible flexibility – you can create almost anything your imagination can dream up, from simple shapes to incredibly complex designs.
Check out the other advanced technology metalworkers are using right now!
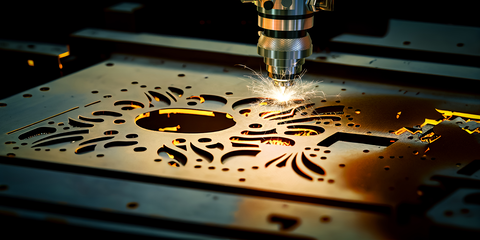
What materials can be used?
You can print with all sorts of things, including:
- Plastics – These are very common and used for many everyday objects.
- Metals – Strong and durable, great for industrial parts.
- Even things like glass, ceramics, and even food!
Why is 3D printing so cool?
- Versatility – You can create almost any shape or geometry.
- Performance – Often uses less material than traditional manufacturing methods.
- Speed – Can often produce objects faster than traditional methods.
This is why metal 3D printing is in-budget for SMEs:
No more expensive molds
Traditional manufacturing often relies on expensive molds and tools to create parts. 3D printing eliminates this upfront cost, saving SMEs a big chunk of money, especially for smaller production runs.
Say goodbye to wasted materials
3D printing uses only the necessary material to create an object, which improves manufacturing operations in Virginia shop floors. This “additive” process minimizes waste compared to traditional methods that often involve cutting away large amounts of material, like carving a sculpture from a block of stone.
Bring production in-house
Instead of outsourcing production, SMEs can bring it in-house with a 3D printer. This eliminates reliance on external manufacturers, cutting down on transportation costs and potential delays.
Prototype faster, cheaper
It stimulate rapid prototyping. This means SMEs can quickly test and refine designs, minimizing the risk of costly mistakes and speeding up the time it takes to bring a product to market.
Easy customization
3D printing makes it easy to customize products. This helps SMEs offer unique and personalized products to customers, increasing customer satisfaction and potentially commanding higher prices.
Challenges to Think About
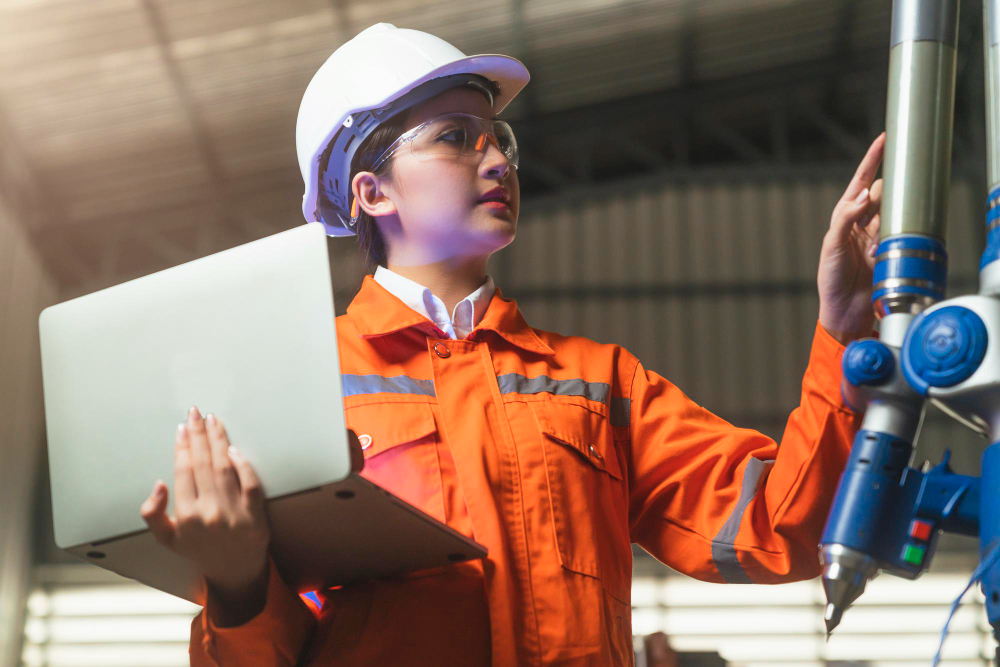
- Expensive to Start: High-quality 3D printers can be very costly.
- Extra Work After Printing: Many 3D-printed metals need extra work like machining or heat treatment, which takes time and money.
- Limited Material Choices: You can’t print with everything, and some metals are expensive.
- Need for Expertise: You or your team need specialized knowledge to use 3D printers effectively.
- Difficult to Scale Up: For large-scale production, metal 3D printing might not be the most cost-effective method.
- Slow Production: 3D printing in metal can be slower than traditional manufacturing.
- Protecting Your Ideas: It can be hard to prevent others from copying your 3D designs.
Virginia Metalworker Spotlight
GENEDGE collaborates with M-Lab to provide a state-of-the-art environment where students and SMEs can explore, design, and prototype using cutting-edge 3D printing technologies. This partnership helps push the boundaries of innovation, solve contemporary problems, and create future job opportunities.
M-Lab’s Role in Promoting Innovation
The M-Lab at Old Dominion University offers a modern collaboration and prototyping space, facilitating technological advancements among students and faculty. It encourages creativity, invention, and interdisciplinary collaboration, focusing on metalworking, woodworking, composites, and welding.
The lab is equipped with advanced tools, including 3D printers and scanners, laser cutters, and relevant software. This environment supports students and SMEs in taking innovative ideas from concept to prototype, fostering a culture of hands-on learning and entrepreneurship.