The machining and metalwork industry faces a large and noticeable skilled labor shortage that impacts productivity and growth. Small businesses feel this pressure more than large corporations and need tangible, practical solutions to flourish.
This blog explores innovative strategies to tackle the skilled labor shortage in the machining and metalwork industry.
To sum it up, we will:
- Identify the impact of labor shortages on industry productivity
- Address challenges faced by small businesses
- Offer practical and creative solutions for growth
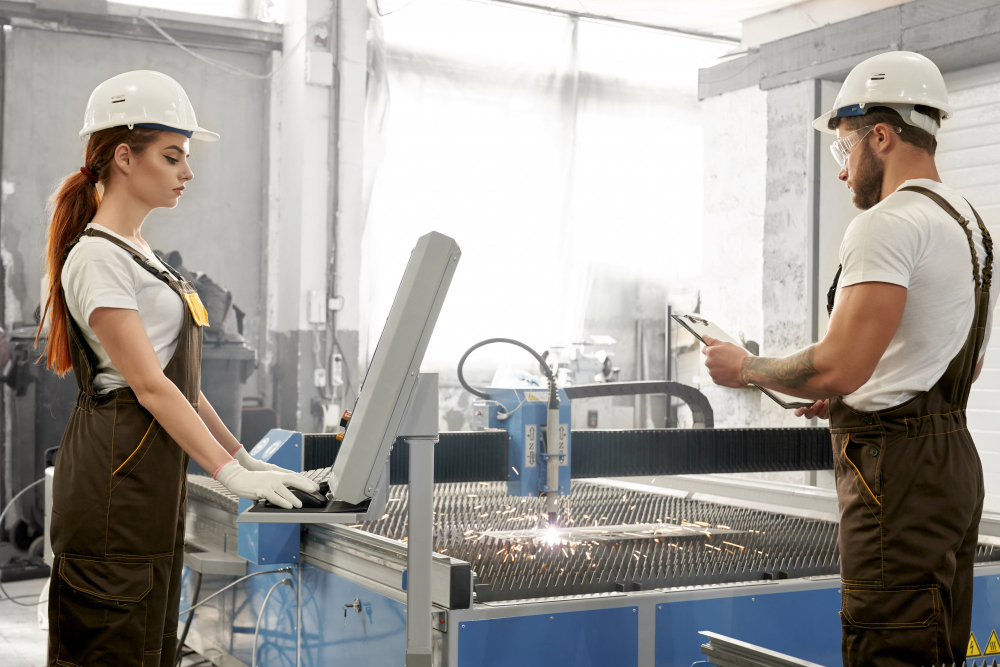
The Impact on Small Businesses
The manufacturing labor shortage hits small companies hard by increasing costs and delaying projects. Owners and HR managers find it difficult to maintain quality and meet demand.
Key Challenges
- Difficulty in finding skilled workers
- Higher wages to attract talent
- Increased training costs
- Strain on existing employees
Solving these challenges requires innovative hiring and training strategies.
Creative Hiring Solutions
1. Technology in Recruitment
Using technology can streamline hiring processes. Many businesses now use AI tools and platforms to find candidates. These tools make it easy to match skills with job requirements.
- Use of online job platforms
- AI-powered candidate matching
- Virtual interviews
Read more about the impact of today’s technology on common manufacturing practices in our past blog.
2. Local Trade Schools and Community Colleges
Build relationships with educational institutions. They supply eager, trainable talent.
- Offer internships for real-world experience
- Host workshops to showcase industry careers
- Collaborate on curriculum development
This ensures a steady pipeline of skilled workers.
3. Apprenticeship and Training Programs
Apprenticeships attract young talent by promoting hands-on learning. They allow businesses to shape the workforce from the ground up.
- Paid learning opportunities
- Dual benefit of education and skill development
- Long-term employment prospects
These programs build loyalty and expertise simultaneously.
Innovative Training Approaches for Existing Employees
Training current staff is vital for adapting to the labor shortage.
Enhance skills with these methods:
Cross-Training to Fill Multiple Roles
Cross-training boosts flexibility and resilience. Employees learn to cover various functions, reducing dependency on specific roles. In addition, incorporating online training manufacturing courses into employee development programs provides flexible learning opportunities and allows employees to “upskill” at their own pace.
- Improved team collaboration
- Increased employee satisfaction
- Reduces impact of absences
- Allows for self-paced upskilling
This maximizes productivity and preparedness.
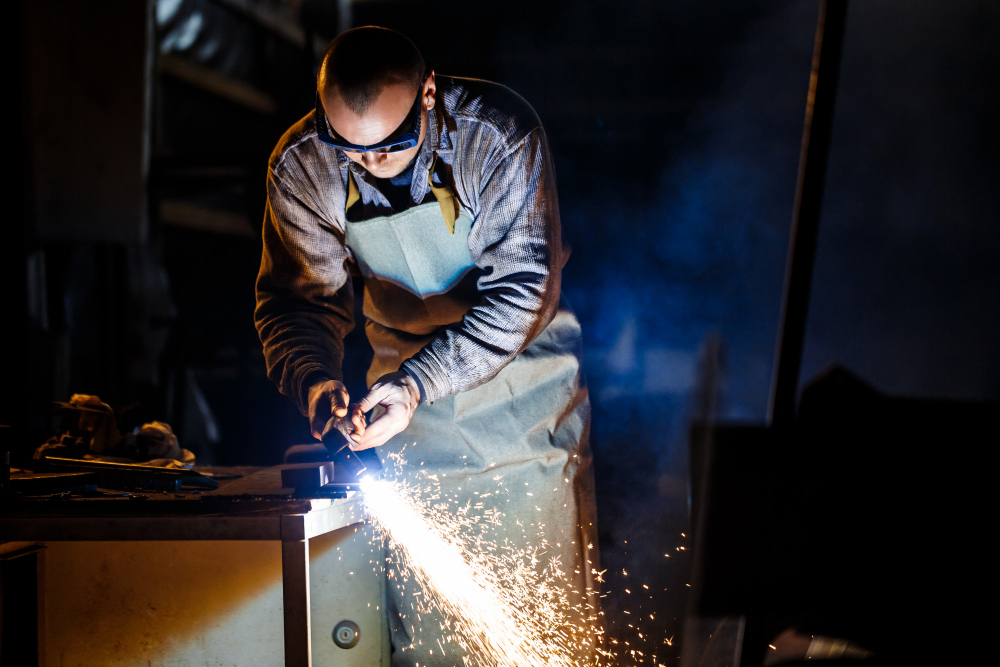
Continuous Learning and Development
Commit to ongoing employee growth. Access to manufacturing workforce development resources is key to getting your team’s morale on the right track.
When employers are committed to employee growth and continuous improvement, it boosts morale by rewarding employees’ hard work and dedication, making them feel recognized and valued.
- Provide online training and resources
- Attend industry conferences and workshops
- Encourage certifications and advanced courses
This approach fosters a culture of continuous improvement.
Embracing Automation and Advancements in Technology
As small manufacturers work to mitigate the effects of the skilled labor shortage, embracing automation and advanced technology is vital. These solutions do not replace workers but complement human capabilities, enhancing productivity and efficiency. Integrating automated systems for repetitive tasks allows businesses to free up workers’ time for more complex and rewarding duties. Smart technology and data analytics can even provide insights into operational efficiencies, allowing for strategic decision-making.
- Implementing Robotics: Robotics can perform tasks that are dull, dangerous, or dirty, allowing the workforce to focus on safer and more intellectual roles.
- Utilizing IoT Devices: Internet of Things (IoT) devices offer real-time monitoring and data collection, improving maintenance scheduling and machine performance.
- Adopting AI for Workflow Optimization: Artificial intelligence can analyze patterns and predict outcomes, promoting smart scheduling and resource allocation.
These technologies require an upfront investment but can drastically reduce operational costs and increase flexibility in the long run.
Next Steps for Small Businesses
Small businesses must adapt to the manufacturing labor shortage. They can thrive in challenging times by implementing creative hiring and training solutions and embracing automation and new technology.
GENEDGE offers invaluable support. Engage with their consultants to refine strategies and strengthen your workforce. Request a consultation to enhance workforce optimization and resilience.